Table of contents
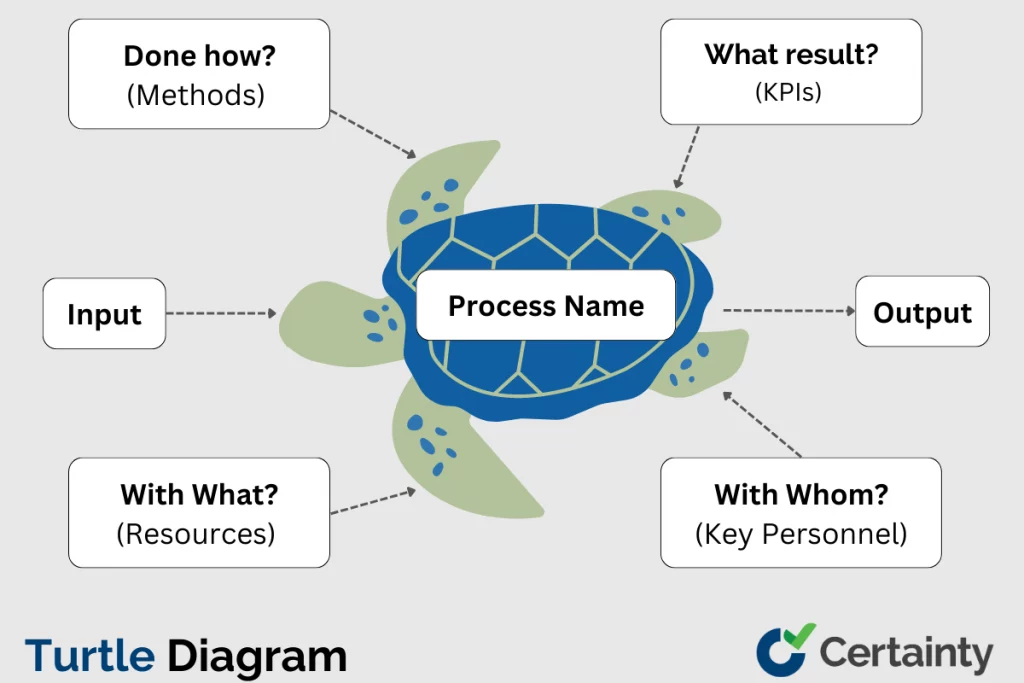
Quality management is an essential component of any business, and its significance is growing with time. To ensure quality, organizations use various tools and techniques to manage their processes and minimize errors. However, the complexity of these processes can make it difficult for individuals to understand and assess them. This is where the Turtle Diagram comes in. Although turtles may be considered slow, utilizing a Turtle Diagram in Quality Management Systems can significantly accelerate the comprehension of intricate processes. Let’s dive into what a Turtle Diagram is and how it can benefit you.
What is a Turtle Diagram?
A Turtle Diagram is a visual tool used to represent your quality management system (QMS) processes. It is a simple yet effective method developed by Philip Crosby that helps organizations understand the process and manage it effectively. The Turtle Diagram breaks down a process into five questions:
- What inputs?
- What output?
- Done How?
- What result?
- With What?
- With whom?
What does a Turtle Diagram Show?
A turtle diagram provides a graphical representation of the entire process, highlighting its inputs, outputs, support processes, and interested parties. It allows organizations to visualize and understand the process flow, identify any gaps or inefficiencies, and streamline QMS process improvement. Completing one ensures that the process is aligned with customer requirements and that each step in the process adds value to the final product or service. Doing so enhances customer satisfaction and the organization’s reputation.
The Elements of a Turtle Diagram
You may find understanding the input, output, supporting processes, and interested parties elements of the diagram made easier by asking these five questions:
What Inputs?
The inputs in a turtle diagram represent the resources needed to initiate the process. This includes the equipment, raw materials, information, and people required for the process. Inputs must meet the process requirements and customer needs. For instance, in the sourcing process, the inputs may include supplier information, contract documents, and specifications.
What Output?
The output is the end product or service that the process produces. These must meet the customer’s requirements and expectations. For example, the output in a manufacturing process could be a finished product, or in a service-oriented process, it could be a service report.
Done how?
This question requires a detailed description of the process steps, activities, and tasks involved in carrying out a process. It seeks to identify the specific actions that are necessary to achieve the desired process outcome. Answering this question requires a clear understanding of the process flow and the sequence of activities involved.
For example, in a manufacturing process, the “Done how?” question might require a step-by-step breakdown of the production process, including details about the equipment, tools, and materials used, as well as any quality checks or inspections that occur along the way.
What result?
The “What result?” question is a critical component as it focuses on the outputs or results of the process. In many cases, these results are measured using KPIs, which are quantitative or qualitative metrics used to evaluate the success of a process or activity.
It’s important to identify the specific KPIs that are relevant to the process being analyzed. For example, a manufacturing process might track KPIs such as production yield, defect rates, or equipment uptime, while a customer service process might track KPIs such as customer satisfaction, response times, or first-call resolution rates.
