Table of contents
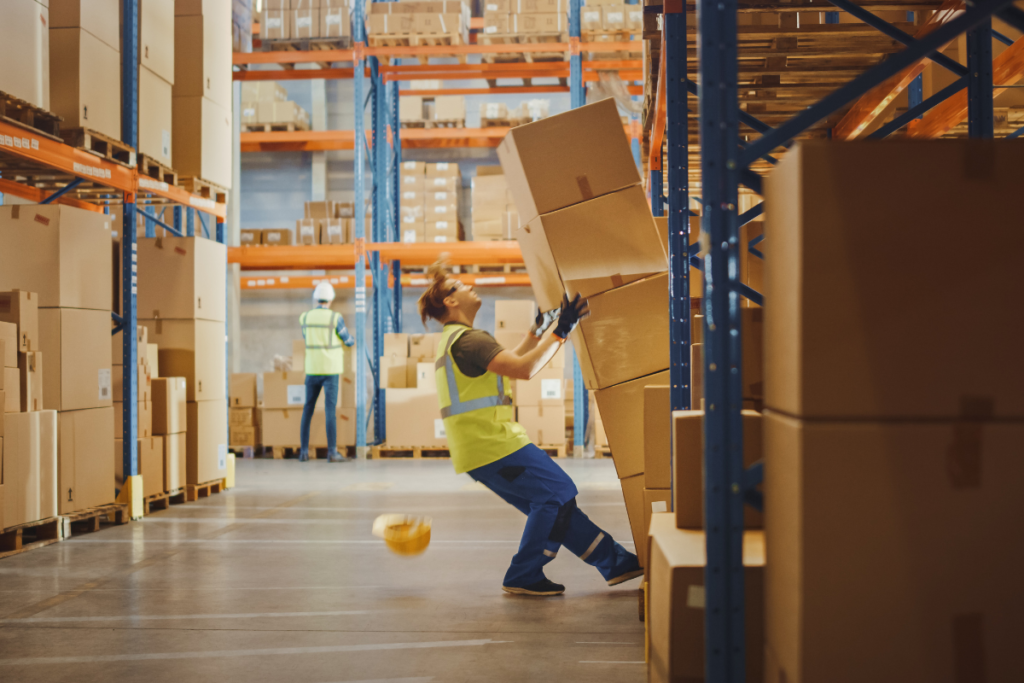
What is a Near Miss Event?
Near miss events are situations where an accident or injury was narrowly avoided, but could have happened under slightly different circumstances. They are also known as close calls, near hits, or near accidents. Near miss events are common in the work environment. According to the Accident Triangle, for every serious workplace accident, there were 60 near miss events. These events can occur in any setting or industry, but they are often underreported or ignored. However, near miss events can provide valuable insights into potential hazards and risks that exist in the workplace, and how to prevent them.
Types of Workplace Near Miss Events
Understanding the most common workplace hazards that can lead to a near miss event is essential in helping you to narrow your focus on addressing potential unsafe acts, or conditions in your work environment. Some of the common types of workplace near miss events are:
Slips, trips, and falls
These occur when a worker or a bystander slips, trips, or falls but does not suffer any injury or damage.
Example: A worker was carrying a heavy load of metal parts across the factory floor. He did not notice a puddle of oil that had leaked from a nearby machine. He stepped on the oil and slipped, losing his balance and dropping the load. Fortunately, he was wearing steel-toed boots and gloves, and no one else was nearby. He managed to avoid injury and damage to the equipment.
Struck by or against
When a worker or a bystander is struck by or against an object or a person but does not sustain any injury or damage, this type of near miss event happens.
Example: A worker was using a saw to cut a wooden plank. He did not see a nail on the plank. The nail hit the saw blade and flew off. It almost hit his head but the worker was not hurt.
Caught in or between
This type of near miss event involves a worker or a bystander being caught in or between two objects or forces but not suffering any injury or damage.
Example: A worker was loading a pallet of boxes onto a truck using a forklift. She was wearing a safety vest and a hard hat. She did not notice that another worker was standing behind the truck, checking his phone. As she was backing up the forklift, she almost hit the other worker, who jumped out of the way at the last second.
Ergonomic near miss events
This type of near miss event happens when a worker or a bystander is exposed to an ergonomic hazard or a risk that could have resulted in a musculoskeletal disorder, such as sprain, strain, or inflammation.
