Table of contents
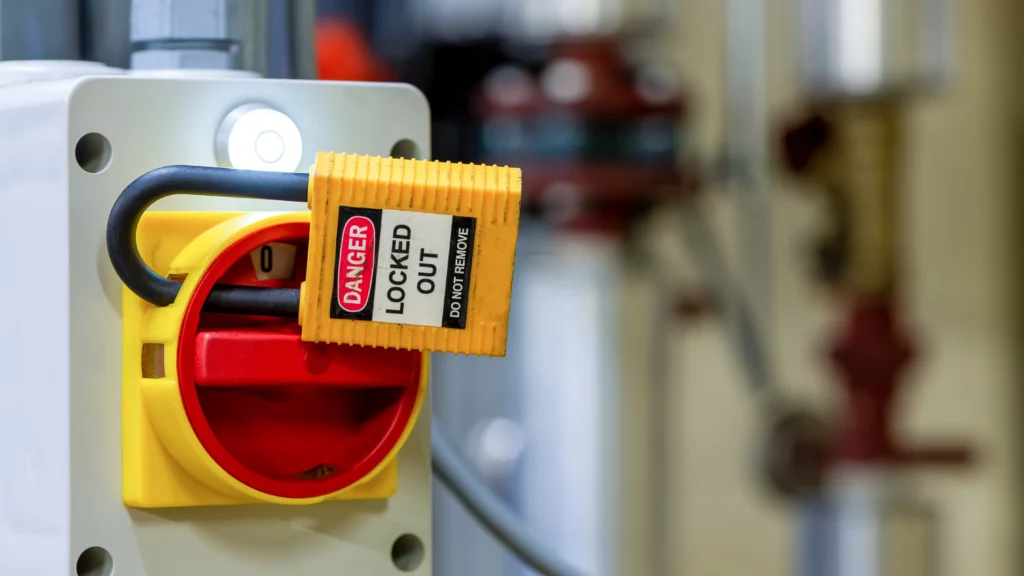
Working with energy-consuming or energy-storing equipment puts you at risk for dangerous energy releases. This is a scenario that could arise where machinery is shut down for maintenance or repair and an unexpected startup may occur. Devastating outcomes are possible, including serious injuries, fatalities, property damage, and environmental devastation.
To prevent such incidents, you must follow a safety procedure called Loto, which stands for lockout tagout. Loto involves isolating and securing the energy sources of the machines or equipment before performing any service or maintenance work. It stops machines or equipment from starting without permission or by mistake.
Loto is not only a good EHS practice but also a legal requirement. OSHA has a rule that requires employers to have lockout/tagout programs which is outlined in 29 CFR 1910.147.
The purpose of these programs is to ensure safety when dealing with dangerous energy sources. These energy sources include electricity, machines, chemicals, heat, and gravity. OSHA estimates that complying with this standard can prevent an average of 120 fatalities and 50,000 injuries yearly.
Benefits of Loto for Workers and Employers
Lockouts and tagouts are vital as they protect workers from the potential release of hazardous energy in machines or equipment starting up without permission.
Most commonly, these risks are brought to fruition during machine/equipment repair or maintenance activities. A proper LOTO program can help your employees avoid injuries like electric shocks, burns, cuts, crushes, falls, explosions, and fires because Loto allows for the control of hazardous energy.
Aside from workplace safety, employees also see benefits by reducing downtime, costs, and liability associated with hazardous stored energy incidents.
By preventing accidents and injuries, LOTO can improve the productivity, efficiency, quality, and morale of workers. Effective implementation can also help employers comply with OSHA regulations and avoid penalties, fines, lawsuits, or reputational damage.
6 Steps of the Loto Procedure
Six fundamental steps make up the energy control procedure of Loto. It’s essential that authorized personnel with the necessary training and credentials that operate or maintain machinery or equipment adhere to these steps.
1. Prepare for shutdown
The authorized employee should notify all affected employees (those who operate or use the machines or equipment) about the planned shutdown and the reason for it.
2. Identify and isolate the power sources
The authorized employee should locate and isolate all the hazardous energy sources (such as electrical outlets, switches, valves, plugs, etc.) that supply power to the machines or equipment. Isolating any stored or residual energy (such as pressure, gravity, springs, capacitors, etc.) is also recommended.
3. Apply locks and tags
Applying a lockout device (such as a padlock, hasp, cable lock, etc.) with a unique key or combination to each energy-isolating device to prevent it from being operated or moved should be followed by the authorized employee.
