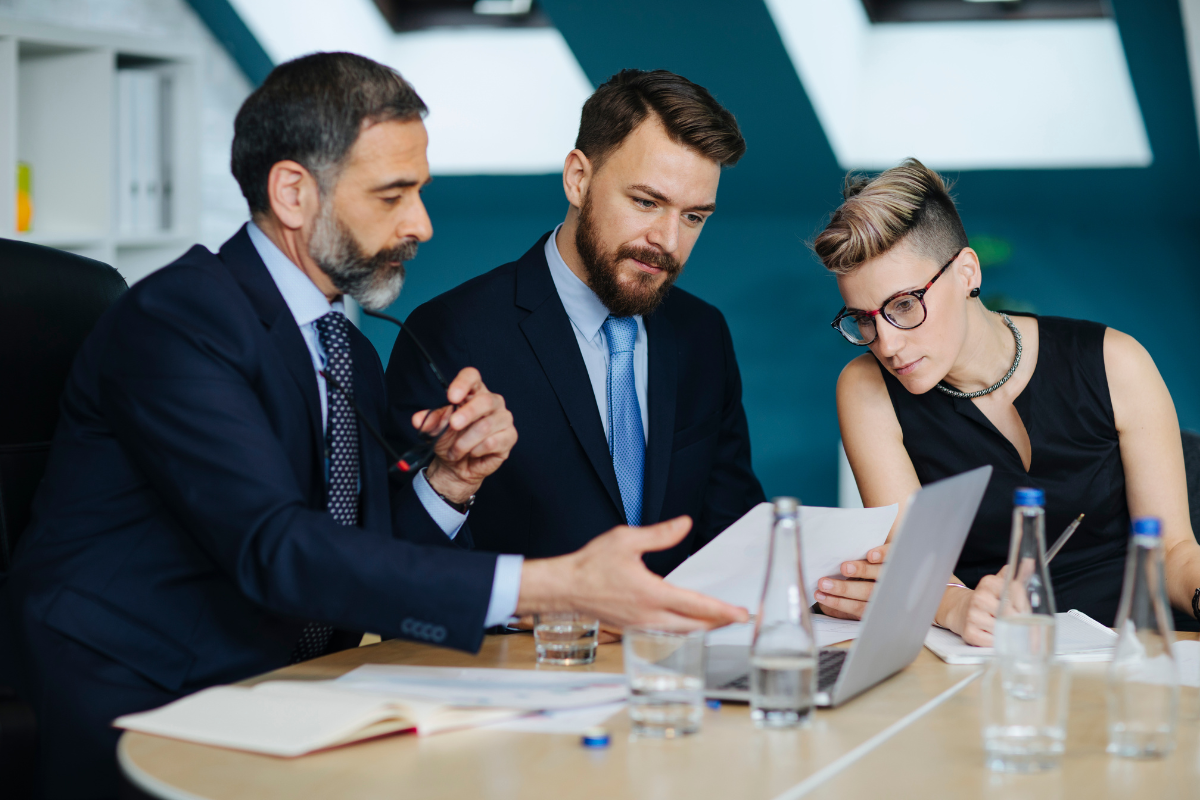
6S Lean
Discover how Certainty Software guarantees the quality stability and compliance of your entire 6S Lean manufacturing process, from Sort to Safety, Certainty is there to help collect, manage, correct, and report your audit and inspections.
The Challenge
Overcoming employee reluctance and fostering acceptance of new practices during 6S Lean adoption.
When implementing 6S Lean practices, organizations frequently face opposition from employees who are familiar with current processes. This opposition can take on different forms, such as pushing beyond employees’ comfort zones, fear of the unknown, perceived threats to job security, and challenges related to cultural norms.
The Solution
Eliminate pushback with a well-aligned digital 6S Lean Management software solution.
Tailored data collection for each and all of the six S’s.
Tailor your data collection process to fit the unique needs of each of the individual S’s in 6S Lean or as a whole. Create customized forms that align with your internal processes and industry standards, ensuring that your audits and inspections cover all essential aspects of 6S Lean Manufacturing. Gather precise data to conduct a thorough audit.
