Table of contents
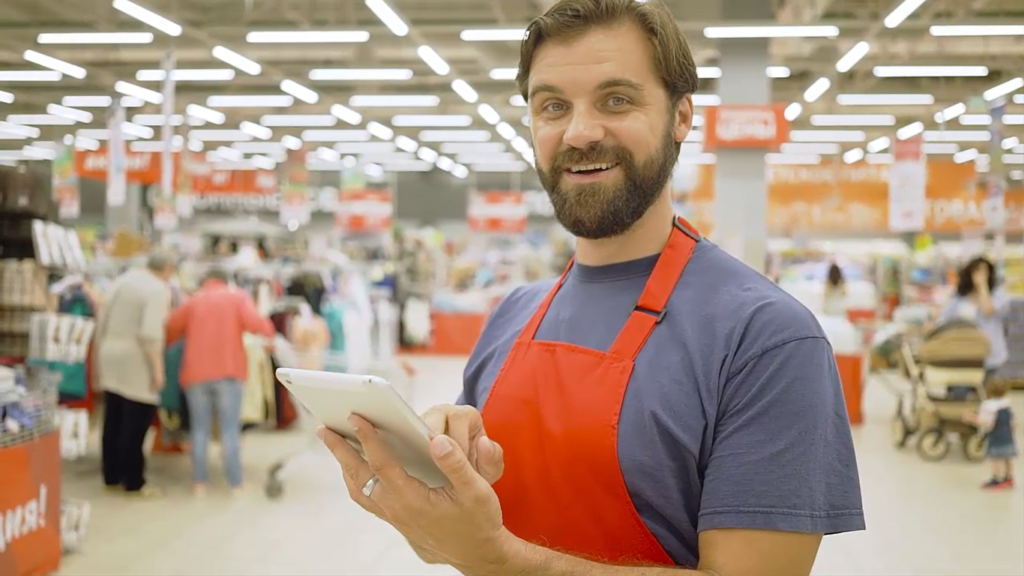
There’s always room for improvement. That’s the idea behind continuous improvement assessment frameworks, which can help organizations identify opportunities for improvement and take effective action. This is a key priority for manufacturing organizations, which continue to experience post-pandemic supply chain challenges — as noted by Bloomberg, the average lead time for materials reached a record-breaking 96 days in November 2021. The result? Companies can no longer be certain when — or if — material shipments will arrive. Continuous improvement assessments can help ensure that organizations are prepared to make the most of what they have, when they have it, to meet both customer and stakeholder expectations.
Why Does Continuous Improvement Matter?
Continuous improvement matters as an acknowledgment that there is no “perfect” state: Business processes can always be enhanced to reduce waste, improve efficiency, or minimize the risk of defects. Continuous improvement is also critical as digital processes become the norm for manufacturing organizations. With digital operations rapidly evolving to include mobile devices and the Internet of Things (IoT) enabled sensors and connections, the status quo provides success for shorter and shorter periods of time. To prepare for change and meet the challenge of digital transition head-on, businesses need continuous improvement.
Here are the core benefits of embracing a continuous improvement culture:
- It assists you in locating and fixing issues with your company’s procedures.
- You can increase productivity, quality, client satisfaction, and profitability.
- It enables you to be flexible and maintain an edge over the competition.
- It aids in developing a culture of invention, experimentation, and feedback.
- It aids in employee empowerment and acknowledges their accomplishments.
What Does a Continuous Improvement Assessment Accomplish?
A continuous improvement assessment tool helps companies create a framework for ongoing success. By taking the time to assess current operations, pinpoint areas for improvement, and take directed action, manufacturers can make the most of the people and processes they have, while simultaneously identifying the need for additional staff or resources. Consider a production line station that has consistently met time and quality goals. While at first glance there may seem to be no need for improvement, a continuous assessment might identify a process or component that could be modified to improve output times and boost overall efficiency.
The 4 Phases of Continuous Assessment
Continuous improvement assessment methodology leverages four key phases: Plan, do, check, and act, also called the PDCA cycle to help drive decision-making. The term “cycle” applies because there is no end-state in PCDA — once actions have been taken to improve a specific process the cycle starts again at the planning stage to identify new opportunities for improvement.