The authorized employee should also attach a tagout device (such as a tag, label, sign, etc.) to each lockout device to provide the required information, such as the name of the authorized employee, the date and time of the LOTO, and the reasoning. The tagout device should also warn other employees not to operate or remove the lockout device or attempt to start the machines or equipment.
4. Verify a zero energy state
The authorized employee should verify that the machines or equipment are completely de-energized and isolated from all energy sources. It’s important for the individual to test the machines or equipment by trying to operate them using normal controls (such as switches, buttons, levers, etc.).
The worker must use suitable testing tools (like voltmeters and pressure gauges) to check for any stored energy. At this stage, the authorized employee should also check if all testing instruments are working correctly and calibrated before and after use.
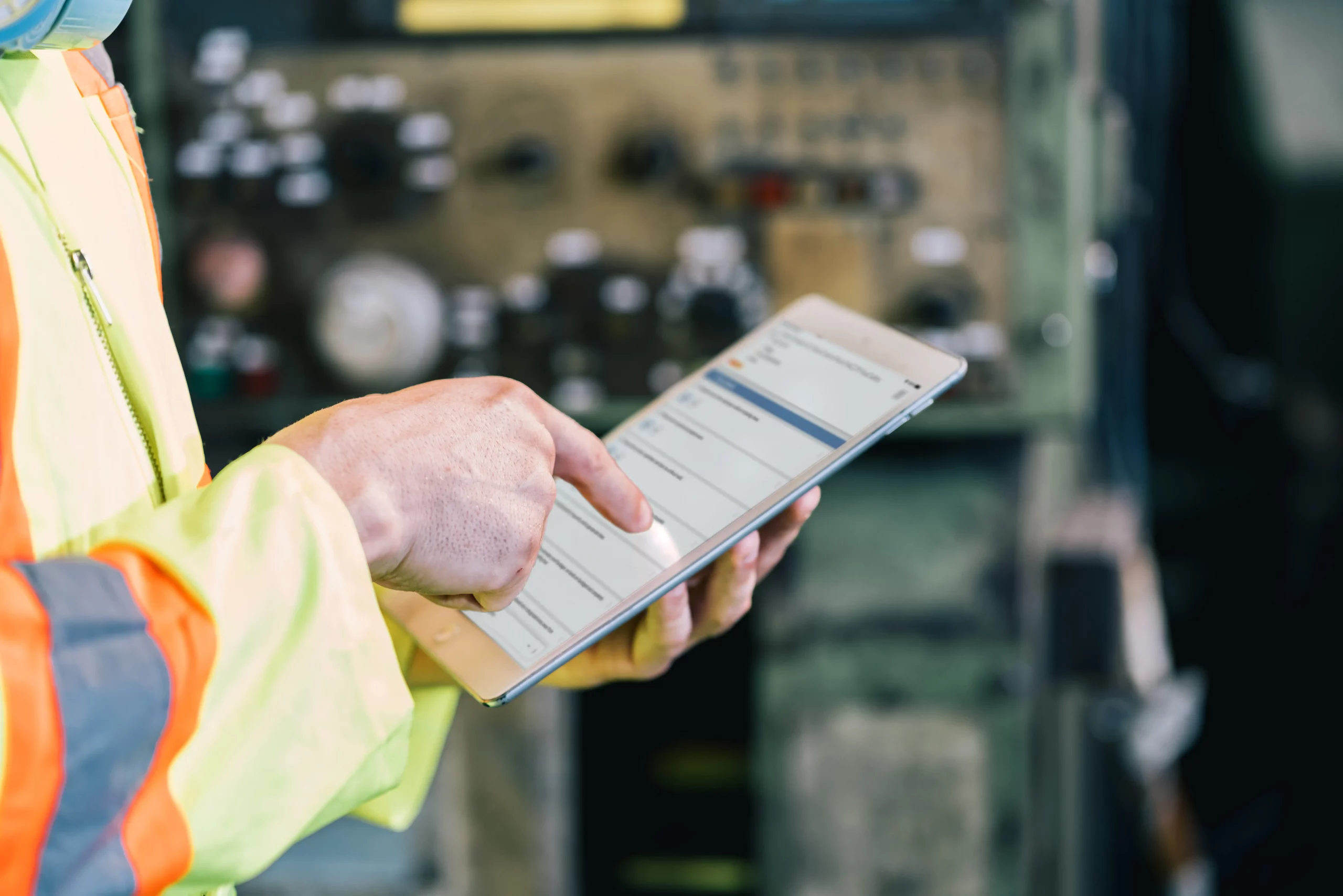
30+ Audit and inspection checklists free for download.