“We can now create our own custom checklists to allow our users to input data from remote sites.“
– Alexis Halenda, Quality Project Auditor/Field Advisor, Strike Group
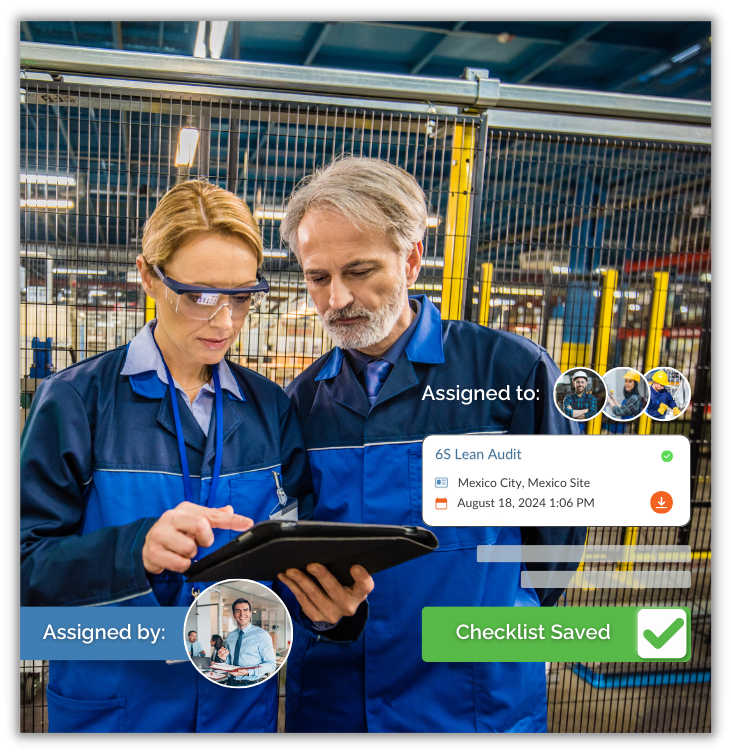
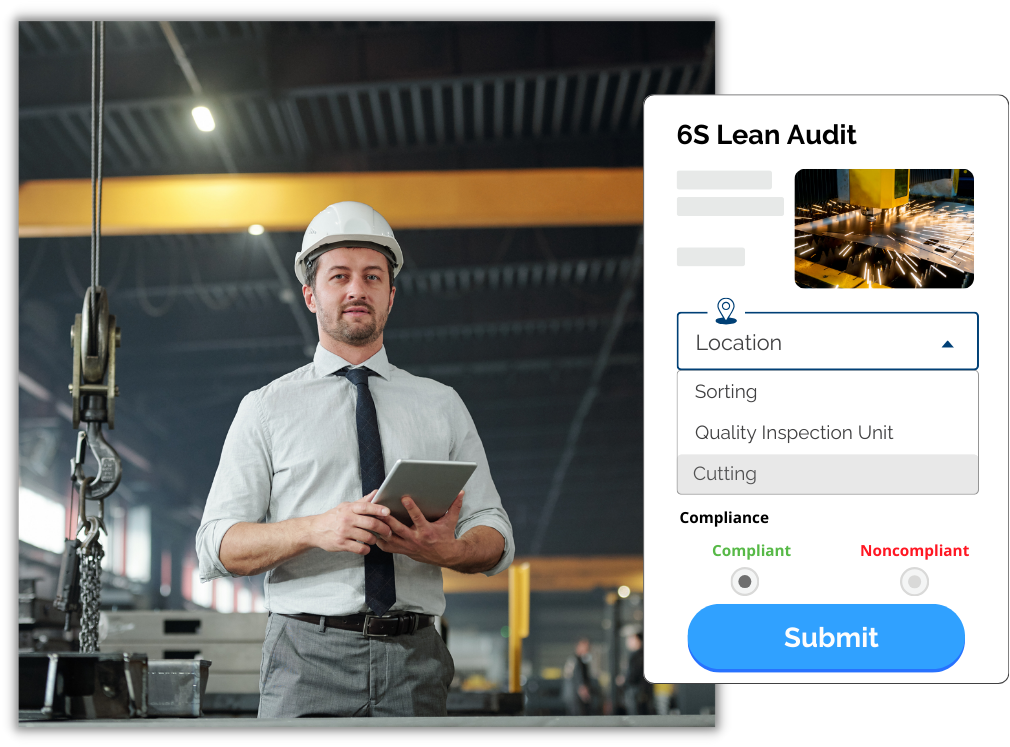
Improve communication in 6S Lean with customizable form inputs.
Empower your team to effectively communicate their 6S Lean audit and inspection findings while ensuring their voices are truly heard.
