
Checklists
Enjoy our Free Certainty Software inspection checklists available for download
Safety Inspections
Quality Audits
Supply Chain Audits
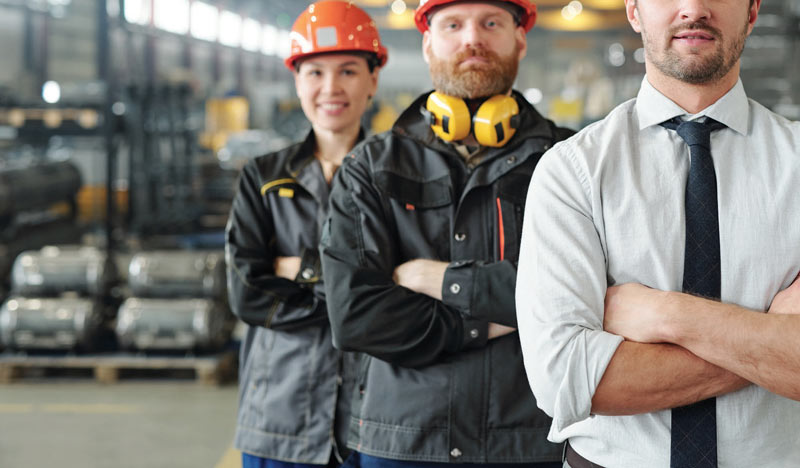
Spend Time On Prevention
Not Paperwork
Watch our overview video to see how your organization can benefit from Certainty.
Watch Video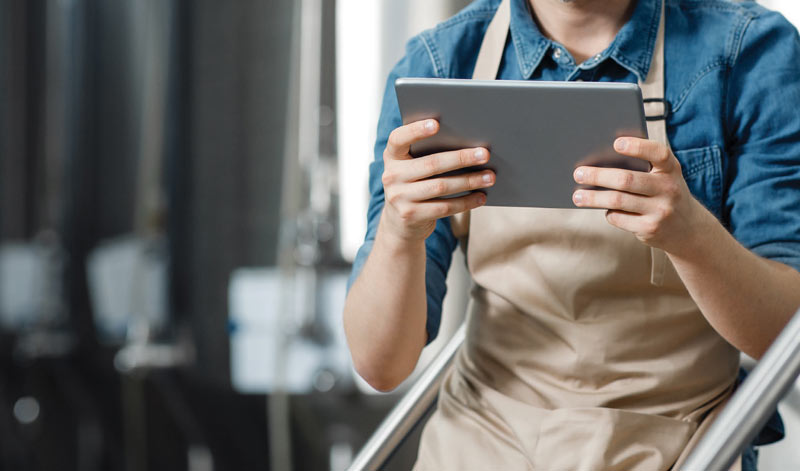