Table of contents
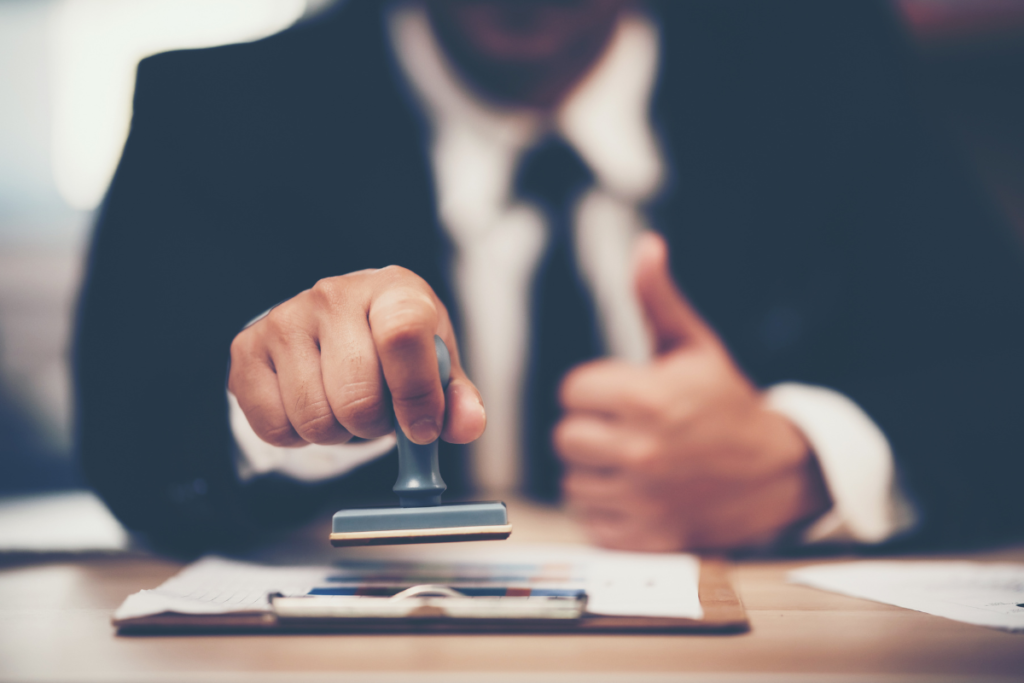
If your business is in the manufacturing sector, you are aware of how crucial it is to guarantee that your products meet the quality and safety requirements set forth by your market and industry. Failure to do so may result in exorbitant fines, product recalls, client complaints, and reputational harm to your company.
But how can you demonstrate that your goods adhere to the necessary rules and requirements? A Certificate of Conformity (CoC) is useful in this situation.
A CoC is a document that attests to the fact that your product has undergone testing and verification by an approved third party and complies with all required standards. In some nations and locations, it is a prerequisite for the sale of specific goods, and it can also be a useful instrument for boosting consumer confidence and happiness.
You will have a comprehensive grasp of what a CoC is, how to obtain one, and how to use one for the success of your manufacturing business at the end of this article.
Understanding Certificate of Conformity (CoC)
A Certificate of Conformity (CoC), also known as a Certificate of Compliance or Certificate of Conformance, is a document issued by an authorized party (such as a manufacturer, importer, or third-party testing and certification body) that states that a product meets the required standards or specifications.
A CoC can either be requested by a buyer to ensure product quality and safety, or it can be a mandatory requirement by law for certain products in certain countries or regions.
The significance of Certificate of Conformity in the manufacturing industry
A Certificate of Conformity is used to show that a product has been examined and found to adhere to the rules and requirements that are relevant. This can guard consumers, employees, and the environment from potential risks while also ensuring the quality, safety, performance, and dependability of the product.