Example: A worker was typing on a computer keyboard for several hours. Unfortunately, she was sitting on a chair that was too low and had no back support, and did not have a wrist rest or an adjustable monitor. She began to feel pain and stiffness in her neck, shoulders, and wrists; but she ignored the pain and continued working. Fortunately, she took a break and stretched her muscles and didn’t develop an MSD.
Exposure to harmful substances
This type of near miss event happens when a worker or a bystander is exposed to a harmful substance but does not experience any adverse health effects.
Example: A worker was cleaning a laboratory bench with a disinfectant solution. He was wearing gloves and a lab coat, but not goggles or a mask. He did not notice that the bottle of disinfectant had a small crack and was leaking. Suddenly, some of the solutions splashed on his face and eyes. He felt a burning sensation and ran to the eyewash station where he rinsed his eyes for 15 minutes and did not suffer any permanent damage.
According to the National Safety Council (NSC), worker exposure to harmful substances was the leading cause of days away from work in the US workforce in 2020.
Electrical near miss events
When a worker or a bystander is exposed to an electrical hazard or a risk that could have resulted in an electric shock, burn, or fire, this type of near miss event occurs.
Example: A worker was installing a new light fixture in a ceiling. He was wearing insulated gloves and boots, but not goggles or a hard hat. The worker, unfortunately, did not check if the power was turned off before cutting the wires and accidentally touched a live wire and felt a jolt of electricity. He dropped the wire and stepped back but was not injured.
Fire near miss events
These occur when a worker or a bystander is exposed to a fire hazard or a risk that could have resulted in a fire, explosion, or smoke inhalation.
Example: A worker was welding a metal pipe in a workshop. He was wearing a welding mask, gloves, and apron, but not a fire-resistant suit. He did not check if there were any flammable materials nearby and ignited a spark that flew into a pile of oily rags and paper. The rags and paper caught fire and produced thick smoke. He smelled the smoke and saw the flames, grabbed a fire extinguisher, and put out the fire.
Causing Factors
Each type of workplace near miss event has its own patterns and risk factors that can be identified and analyzed to prevent future occurrences. The factors that contribute to a workplace near miss events are:
Human factors: These are related to the behavior, attitude, skill, knowledge, or performance of the workers involved in the near miss event. For example, lack of attention, fatigue, stress, distraction, complacency, or poor judgment.
Environmental factors: This pertains to any unsafe conditions of the workplace where the near miss event occurred. For example, poor lighting, noise, temperature, weather, or ventilation.
Organizational factors: These are factors related to the policies, procedures, culture, or management of the workplace where the near miss event occurred. For example, lack of training, supervision, communication, feedback, or incentives.
Prevention Strategies for Workplace Near Miss Events