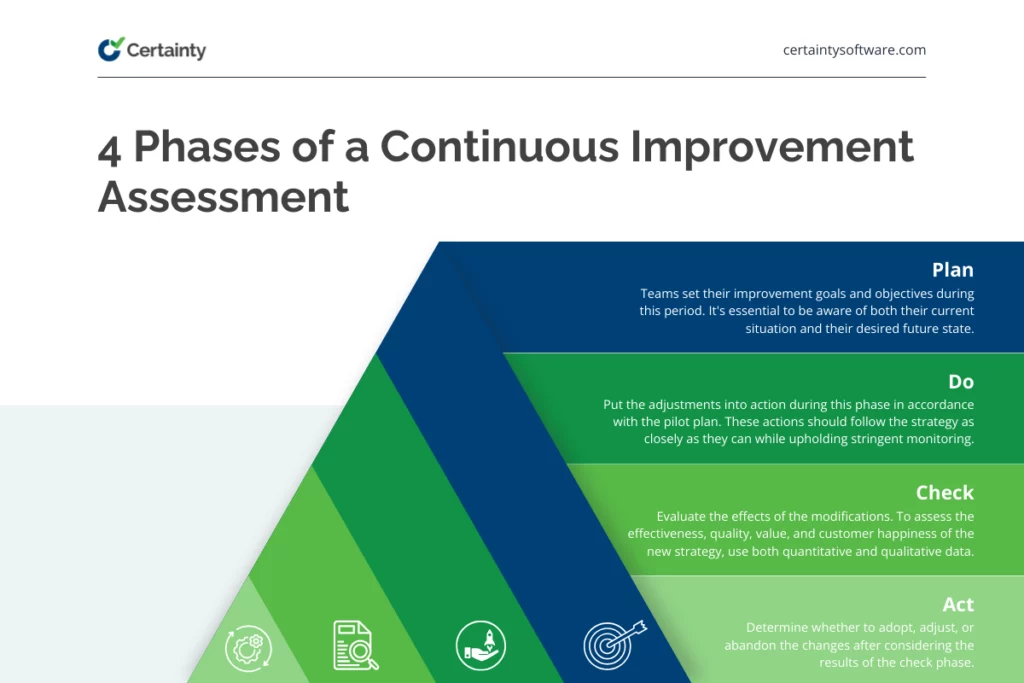
Let’s break down each phase in more detail:
Plan
Teams set their improvement goals and objectives during this period. It’s essential to be aware of both their current situation and their desired future state. They can achieve this by contrasting their present situation with the best practices of their sector or of their peers. This process, known as benchmarking, assists teams in establishing reasonable and doable improvement goals.
Teams can utilize a variety of approaches or tools for benchmarking, including balanced scorecards, Porter’s five forces, SWOT analyses, and customer satisfaction surveys. Following benchmarking, teams should develop a pilot plan that describes the goals, resources, schedule, and anticipated results of the change program. The next phase’s implementation of the improvements should be guided by the pilot plan, which needs to be clear and comprehensive.
Do
After the Plan stage, you’ll need to put the adjustments into action during this phase in accordance with the pilot plan. These actions should follow the strategy as closely as they can while upholding stringent monitoring of the development and effectiveness of the adjustments. However, be prepared to modify as necessary.
Utilizing small-scale pilot initiatives with a constrained number of participants, locations, or units is one technique to reduce the impact on the organization’s regular operations while evaluating the new strategy. By doing so, you can prevent causing a systemic disruption while still testing the modifications in real-world settings. Companies can utilize the lessons they’ve learned from their failures and triumphs from small-scale pilot programs to the following stage.
Check
Now that you have begun implementing your actions, it’s time to measure and evaluate the effects of the modifications. To assess the effectiveness, quality, value, and customer happiness of the new strategy, use both quantitative and qualitative data. Also, ensure that you and your team assess if your goals and objectives set during the planning phase are a success by comparing the results to those goals and objectives.
Using the root cause analysis, uncover and understand the underlying causes of the success or failure of the improvements. Deploying a root cause analysis is a highly effective methodical approach to determining what happened, why it happened, and how to stop it from happening again. From here, you can gain knowledge from any mistakes and sharpen your problem-solving abilities.
Act
Now, at this stage, you need to determine whether to adopt, adjust, or abandon the changes after considering the results of the check phase. Your team should expand the improvements to include more people, places, or units if they have shown to be efficient and advantageous. Scaling up implies implementing the modifications while preserving their effectiveness and quality in a bigger system or context. Increasing the organization’s efficiency, productivity, profitability, and competitiveness, can have a substantial impact on the entire business.
A manufacturing corporation, for instance, may scale up a new quality control system after successfully implementing it in one facility to all of its plants, which would boost customer satisfaction and market share. You may need to forsake the adjustments and go back to their prior state or try an alternative strategy, however, if the alterations have turned out to be unsuccessful or harmful.
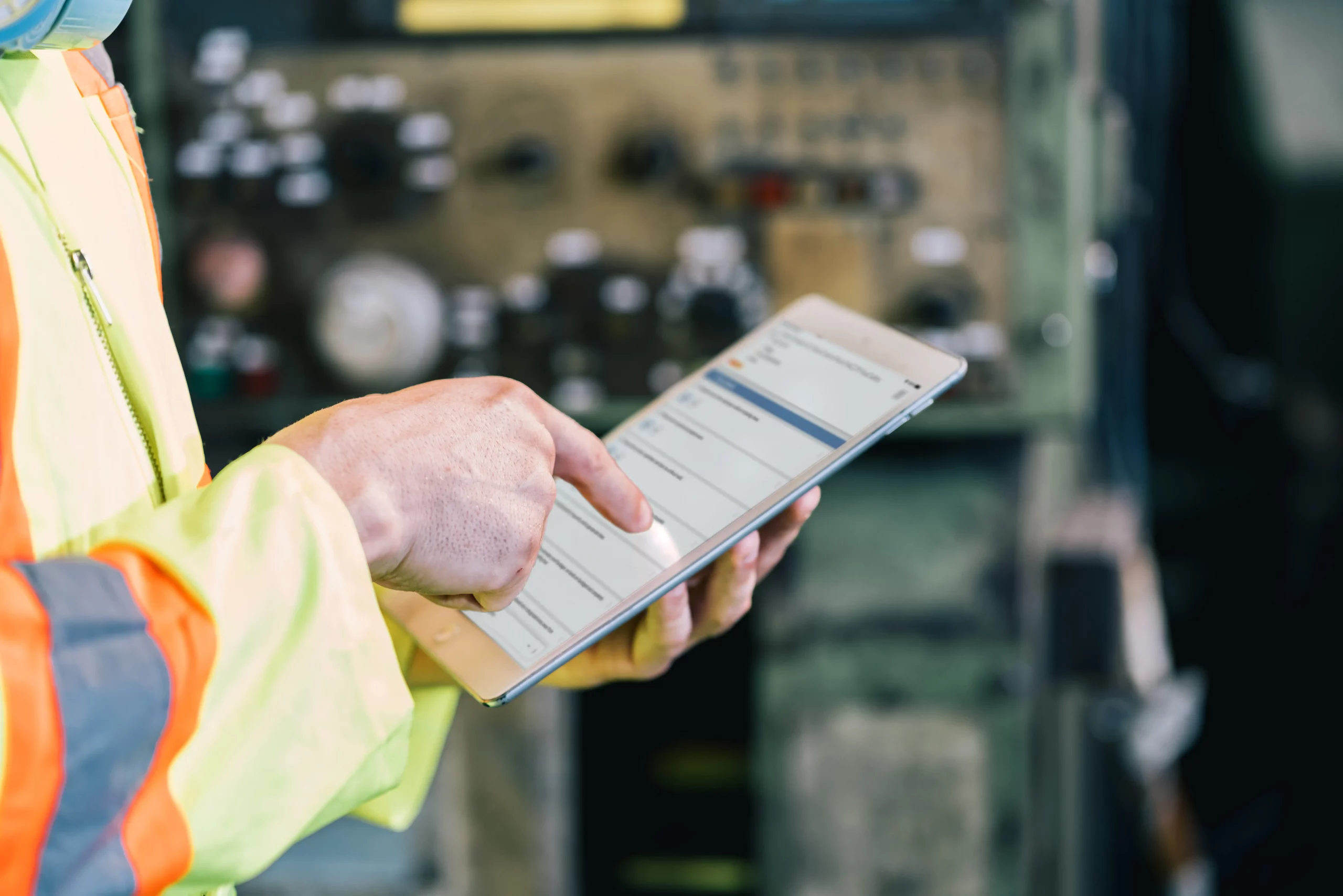
30+ Audit and inspection checklists free for download.
Methods for Effective Evaluation
How do you effectively implement continuous improvement assessment initiatives across your organization? Several common methods exist. One of the most popular is the Kaizen continuous improvement process which utilizes techniques such as Gemba walks to identify areas for long-term improvement. Other options include lean manufacturing, lean Six Sigma, and DMAIC, or “define, measure, analyze, improve and control”.
No matter which assessment process approach you choose, it’s worth laying a solid foundation. Start with purpose-built Gemba Walk checklists or ESG checklists to get a sense of where improvement efforts are working and where they need improvement, and then leverage robust reporting and documentation software to ensure consistent, comparable, and accurate performance metrics are available to relevant stakeholders in real-time.
While assessment methods differ, assessment results are more straightforward: Companies define desired outcomes and then use on-site data collection to determine effective improvement actions. These may include educational programs for the staff improvement plans that help address current management system challenges or specific performance indicators that are negatively affecting strategic planning initiatives.