With a plethora of form input options available, including image and file uploads, document attachments, scale ratings, e-signatures, barcode scanning, and so much more, guarantee that your auditors’ message resonates loud and clear.
“The ease of creating a template and pushing it out to the field is like no other software ever used. Changes can be made and updates performed in a live setting.”
– Ted Luebbert, Training Manager, Goodman Telecom
Enhance inspection management visibility with automated scheduling and reminders.
Ensure consistency in your 6S Lean Management inspections by utilizing dynamic scheduling. Customize your inspection schedule to include both recurring and one-time inspections, assigning specific forms to designated Sites and Users/User Groups. This ensures that inspections are conducted by the appropriate individuals, at the correct time, and in the proper manner.
“With Certainty, we are now able to create multilingual checklists with translations (one checklist in several different languages). It’s been a great addition to our LPA needs.”
– Matthias Jäger, Quality Engineer, Brose
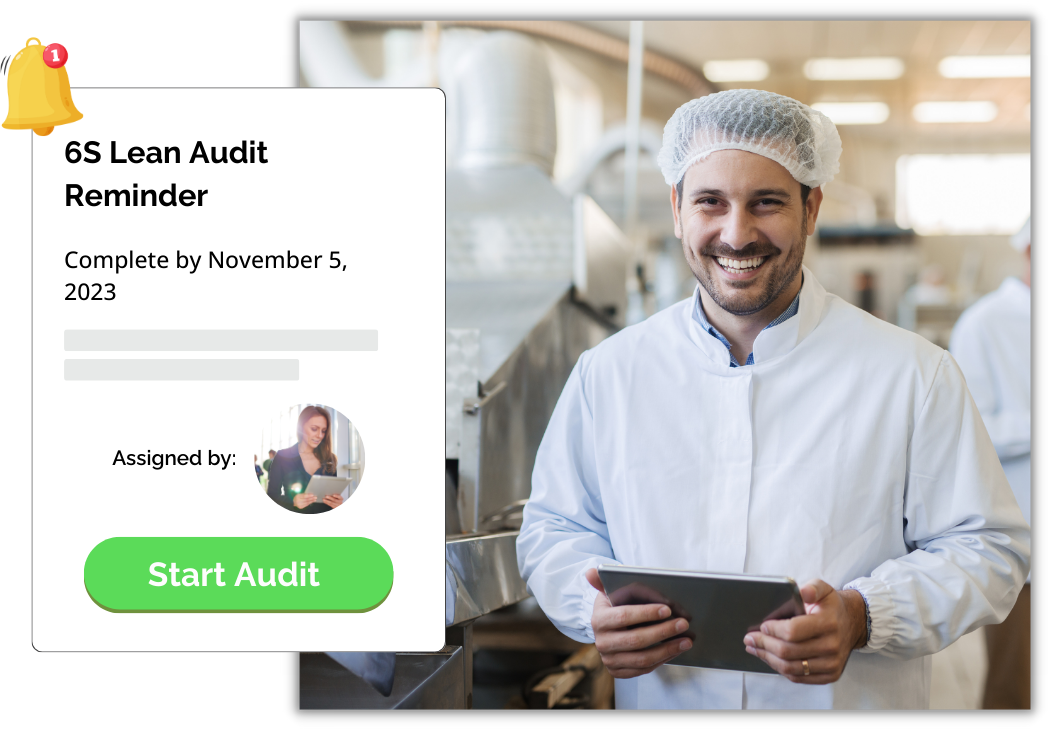
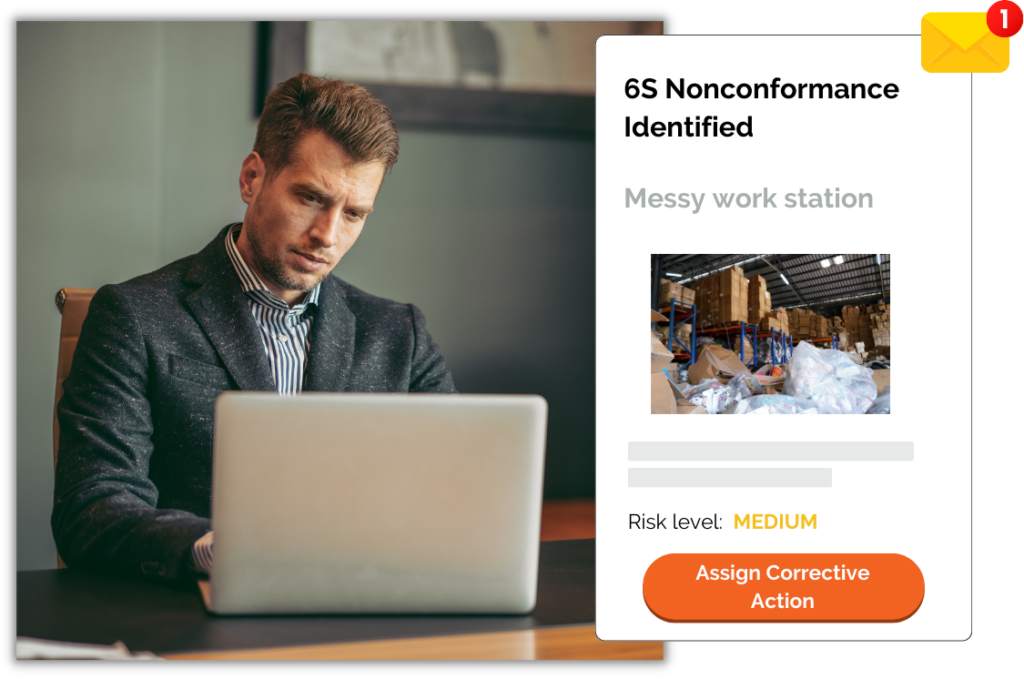
Address any identified issues during inspections promptly to ensure the continuous optimization of our 6S Lean operations.