The significance of a CoC in the manufacturing industry is that it can help to:
- Avoid legal liabilities and penalties for non-compliant products
- Prevent product recalls and rework costs
- Reduce customer complaints and returns
- Increase customer confidence and satisfaction
- Enhance brand reputation and credibility
- Gain competitive advantage and market access
- Facilitate trade and customs clearance
Key components in a typical Certificate of Conformity
A typical Certificate of Conformity should include the following key components and information:
- Product identification: A clear description of the product name, model number, serial number, batch number, etc.
- Manufacturer/importer identification: The name, address, contact details, etc. of the manufacturer or importer of the product
- Standards/specifications: The list of relevant standards or specifications that the product complies with (such as ISO, ASTM, UL, CE, etc.)
- Test results: The summary or details of the test results that demonstrate the product conformity
- Certification body: The name, address, contact details, accreditation number, etc. of the third-party testing and certification body that issued the CoC (if applicable)
- Declaration: A statement by the manufacturer or importer that certifies that the product conforms to the required standards or specifications
- Signature: The signature, name, title, date, etc. of the authorized person who issued the CoC
The Benefits of Obtaining a Certificate of Conformity
Obtaining a Certificate of Conformity for your products can bring you many benefits as a manufacturing company. Here are some of them:
Ensuring product compliance with industry standards and regulations
Getting a CoC will help you make sure that your items adhere to the norms and laws that are relevant to your market, which is one of the key advantages. By doing this, you can protect your company from costly and harmful legal obligations and penalties for non-compliant items.
For instance, the U.S. Consumer Product Safety Commission states that a General Certificate of Conformity (GCC), provided by the manufacturer or importer and attesting to the items’ compliance with all relevant consumer product safety regulations, is required for some non-children’s products. Civil or criminal consequences, including fines of up to $15.5 million per violation, may ensue from failure to comply.
Similarly to that, in order to comply with all applicable European Union rules and regulations, certain products must bear the CE marking and a Declaration of Conformity (DoC) signed by the maker or importer. If you don’t, you risk market monitoring, product recalls, or legal action.
Mitigating risks associated with non-compliant products
The ability to reduce the risks connected with non-compliant products, such as product recalls, rework expenses, customer complaints, returns, and legal action, is another advantage of acquiring a CoC.
Products that aren’t compliant can put your customers, employees, and the environment in grave danger by causing accidents, sicknesses, fires, explosions, or pollution. These dangers could have detrimental effects on your company, including:
- Loss of customer trust and loyalty
- Damage to brand reputation and credibility
- Loss of market share and competitive advantage
- Loss of revenue and profit
- Legal liabilities and penalties
Enhancing customer confidence and brand reputation
A Certificate of Conformity can also assist you improve customer confidence and brand reputation, which is its third advantage. Today’s consumers care more about the reliability and security of the goods they purchase. They seek assurance that the goods they purchase are trustworthy, robust, and safe.
You may demonstrate to your clients that you value their needs and expectations and that you are dedicated to providing them with high-quality and safe products by obtaining a CoC. The CoC can also be used as a marketing strategy to set your products apart from those of your rivals and draw in new clients.
With your stakeholders, including suppliers, distributors, retailers, regulators, and industry groups, a CoC can also help you establish credibility and confidence. By obtaining a CoC, you can demonstrate to them that you are a dependable and responsible manufacturer who adheres to the norms and best practices of your sector.
Navigating the Certificate of Conformity Legal and Regulatory Landscape
A Certificate of Conformity for your products can be difficult to get because of the complicated and ever-changing legal and regulatory environment. Depending on the kind of product, industry, standard, or specification, various countries and regions have varying criteria for CoC. Additionally, these standards may alter over time as a result of fresh discoveries or revisions to the laws or regulations.
You must therefore constantly be aware of the CoC criteria that are relevant to your products and markets. Following are some pointers for navigating the legal and regulatory environment:
Overview of relevant international and regional regulations
Understanding the pertinent national and regional laws that control the Certificate of Conformity requirements for your items is one of the first stages. Among the most typical ones are:
- The International Organization for Standardization (ISO) is a private, non-governmental organization that creates and disseminates international standards for a range of business sectors and industries. Quality management, environmental management, health and safety management, social responsibility, and other topics are all covered by ISO standards. Despite being optional, several nations and regions have embraced ISO standards as part of their legislative system.
- The International Electrotechnical Commission (IEC): IEC is an international organization that develops and publishes standards for electrical, electronic, and related technologies. IEC standards cover aspects such as electrical safety, electromagnetic compatibility, performance testing, etc. IEC standards are also voluntary but widely adopted by many countries and regions as part of their regulatory framework.
- The European Union (EU): A single market is run by the EU, a political and economic union of 27 member states, which also shares similar laws and regulations. The EU has a number of directives and rules that establish the standards for product compliance in a variety of industries, including consumer goods, industrial, and medical devices. Additionally, the EU mandates that specific products bear the CE (Conformité Européenne) label, which certifies that the product complies with all applicable EU directives and rules.
These are only a few instances of the regional and global laws that could have an impact on your CoC needs. Before requesting a CoC, you should always confirm the precise requirements for your products and markets.
Common certification bodies and standards applicable to different industries
Finding the common certification organizations and standards that apply to your sector and product category is a further step. Organizations known as certification bodies offer testing and certification services for items to confirm their adherence to the necessary standards or requirements. Standards are written descriptions of the prerequisites, standards, rules, or requirements that items must fulfill in order to guarantee their quality, safety, performance, etc.
The most popular certification organizations and guidelines for various industries including:
- Consumer goods: DNV, UL, Intertek, SGS, TÜV SÜD, and other well-known certification agencies for consumer goods include these. ISO 9001 (quality management), ISO 14001 (environmental management), ISO 45001 (occupational health and safety management), and others are some of the typical standards for consumer goods.
- Medical devices: BSI, DNV, DEKRA, NSF International, and others are a few of the often-used certification organizations for medical devices. Common standards for medical devices include IEC 60601 (electrical safety and performance for medical electrical equipment), ISO 13485 (quality management for medical devices), ISO 14971 (risk management for medical devices), etc.
- Machinery: Some of the common certification bodies for machinery are CSA Group, TÜV Rheinland, DNV, Bureau Veritas, etc. Some of the common standards for machinery are ISO 12100 (safety of machinery), ISO 13849 (safety-related parts of control systems), IEC 60204 (electrical equipment of machines), etc.
How to identify the specific requirements for your manufacturing business
The last step is to determine the precise requirements for your manufacturing company based on the nature of your products, your sector, your target market, and your client’s wants. There is no one-size-fits-all method for acquiring a CoC because many circumstances may affect the requirements for diverse products.
To determine the precise needs of your manufacturing company, you might consider asking yourself some of the following questions:
- What inclinations or goals do customers have for your goods? Consider its appearance, functionality, use, warranty, etc.
- What features of the product influence its compliance? For instance, the item’s size, shape, weight, substance, purpose, effectiveness, etc.
- What are the requirements or industry standards that apply to your product? For instance, its caliber, security, dependability, toughness, etc.
- What rules or laws are there in your target market that apply to your product? Labeling, packing, paperwork, testing, certification, etc. are a few examples.
- What preferences or expectations do customers have for your product? For instance, how it looks, works, is usable, has a warranty, etc.
The Certificate of Conformity Process
You can move on with obtaining a Certificate of Conformity for your product once you have determined the precise requirements for it. Depending on the product type, industry, market, and certification authority, the procedure for acquiring a CoC may vary, but it typically entails the following steps:
Preparing documentation and product testing
To prove your product’s conformity, you must first produce the relevant paperwork and do the necessary product testing. The records could consist of:
- Product specifications: A detailed description of your product characteristics, features, functions, performance, etc.
- Test reports: A summary or details of the test results that show your product’s conformity to the relevant standards or specifications
- Declaration of Conformity: A statement by you that certifies that your product conforms to the required standards or specifications
- Certificate of Conformity: A document issued by an authorized party that certifies that your product conforms to the required standards or specifications
The product testing may include:
- In-house testing: Testing conducted by you or your supplier using your own equipment and methods
- Third-party testing: Testing conducted by an independent testing and certification body using their equipment and methods
- Laboratory testing: Testing conducted in a controlled environment using specialized equipment and methods
- Field testing: Testing conducted in a real-world environment using actual conditions and scenarios
You may need to create various types and degrees of documentation and product testing depending on the product type, industry, market, and certification organization. Always follow the rules and regulations provided by the relevant parties and authorities.
You can utilize the free checklists available for download from Certainty Software to assist you with this process. These checklists cover a variety of product compliance topics, including quality, safety, the environment, social issues, etc. These checklists are made to assist you in gathering accurate, comparable, and consistent data to meet your CoC obligations. Additionally, you can alter them to meet your unique requirements and tastes.
Choosing a reputable third-party testing and certification body
Selecting a trustworthy third-party testing and certification organization to carry out the assessment and audit of your product compliance is the second stage. An organization that offers testing and certification services for products to confirm their conformity with the appropriate standards or specifications is known as a third-party testing and certification body.
Choosing a reputable third-party testing and certification body can help you to:
- Ensure the accuracy, validity, and reliability of your test results and CoC
- Gain recognition, acceptance, and trust from your customers, regulators, and industry associations
- Save time, money, and resources by outsourcing the testing and certification process
- Access expert knowledge, advice, and support from the testing and certification professionals
Some of the factors you should consider when choosing a reputable third-party testing and certification body are:
- Accreditation: The accreditation status of the testing and certification body by an authoritative body that attests to its competence, impartiality, and credibility
- Experience: The experience level of the testing and certification body in your industry, product type, market, and standards or specifications
- Reputation: The reputation of the testing and certification body among your customers, regulators, and industry associations
- Service: The service quality of the testing and certification body in terms of speed, cost, flexibility, communication, etc.
Before selecting a credible third-party testing and certification authority, you should always do your homework and weigh your possibilities.