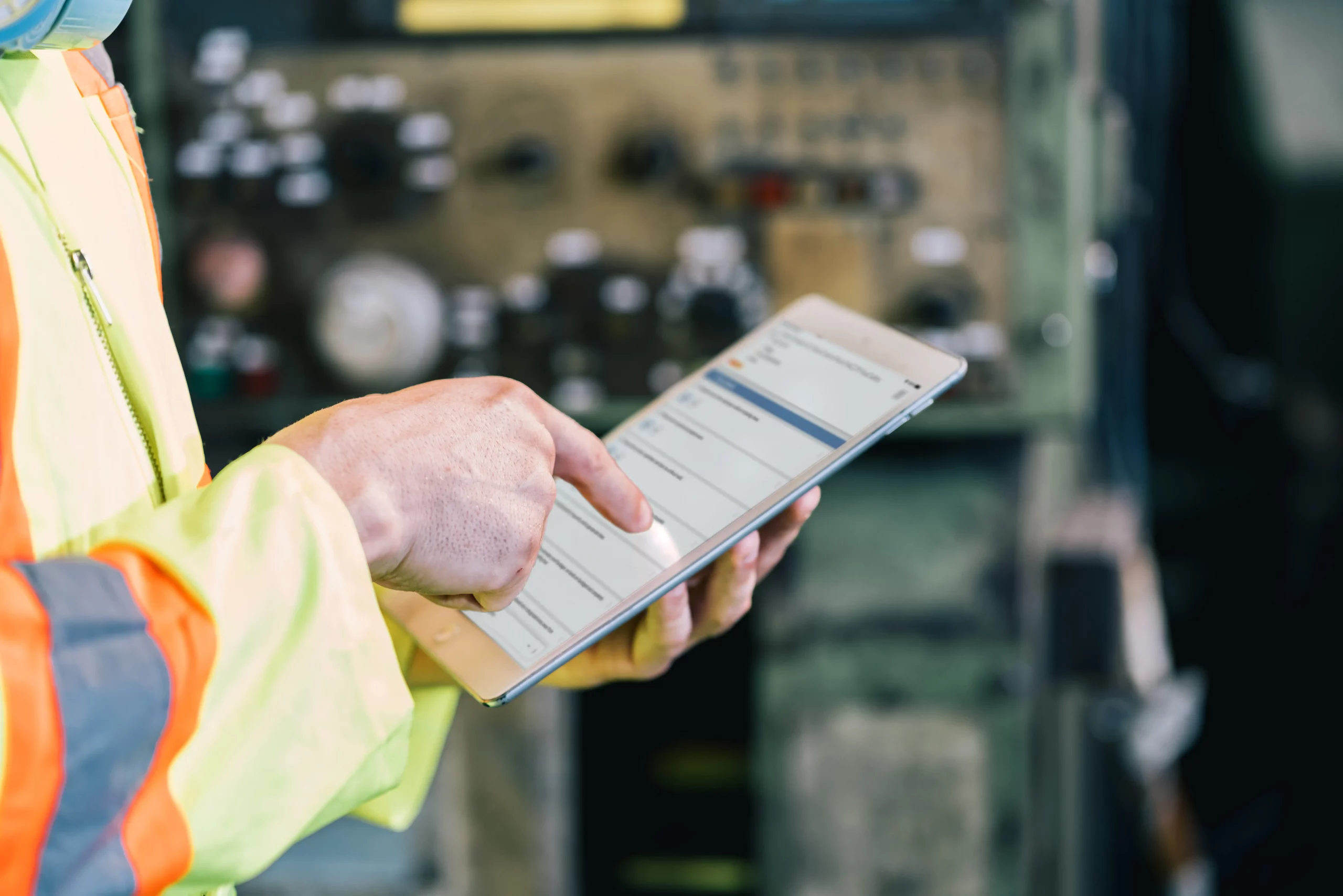
30+ Audit and inspection checklists free for download.
With what?
This question focuses on the resources required to carry out the process. It asks what equipment, tools, materials, or software are needed to complete the process successfully. For example, in a logistics process, the “With what?” question might require a list of the trucks, warehouses, and other resources needed to transport and store products. It might also require a description of any software or systems used to track inventory or shipments.
With whom?
Here relates to the people or organizations involved in the process. It asks who is responsible for carrying out each process step, who are the stakeholders or interested parties, and what are their needs and expectations. For example, in a customer service process, the “With whom?” question might require a list of the customer service representatives involved in the process, as well as any external stakeholders, such as customers or regulatory bodies. It might also require a description of any communication or feedback loops between stakeholders to ensure that customer needs are being met.
How to complete a Turtle Diagram
Get started by downloading our free Turtle Diagram Template.
Here’s a quick 8-step approach to completing a Turtle Diagram:
- Identify the process to be evaluated and the process owner.
- Gather all relevant information, such as inputs, outputs, and support processes.
- Map out the process using a process map or flowchart.
- Identify the interested parties and their needs and expectations.
- Determine the performance indicators or metrics that will be used to measure the process’s success.
- Analyze the process for risks and opportunities for improvement.
- Perform internal audits using quality audit checklists such as Certainty’s GMP Audit Checklist for identifying nonconformity and implementing corrective actions needed to improve the process.
- Review the turtle diagram in the management review process and implement continual improvement.
Discover how Certainty is the quality audit software solution.