5. Perform the maintenance or repair work
The authorized person can now safely carry out any necessary repairs or maintenance on the piece of equipment. Naturally, the worker must utilize the appropriate tools, gear, and personal protection equipment (PPE) for the task at hand during this phase. The authorized worker must likewise abide by the machine or equipment’s operating manual and procedures. Throughout the task, it is important to keep an eye on the work area and prevent unauthorized individuals from using the equipment.
6. Replace locks and tags and restore normal operation
The authorized worker must verify that the machinery or equipment is safe to use and in working order after finishing the task. It is also necessary to remove any materials, tools, equipment, and debris from the work area.
When the machines or equipment are prepared to be restarted, the authorized employee should inform all impacted employees that the lockout or tagout is back in place. The energy-isolating devices should then have all locks and tags removed and put back in their original locations. To make sure the equipment is operating correctly, it must lastly be inspected and reenergized.
Types of Locks and Tags Used for Loto
Essential components of LOTO are locks and tags. These not only offer information and warnings but also stop energy-isolating devices from being operated unintentionally or illegally. For various energy sources and isolating devices, there are many lockout/tagout device types available. Among them are:
Padlocks
These are movable locks that can be used to secure energy-isolating components like switches, valves, plugs, and other items. They can be fastened to hasps, chains, cables, or other objects. Padlocks ought to be secured with a special key or combination that can only be obtained by the authorized worker who installed them.
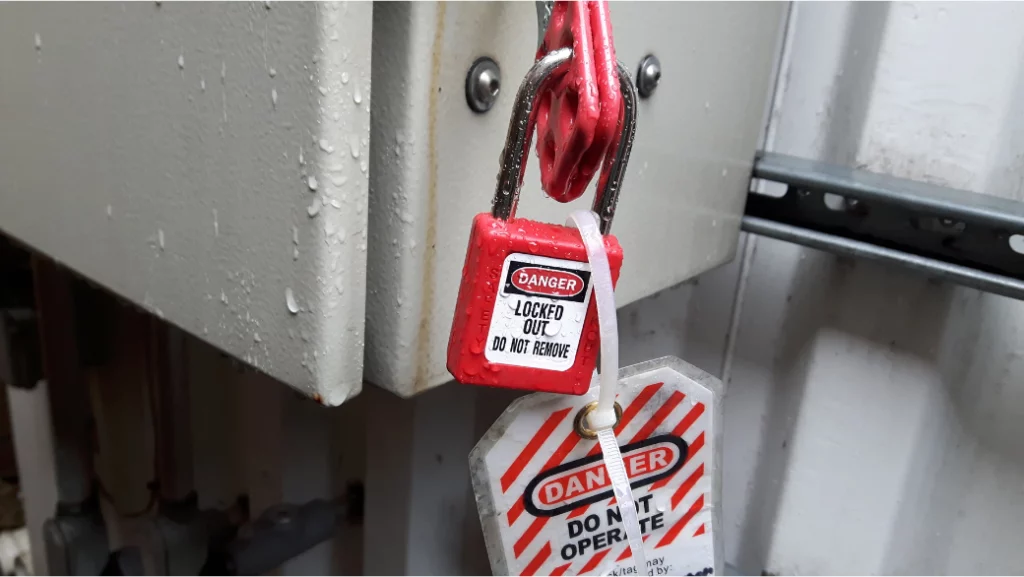
Hasps
Hasps can be fastened to plugs, switches, valves, and other energy-isolating devices. These can hold padlocks or other lockout mechanisms since they contain one or more holes in them. Hasps ought to be constructed from sturdy, non-conductive materials.