Maintain operational efficiency and minimize downtime with instant notifications for corrective actions and efficient management. Streamline communication loops and receive immediate alerts for any significant 6S Lean-related risks uncovered during inspections. Respond promptly by implementing tailored corrective measures or establishing a personalized automated workflow for corrective actions.
“We’ve improved our accountability on closing out any areas for improvement throughout all locations accordingly through corrective action functions. The ability of notifications is extremely useful to immediately alert senior management in high-risk situations to quickly resolve any concerns.”
– Daniel Girardi, Continuous Improvement Analyst, Longo’s
Merge intelligent data analysis with interactive reports to enhance visibility.
Ensure that your 6S Lean audit feedback is backed by strong analytical evidence. By leveraging tools like Power BI, System Reports, or crafting custom reports, you can bolster the reliability and depth of your audit insights.
“The great real-time reporting features allow accuracy of completion in our audits. This lets us analyze the data from the checklists completed to see trends and areas that require more focus.”
– Kate Reid, Safety & Security Manager, Longo’s
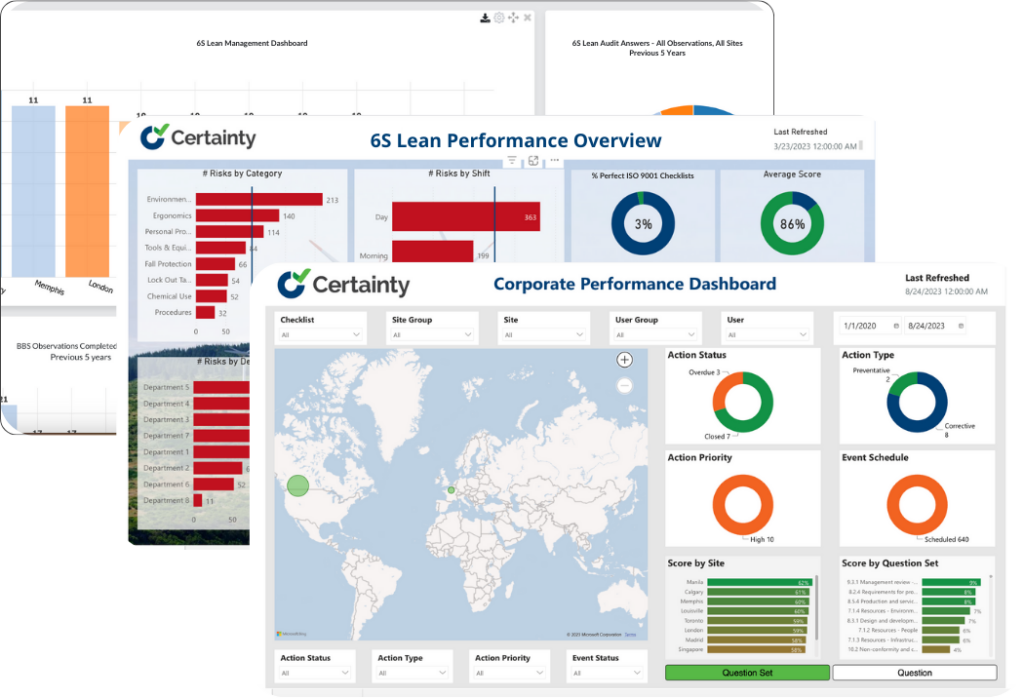
The Features
Tools to Bolster Your 6S Lean Audit Management Efficiency and Accuracy
Collect
- Truly multilingual answer options that include text, radio buttons, drop-downs, checkboxes, a date picker, a signature, a star rating, bar & QR code readers, GPS locations, and more…
- Conditional and repeatable questions to automate and standardize your 6S workflows