Here are some recommended best practices to implement in your safety programs that will help prevent near miss events from occurring, and mitigate them from becoming serious injuries.
Hazard identification: Identify and eliminate or control the sources of potential harm or danger in the workplace. For example, conducting regular inspections and audits using Certainty’s Near Miss Checklist and tools involving workers and stakeholders and applying the hierarchy of controls (elimination substitution engineering administrative and personal protective equipment).
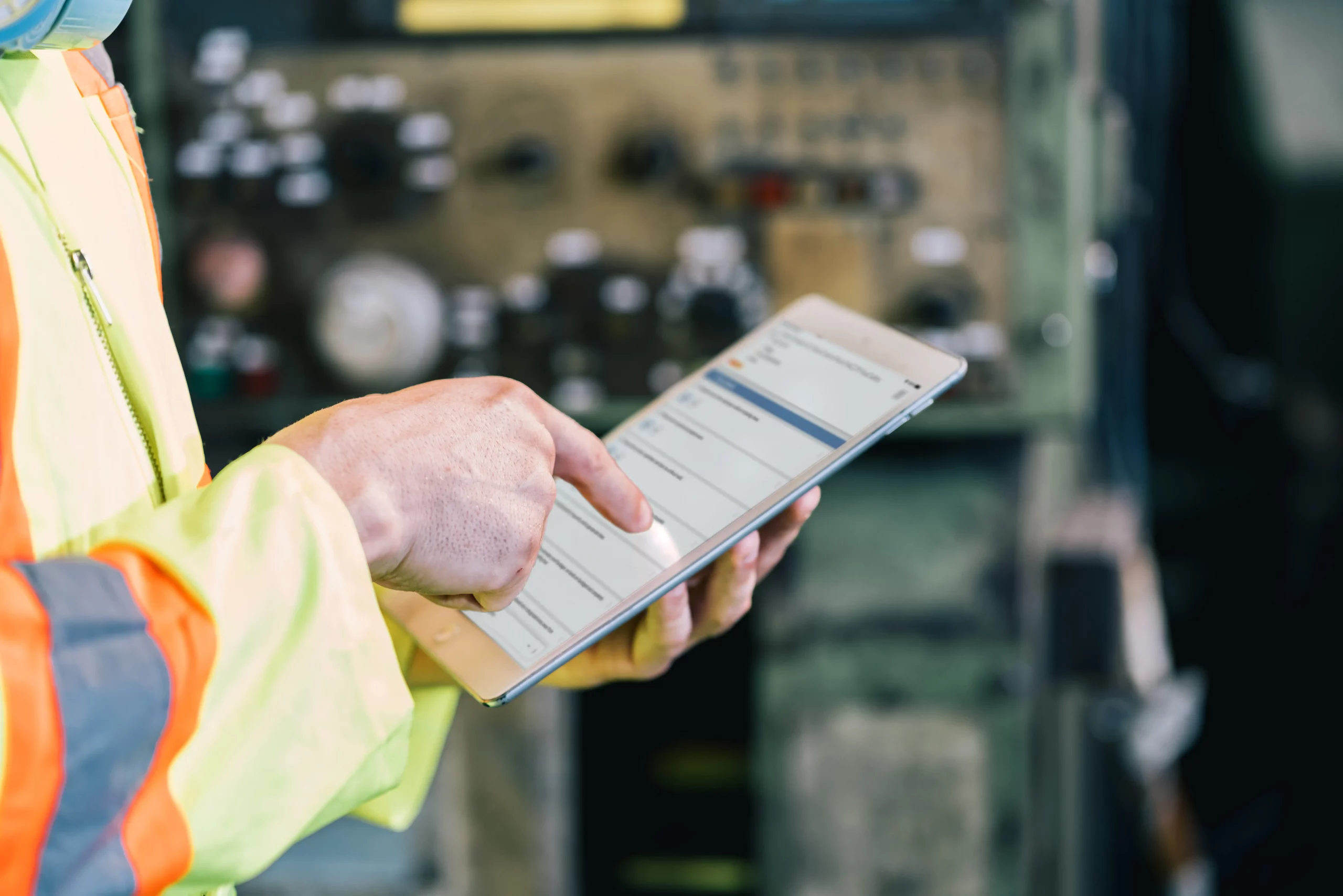
30+ Audit and inspection checklists free for download.
Risk assessment: Evaluate and prioritize the likelihood and severity of the consequences of a hazard or a risk. For example, using risk metrics and scales considering frequency and duration of exposure identifying vulnerable groups and scenarios, and applying the ALARP principle (as low as reasonably practicable).
Communication: Share and exchange information and feedback about hazards and risks in the workplace. For example, using clear and consistent signs and labels holding regular meetings and briefings encouraging open and honest dialogue, and using multiple channels and formats.
Safety Training: Provide and enhance the knowledge and skills of workers and managers to prevent and respond to near miss events. For example, conducting orientation and induction sessions offering refresher and specialized courses using interactive and engaging methods and assessing learning outcomes and retention.
Reporting: Record and analyze near miss events to identify and address underlying causes and trends. For example, establishing a simple and accessible incident reporting system creates a positive and supportive reporting culture collecting and analyzing data and feedback, and implementing corrective and preventive actions.
Check out our blog post on building near miss reporting system to learn more.
Here’s a link to OSHA’s Near Miss Reporting Policy.
How to Better Manage Near Miss Events
If you are looking for a way to improve your safety performance and prevent workplace injuries you should consider using Certainty. Certainty is a software solution that helps you report, track, analyze, and address safety compliance matters such as near miss events in an easy and efficient way. Improve your workplace safety with Certainty as you can:
- Create and customize near miss reporting forms that suit your specific needs and preferences
- Collect and submit near miss reports using any device, online or offline, with photos and signatures
- Analyze and visualize near miss data using dashboards, charts, and reports
- Identify trends, patterns, and root causes of near miss events
- Implement preventative and corrective actions to address near miss events
- Track and monitor the status and effectiveness of actions taken
- Communicate and collaborate with stakeholders on near miss issues
- Integrate with other systems and platforms for seamless data exchange
If finding a solution to improve your safety culture and better manage safety measures such as near miss events is important to you, get in touch with us to discover what Certainty can offer you.
You might also be interested in: