Table of contents
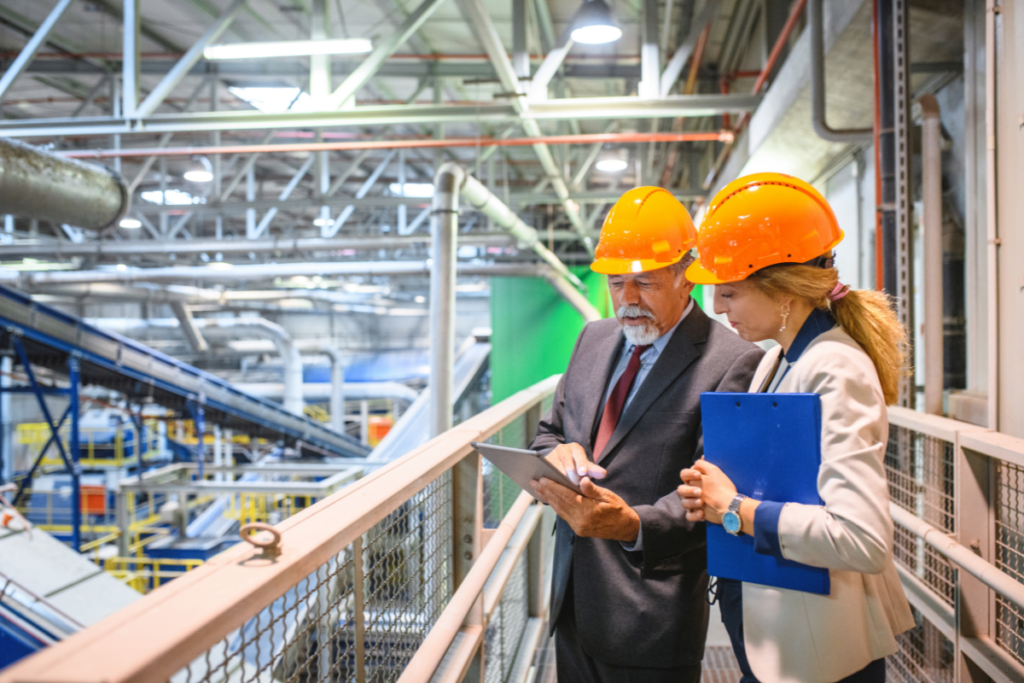
Imagine the possibility of running your business like a well-oiled machine, where every process operates smoothly, efficiently, and flawlessly. Where you can deliver exceptional value to your customers with minimal effort, time, and cost. Achieving higher levels of quality, productivity, and customer satisfaction is not just a dream – it’s within your reach.
The key lies in eliminating Muda from your business processes.
Muda, a Japanese term for waste, refers to any activity or resource that fails to add value to your customers or your business. Whether it’s within manufacturing, service, or administrative processes, Muda can have a detrimental impact on your operational performance, costs, and overall business outcomes.
In this blog post, we will guide you through the process of identifying and eliminating Muda from your business processes using proven lean management principles and methodologies. By following this guide, you will be empowered to streamline your processes, reduce waste, enhance efficiency, and pave the way for sustainable growth within your organization.
What is Muda?
Muda is one of the three types of waste that are commonly recognized in lean manufacturing thinking, along with Mura (unevenness) and Muri (overburden). Muda is any activity or resource that consumes time, money, space, or energy without creating any value for the customer or the business.
Some examples of Muda waste are:
- Producing more than what the customer needs or wants
- Waiting for materials, machines, people, or information
- Moving materials, products, or information from one place to another unnecessarily
- Storing excess inventory of materials, products, or information
- Performing unnecessary or redundant tasks or steps in a process
- Making errors or defects that require rework or correction
- Over-processing more resources than necessary to complete a task or produce a product
Muda can be classified into two categories: type 1 and type 2. Type 1 Muda is waste that is unavoidable or necessary due to the current conditions of the process or the market. For example, safety inspections or regulatory compliance. Type 2 Muda is waste that is avoidable or unnecessary and can be eliminated or reduced by improving the process. For example, overproduction or defects.
The goal of lean thinking is to eliminate type 2 Muda as much as possible and minimize type 1 Muda as much as possible. By doing so, you can increase the value-added activities in your process and deliver more quality control and ultimately value to your customers.
Why is Eliminating Muda Important?
Muda elimination is important because it can help you improve your process performance and outcomes in several ways:
- It can increase your productivity and efficiency by reducing the time and resources required to complete a task or produce a product.
- It can reduce your costs and waste of resources by eliminating unnecessary expenses and consumption.
- It can improve your quality and customer satisfaction by reducing errors, breakdowns, downtime, and defects and increasing reliability and consistency.
- It can enhance your competitiveness and profitability by increasing your value proposition and market share.
