Table of contents
According to recent survey data, 68% of staff say they don’t feel completely safe at work. Reasons vary — some are worried about risks to their health from airborne contaminants or caustic materials, and others are concerned about environmental issues such as working conditions and procedural risks. Still, others point to safety concerns around current operations that could put their lives and livelihoods at risk.
The result? Businesses need to prioritize end-to-end safety efforts that help reduce total risk and address staff concerns. This starts with EHS.
What Does EHS Stand For?
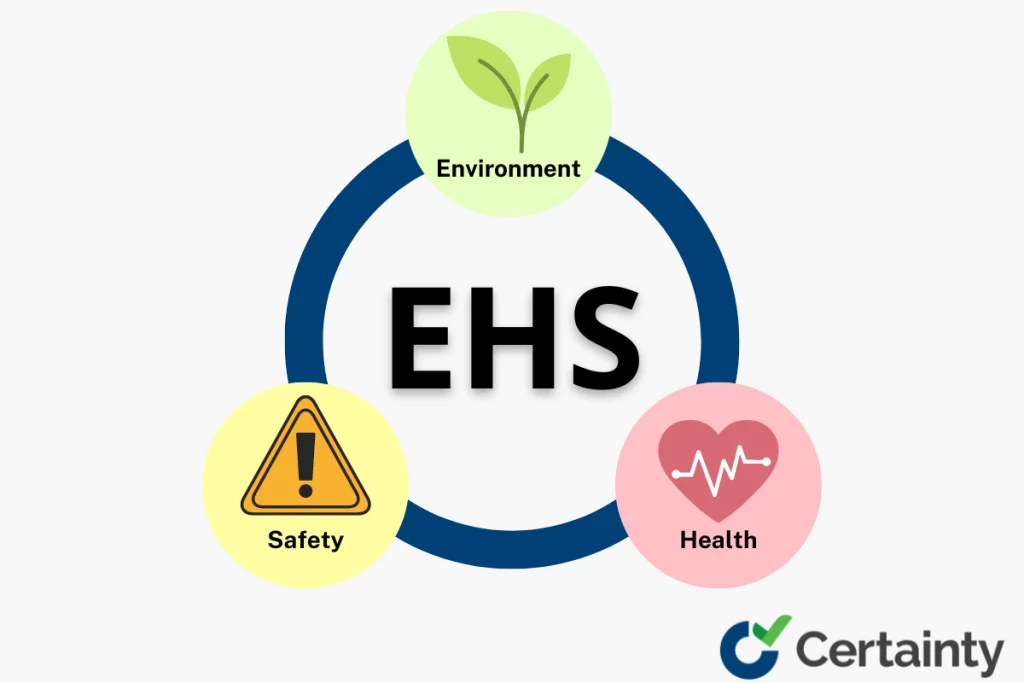
EHS stands for environment, health, and safety, It may also be written as EH&S, or HSE, and may sometimes include a “Q” for quality. No matter the form, however, the function remains the same: To help companies quantify and address potential workplace risks. Let’s break down each component in more detail:
Environment
Environment refers to potential hazards in the workplace such as chemical spills, poor ventilation, or the risk of fire due to current operational practices.
Health
Health speaks to the risk of illness due to hazardous materials pathogens, caustic chemical emissions, or exposure to extremely loud noises or bright lights that could damage hearing or vision. It also speaks to overall employee well-being at work.
Safety
Safety management focuses on the potential for workplace injuries due to malfunctioning or damaged equipment or the lack of available personal protective equipment (PPE). It also looks at current safety training and safety programs to ensure they are effective in creating a robust safety culture.
Why is EHS Important?
EHS management plays an important role in the Occupational Safety and Health Administration’s (OSHA) efforts to create safer workplaces. These efforts are also critical in reducing the number of staff injuries and illnesses, in turn keeping more of the workforce on the job and improving overall production.
Robust environmental health and safety policies also help address the concern mentioned at the beginning of this piece: That staff doesn’t always feel safe at work. By creating EHS plans and regularly reviewing them to ensure they’re working as intended, companies can provide peace of mind for staff.
3 Quick Tips for Managing EHS Compliance
Depending on where businesses are located, they could be subject to multiple levels of EHS regulations from differing regulatory agencies. For example, states each have their own EHS requirements — in New York, for example, companies with more than 100 employees must track and report any potential exposures to dangerous compounds or chemicals. Federal OSHA guidelines may also apply, and companies may be subject to compliance rules set out by industry associations.
No matter the nature of EHS requirements, however, there are common ways to help manage compliance, such as:
- Schedule regular evaluations
First, it’s critical to schedule regular EHS audits to help pinpoint where potential problems exist and address workplace safety concerns as they evolve. Here’s why: While initial EHS plans can help reduce immediate risk, both business operations and compliance rules change over time, meaning regular evaluation is required to keep policies relevant.