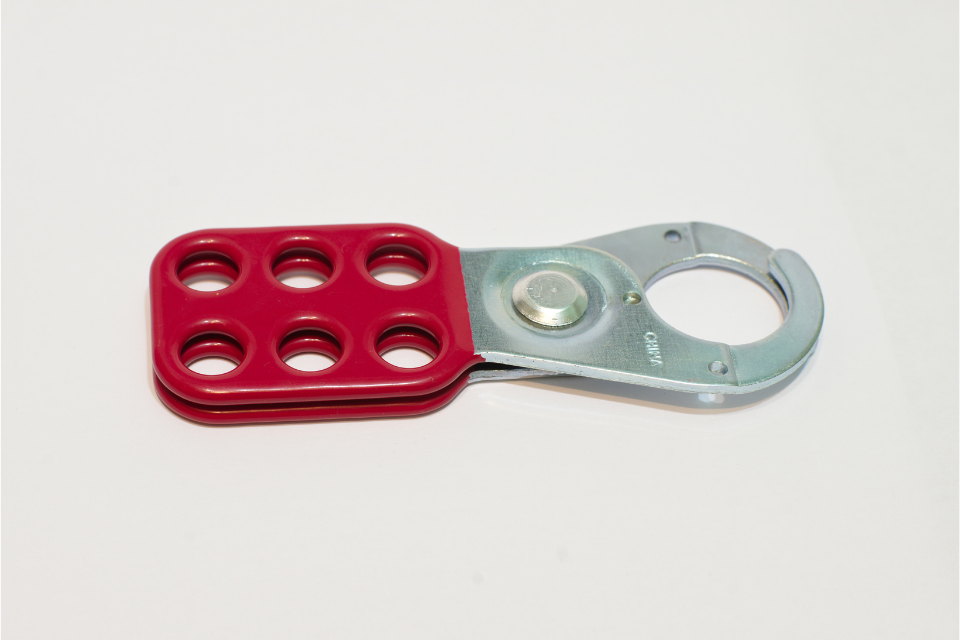
Cable Locks
Cable locks are suitable for wrapping around energy-isolating components like levers, pipelines, valves, etc. A padlock or other lockout tool can be used to secure the locking mechanism of cable locks. Durable and non-conductive materials ought to be used to make cable locks.
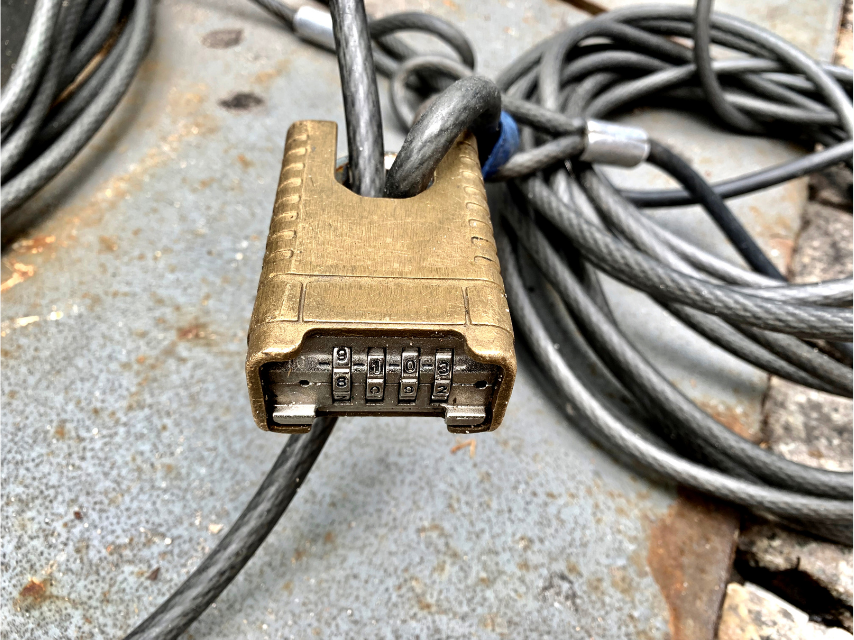
Valve Covers
Valve covers are attachments for valves and other handle or stem-equipped energy-isolating devices. A padlock or other lockout tool can be used to secure the locking mechanism on valve covers. The materials used to make valve covers should be stiff and non-conductive, and they should fit tightly over the handles or valves.
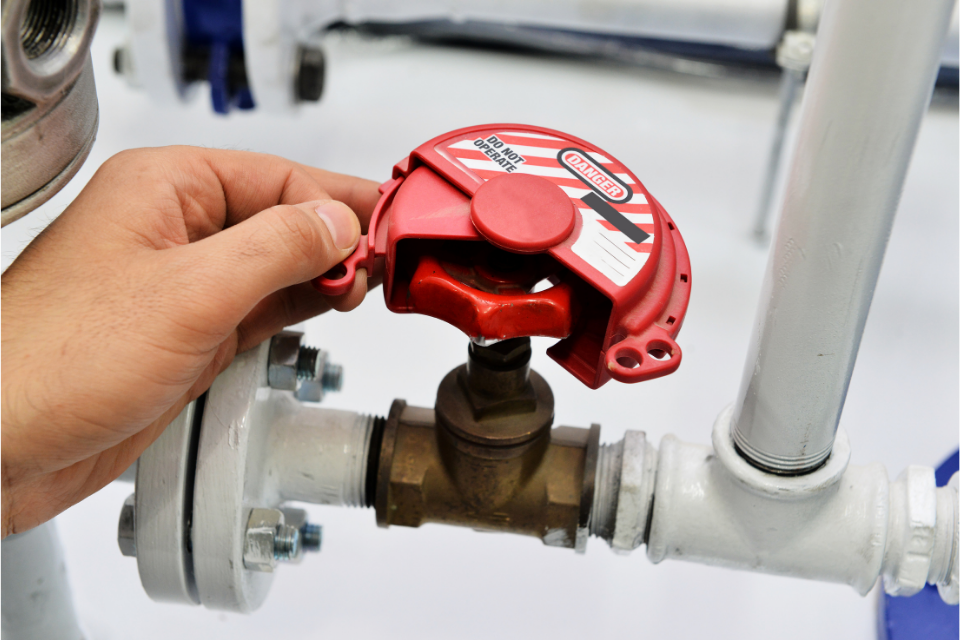
Circuit Breakers
Circuit breakers are attachment-compatible devices that can be connected to other electrical energy-isolating devices or electrical circuits. A padlock or other lockout tool can be used to secure the locking mechanism on circuit breakers. It is recommended that circuit breakers be constructed from non-conductive materials and that they cannot be turned on or off.
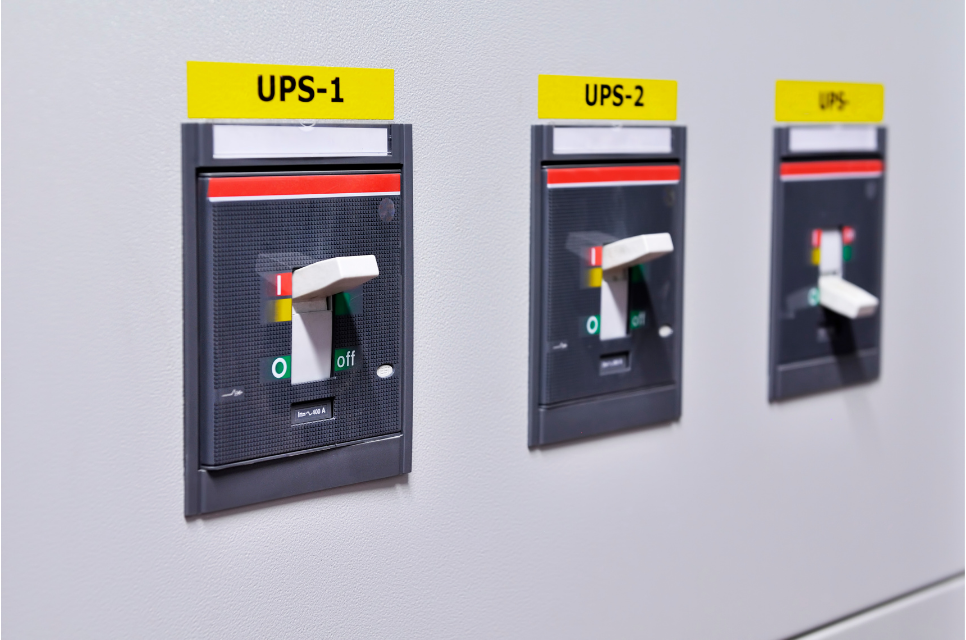
Warning Signs & Labels
Warning signs and labels’ purposes are to provide information and warning about the LOTO. They should be visible, legible, and durable and should include the name of the authorized employee, the date and time of the LOTO, and the reasoning.