Muda elimination is also important because it can help you create a culture of continuous improvement in your organization. By identifying and eliminating Muda from your processes, you can foster a mindset of problem-solving, innovation, and learning among your employees. You can also empower them to take ownership of their work and improve their skills and capabilities.
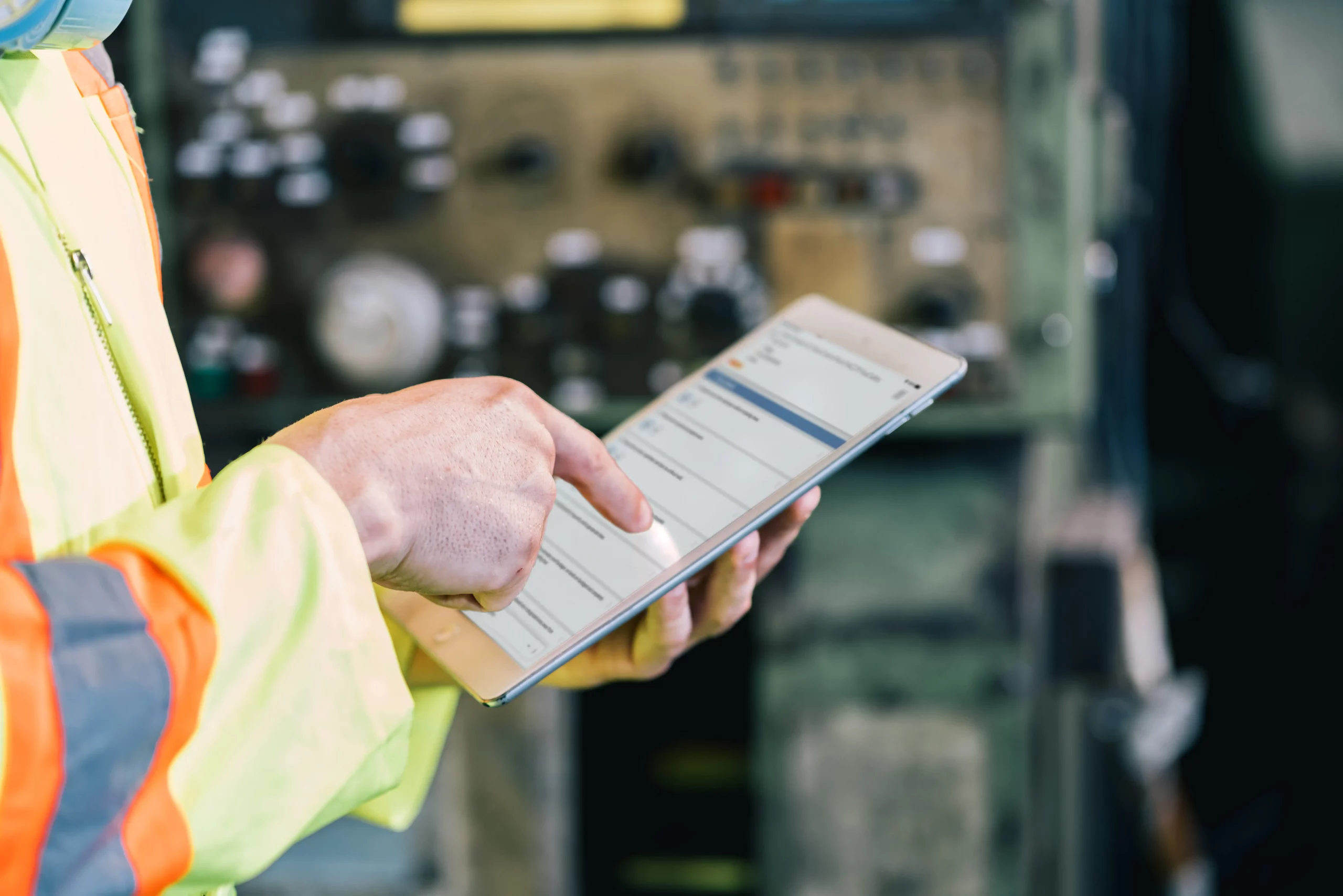
30+ Audit and inspection checklists free for download.
Muda elimination is not only beneficial for your organization but also for your customers, suppliers, society, and environment. By eliminating Muda from your processes, you can create more value for your customers by meeting their needs and expectations better. You can also create more value for your suppliers by reducing their waste and improving their efficiency. You can also create more value for society and the environment by reducing your environmental impact and social responsibility.
Understanding the Different Types of Muda
According to lean principles, three main types of Muda (waste) can occur in any process:
- Muda of transportation: This is the unnecessary movement of materials, products, or information from one location to another. For example, transporting raw materials from a distant warehouse to the production site, or sending documents back and forth between different departments.
- Muda of inventory: This is the excess amount of materials, products, or information that are stored or waiting to be processed. For example, having too much inventory of finished goods that are not sold, or having too many emails in your inbox that are not answered.
- Muda of motion: This is the unnecessary movement of people or equipment within a process. For example, walking across the shop floor to fetch a tool, or bending over to pick up a part.
To illustrate how these types of Muda can affect your processes, let’s look at some examples and scenarios:
- A manufacturing company produces automotive parts using a batch-and-queue system. The parts are transported from one machine to another using forklifts, and they are stored in large bins between each operation. The company suffers from high transportation costs, high inventory levels, high space requirements, and high cycle times.
- A service company provides accounting services to small businesses using a paper-based system. The documents are printed, scanned, faxed, mailed, or couriered between different offices and clients. The company suffers from high transportation costs, high inventory levels, high paper consumption, and a high risk of errors and losses.
- An administrative company processes insurance claims using a manual system. The employees have to move from their desks to different stations to access files, forms, computers, printers, scanners, etc. The company suffers from low productivity, high motion costs, high fatigue levels, and low employee morale.
As you can see, these types of Muda can have a significant impact on your process performance and outcomes. Therefore, it is essential to identify and eliminate these bottlenecks as much as possible.
Identifying Muda in Your Processes
How can you detect Muda within your organization? There are several techniques and approaches that you can use to identify waste in your processes:
Value Stream Mapping
This is a tool that helps you visualize the flow of materials, products, information, and value from the beginning to the end of a process. It helps you identify the value-added and non-value-added activities in each step of the process, as well as the sources of waste such as transportation, inventory, motion, waiting time, etc.
Gemba Walks
This is a practice that involves going to the actual place where the work is done (Gemba) and observing the process with a critical eye. It helps you see the reality of the process as it is happening, and identify any problems or opportunities for improvement.
Process Observation & Analysis
This is a method that involves collecting data and information about the process performance using various tools such as checklists, charts, graphs, timers, counters, etc. It helps you measure the current state of the process, and identify any gaps or deviations from the desired state.
Strategies for Eliminating Muda
Once you have identified Muda in your processes, how can you eliminate it? There are several lean principles and methodologies that you can use to reduce or eliminate waste from your processes:
6S Methodology
This is a system that helps you organize your work in a way that eliminates waste and improves efficiency. It consists of six steps: Sort, Set in order, Shine, Standardize, Sustain, and Safety. By applying this methodology, you can eliminate the Muda of transportation, inventory, motion, waiting, and correction.
Just-in-Time (JIT) Inventory Management
This is a system that helps you synchronize your production with your customer demand, and produce only what is needed when it is needed, and in the amount that is needed. By applying this system, you can eliminate the Muda of overproduction, inventory, waiting, and correction.
Kanban Systems
This is a system that helps you control the flow of materials, products, or information in your process using visual signals such as cards, boards, bins, etc. By applying this system, you can eliminate the Muda of overproduction, inventory, waiting, and correction.
Implementing These Strategies Into Your Business Processes
To help you implement these strategies effectively, here are some practical steps that you can follow:
- Define your value proposition: What is the value that you deliver to your customers? What are their needs and expectations? How do you measure your value delivery?
- Map your value stream: How do you deliver value to your customers? What are the steps involved in your process? What are the inputs and outputs of each step? What are the value-added and non-value-added activities in each step?
- Identify your sources of waste: Where is Muda occurring in your process? What are the causes and effects of Muda? How much waste is there in terms of time, cost, quality, etc.? Download Certainty’s free Gemba Walk Checklist to get started now with identifying wastes.
- Prioritize your improvement opportunities: Which sources of waste have the most impact on your value delivery? Which sources of waste are the easiest or hardest to eliminate? How can you rank your improvement opportunities based on their importance and feasibility?
- Implement your improvement actions: How can you apply the lean principles and methodologies to eliminate or reduce waste in your process? What resources do you need to implement your improvement actions? How will you monitor and evaluate your improvement actions?
- Review and refine your process: How effective are your improvement actions? What are the results and benefits of your improvement actions? What are the challenges or barriers that you faced or may face in implementing your improvement actions? How can you overcome them? How can you sustain or improve your process performance?
How to Use Certainty to Eliminate Muda from Your Processes
Certainty is an enterprise-level inspection software solution that can help you eliminate Muda from your business processes. Our tool allows you to collect and report inspection data, monitor and measure your process performance, manage issues and actions, streamline your processes and reduce waste, ensure quality assurance and compliance, and improve your business outcomes.
A web-based solution, Certainty can be used online or offline, on any device, and in any location. It is trusted by hundreds of thousands of users across various industries and sectors. If you want to see how Certainty Software can help you eliminate muda from your processes, book a demo today.