- Use digital checklists
When it comes to evaluating components of an EHS program — such as compliance with ISO 14001 & ISO 45001 guidelines — digital checklists can help reduce the amount of time required and improve overall accuracy. While paper-based checklists are still used by many organizations, they come with the risk of missing or inaccurate data, which could in turn negatively impact EHS efforts. Digital options for behavioral-based safety observation checklists and hazard evaluations, meanwhile, both reduce the time required to complete audits and help create a digital repository of data that companies can use to evaluate EHS trends.
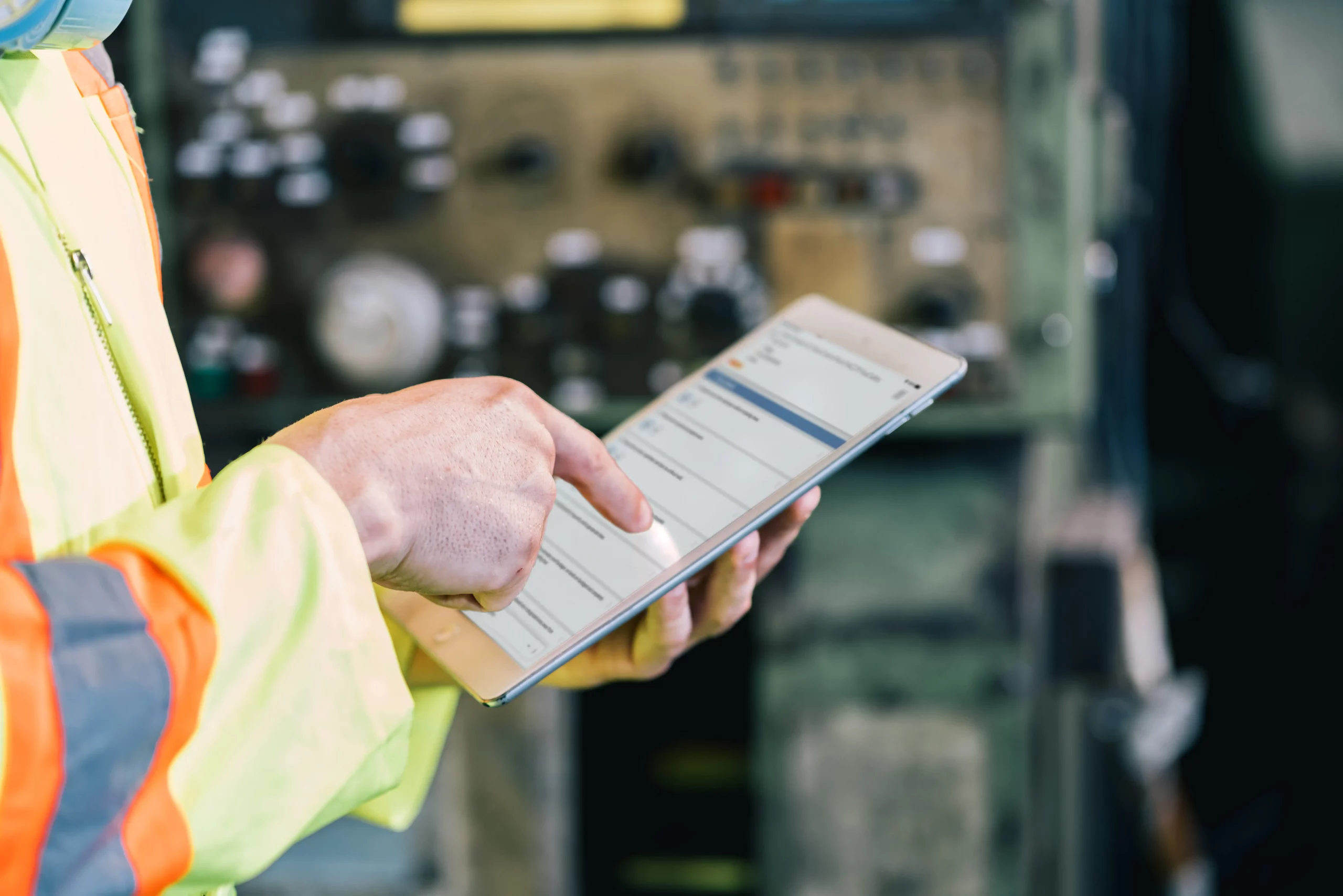
30+ Audit and inspection checklists free for download.
- Create a plan of action
Finally, organizations need to create a plan of action that addresses top-priority EHS issues and implements safety regulations. For example, if EHS audits determine that essential machinery is at risk of breakdowns which could put employees’ safety at risk, companies can make repair or replacement a priority. If current worksites include health hazards such as extremely loud noises, businesses can invest in better PPE or look for ways to reduce the frequency or intensity of this noise
Bottom line? EHS programs are critical to improving safety and enhancing risk management in the work environment. Regular audits combined with digital checklists and clear action plans can help companies stay compliant.
You may also be interested in:
The Differences Between OSHA 301, 300, and 300a