- Fill out your forms with photos, graphics, and documents for greater detail and insight
- Collect your audit data both online and offline
- App access through major appl platforms (iOS, Android, Windows)
Report
- Track issues identified in your 6S Lean audits
- Extensive and detailed audit reporting by inspection, user, site, region, question, and answer
- Business Intelligence Analytics
- Configure your dashboard to deliver optimal viewpoints
- Filterable system reporting
- Report data analysis and analysis online, or export to PDF, Excel, or CSV formats.
- Create customized reporting
Manage
- Automated notifications, escalations, and actions
- Centralized action delegation
- Configure your action workflows for continuity
- Sites, organization structures, and site groups that are customizable
- Change history logs for the entire system
- Implement and delegate your custom actions
Used by hundreds of thousands to easily complete millions of accurate audits and inspections annually.
Brose
As a pioneer in technology and a recognized automotive supplier since 1908, Brose is committed to influencing the direction of mobility. Because of the company’s consistent dedication to innovation, quality, and sustainability, top automakers throughout the world view it as a reliable partner. They use Certainty for seamless integration of all LPA process phases into a single system, which removes the need for manual data transfers.
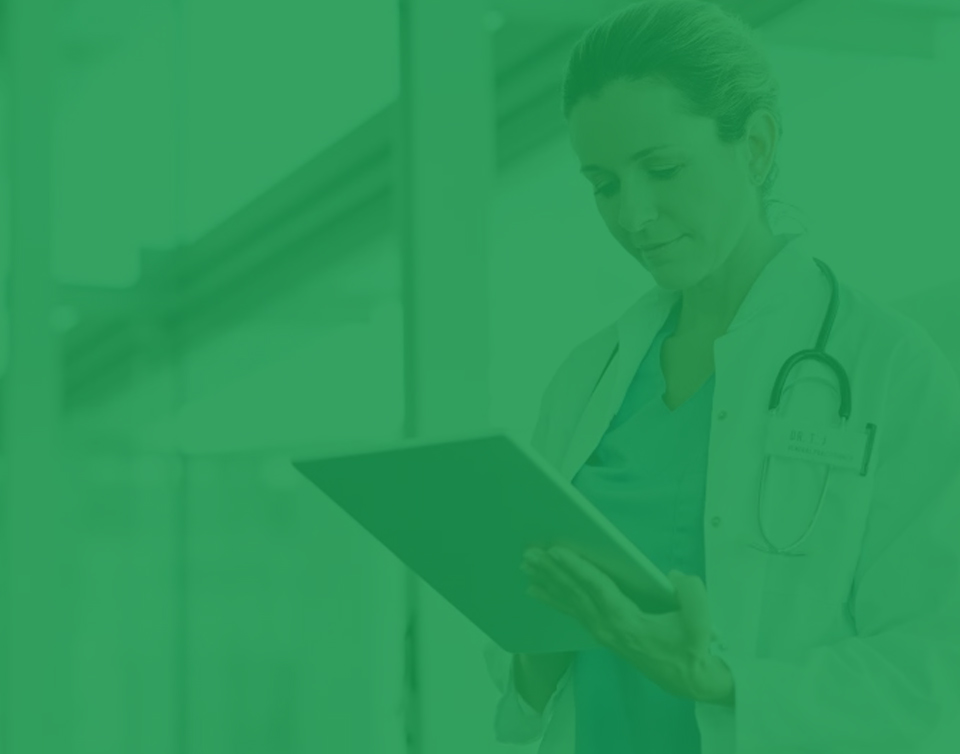