The assessment and audit process
The third phase entails participating in a third-party testing and certification body’s assessment and audit procedure. The assessment and audit process involves carrying out numerous tests, inspections, assessments, etc. to determine whether your product complies with the applicable standards or requirements.
Depending on the product type, industry, market, and certification authority, the assessment and audit process may vary, but it often includes the following steps:
- Application: You submit an application to the testing and certification body with the required documentation and information about your product
- Review: The testing and certification body reviews your application and documentation to determine if they meet the eligibility criteria
- Testing: The testing and certification body conducts various tests on your product samples or prototypes to measure their conformity to the relevant standards or specifications
- Inspection: The testing and certification body conducts various inspections on your production facilities or processes to ensure their conformity to the relevant standards or specifications
- Evaluation: The testing and certification body evaluates your test results and inspection reports to determine if they meet the compliance requirements
- Audit: The testing and certification body audits your quality management system or procedures to ensure their conformity to the relevant standards or specifications
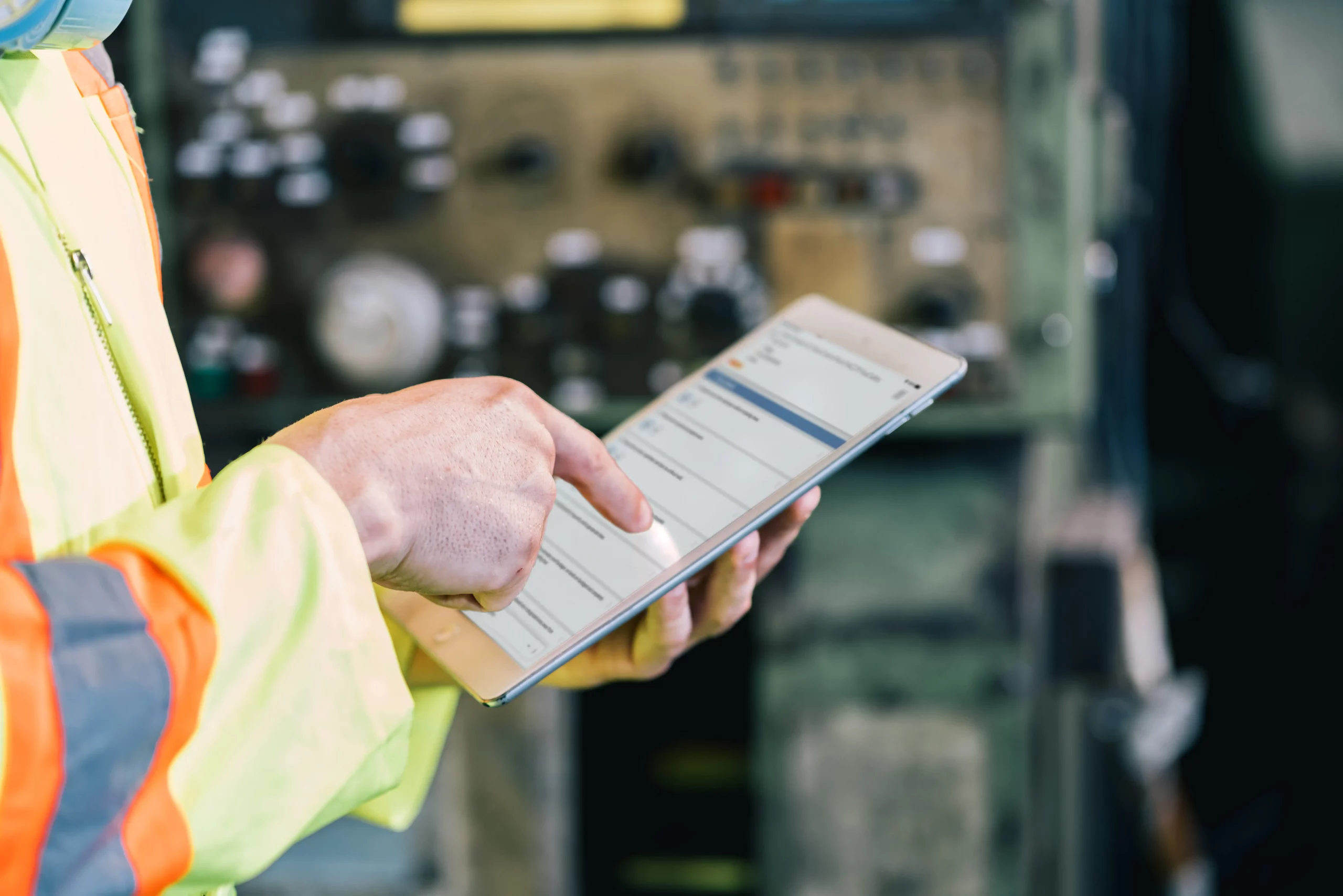
30+ Audit and inspection checklists free for download.
Issuance of the Certificate of Conformity
The third-party testing and certification body’s issue with the Certificate of Conformity is the last stage. The final assurance that your product complies with the necessary standards or specifications is the CoC’s issue.
The CoC may be issued in connection with:
- Certificate of Conformity: A document issued by the third-party testing and certification body that certifies that your product conforms to the required standards or specifications
- Marking or labeling: A symbol or label affixed to your product or packaging that indicates that it conforms to the required standards or specifications (such as CE marking for EU products)
- Registration or notification: A record or notification submitted to a regulatory authority or database that indicates that your product conforms to the required standards or specifications (such as FCC registration for US products)
A copy of your CoC and any related documentation should always be kept for future reference or verification. Every time your product, standards, specifications, or laws change, you should update your CoC and all relevant documentation.
Common CoC Challenges and How to Overcome Them
Getting a CoC for your items can be a challenging, lengthy procedure that is fraught with many obstacles. Here are some typical obstacles and suggestions for overcoming them:
Identifying and addressing potential compliance gaps
Finding and fixing possible compliance gaps in your product’s design, development, or production is one of the common issues. Compliance gaps are inconsistencies or differences between your product’s performance or features and the necessary standards or specifications.