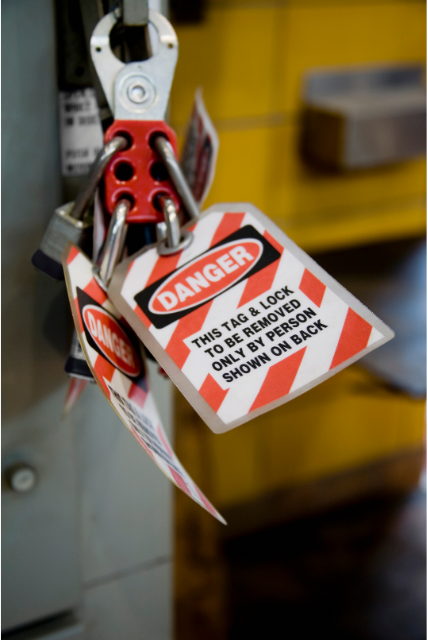
Roles and Responsibilities of Employees Involved in LOTO
There are different roles and responsibilities for employees involved in LOTO. This depends on their level of authority and involvement in the service or maintenance work. These roles are:
Authorized employees: These workers are qualified and trained to apply and remove lockout/tagout devices as well as do maintenance or repair work on machinery or equipment. When working, authorized personnel are in charge of adhering to the established protocols and making sure everyone else and themselves are safe.
Affected employees: These are employees who operate or use the machines or equipment that are subject to LOTO. Affected employees are responsible for complying with the LOTO procedures and not interfering with the devices or attempting to start the machines.
Other employees: These are employees who work in areas where LOTO is performed but are not directly involved in the service or maintenance work. Other employees are responsible for being aware of the LOTO procedures and not interfering with the LOTO devices or attempting to start the machines or equipment during work.
Common Mistakes and Challenges of LOTO Implementation
Loto is a critical safety procedure that requires careful planning, execution, and monitoring. However, there are some common mistakes and challenges that can compromise the effectiveness and compliance of LOTO. Some examples are:
Lack of training: Workers may not be aware of the risks and dangers associated with servicing or maintenance tasks if they have not received enough training on LOTO procedures and equipment. They can also be unaware of the proper and safe methods for applying and removing the LOTO devices.
Lack of communication: It’s possible that staff members who aren’t told or alerted about LOTO operations are unaware of the location and condition of the machinery or equipment that falls under this category. They can also be unaware of who has the authority and accountability for the LOTO and the task.
Lack of coordination: Workers may not apply and remove the LOTO devices in the same order or at the same time if they are not coordinated or synced with one another during the LOTO activities. Additionally, they might fail to attest to the machines’ or equipment’s zero energy state both before and after the work is done.
Lack of compliance: Employees who do not follow or adhere to the LOTO procedures and devices may not isolate and secure all the energy sources of the machines or equipment. They may also not apply and remove the LOTO devices properly and completely.
Lack of documentation: Employees who do not document or record the LOTO activities may not have a clear and accurate record of who, what, when, where, why, and how the LOTO was performed. They may also not have proof or evidence of compliance with the OSHA standard and other regulations.
Best Practices and Tips for Effective LOTO Management
Loto is a vital safety procedure that requires continuous improvement and optimization. There are some best practices and tips that can help employers and employees manage LOTO effectively and efficiently. Some examples are:
- Conduct regular audits, inspections, reviews, and updates of LOTO policies and procedures. This is to ensure they are current, relevant, and compliant with the OSHA standard and other regulations.
- Provide adequate training, education, and awareness to all employees involved in LOTO. They should be trained on the hazards, risks, procedures, devices, roles, responsibilities, and expectations of lockouts and tagouts.
- Establish clear and consistent communication channels and methods among all employees involved in LOTO. This verifies that they are informed, notified, coordinated, synchronized, verified, confirmed, and documented during the LOTO activities.
- Use appropriate and standardized LOTO devices that are durable, non-conductive, and identifiable for different types of energy sources and isolating devices.
- Install a LOTO system for complicated or numerous machinery or pieces of equipment when servicing or maintenance requires the participation of multiple authorized personnel. In a grouped system, the keys or combinations to each of the individual LOTO devices might be stored and secured using a lock box or a multi-lock hasp.
- To guarantee that nobody else can access or tamper with a LOTO device and that only the authorized person who applied it may remove it, enforce a stringent accountability and responsibility framework.
How Certainty Helps in LOTO Safety
Certainty provides you with various checklists that you can use to self-inspect or audit your current LOTO practices, such as:
- Facility Safety Inspection Checklist
- Jobsite Safety Inspection Checklist
- Warehouse Safety Inspection Checklist
- Behavioral Based Safety Observation Checklist
- Hot Work Permit Checklist
By using Certainty and its checklists, you can ensure that your LOTO program is up-to-date, relevant, and compliant with OSHA standards and other regulations. You can also identify areas of improvement and opportunities for enhancing your safety performance.