Compliance gaps can result in:
- Non-conformity: Your product fails to meet the compliance requirements or expectations
- Non-compliance: Your product violates the compliance rules or regulations
- Non-acceptance: Your product is rejected or returned by your customers, regulators, or industry associations
To overcome this challenge, you should:
- Conduct a gap analysis: A gap analysis is a systematic process of comparing your product characteristics or performance with the required standards or specifications to identify and prioritize the gaps
- Implement corrective actions: Corrective actions are actions taken to eliminate or reduce the gaps by modifying your product design, development, or manufacturing
- Monitor and evaluate the results: Monitoring and evaluation are processes of measuring and assessing the effectiveness and impact of your corrective actions on your product compliance
Dealing with product modifications and updates
Dealing with product upgrades and alterations that can influence your product compliance is another typical difficulty. A product’s qualities, features, functionalities, performance, etc. may change as a result of a variety of factors, including consumer feedback, market demand, technical innovation, etc.
- Product modifications and updates can result in:
- Non-validity: Your CoC becomes invalid or outdated due to the changes in your product
- Non-applicability: Your CoC becomes irrelevant or inappropriate due to the changes in the standards, specifications, or regulations
- Non-transferability: Your CoC becomes non-transferable or non-reciprocal due to changes in the market or customer requirements
To overcome this challenge, you should:
- Review and update your CoC whenever there are changes to your product, standards, specifications, or regulations to ensure its validity, applicability, and transferability
- Re-test and re-certify your product whenever there are significant changes to your product characteristics or performance that may affect its conformity to the required standards or specifications
- Communicate and coordinate with your stakeholders such as customers, regulators, industry associations, certification bodies, etc. whenever there are changes to your product compliance status or requirements
Handling cross-border trade and international CoC requirements
Handling cross-border trade and international CoC requirements that may differ from country to country or region to area is a third frequent difficulty. The laws or rules that control the importing or exportation of goods across different nations or areas are cross-border trade and international CoC requirements.
Cross-border trade and international CoC requirements can result in:
- Confusion: You may be confused by the different or conflicting CoC requirements for different countries or regions
- Complexity: You may face complexity in complying with multiple or diverse CoC requirements for different countries or regions
- Cost: You may incur additional costs in obtaining multiple or different CoCs for different countries or regions
To overcome this challenge, you should:
- Research and understand the CoC requirements for each country or region that you intend to trade with, such as their standards, specifications, regulations, certification bodies, etc.
- Harmonize and streamline your CoC process by adopting common or compatible standards, specifications, regulations, certification bodies, etc. for different countries or regions
- Leverage mutual recognition agreements (MRAs) that are agreements between two or more countries or regions that recognize each other’s testing and certification results for certain products
How Constant Compliance is Made Easier with Certainty Software
Certainty Software will assist you if you’re seeking a dependable and effective way to get and keep CoC for your items. A platform for enterprise-level inspection software called Certainty Software makes it simple to gather, report, and handle issues found during inspections.
Using Certainty Software, you can:
- Use pre-built templates or design your own inspection forms to meet the requirements of your industry, market, and customers.
- Collect data using any device, such as a smartphone, tablet, or laptop, wherever you are—online, offline, in the field, or on the shop floor.
- Utilize real-time dashboards, charts, graphs, and reports to present uniform, comparative, and accurate performance indicators across your company.
- Easy and on-the-go problem-solving through the creation and delegation of tasks, deadline setting, reminder sending, and progress monitoring.
- Integrate your workflows and data management with other tools and systems, such as ERP, CRM, and QMS, among others.
- Utilize the Certainty Software team’s experience, guidance, and assistance to assure your success.
With simple forms, timely reports, and comprehensive action management, Certainty Software assists you in ensuring compliance, lowering risk, and enhancing performance. By delegating the inspection process to a credible third-party testing and certification agency, you can also save time, money, and resources.
If you’d like to learn more about how Certainty Software can help with your compliance needs, book a quick demo today.
You might also be interested in: