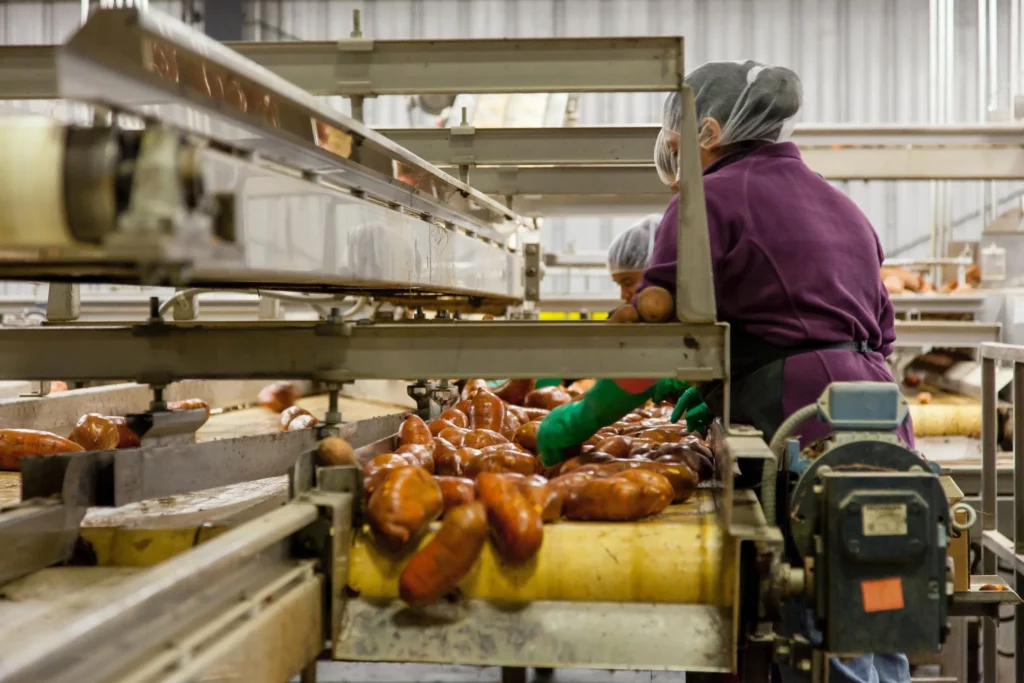
Informed by the Food Safety Modernization Act (FSMA), manufacturers are required to implement processes that actively reduce the risk of foodborne illness, both from known pathogens and unknown agents. These processes are critical to track the type and nature of these illnesses and mitigate their impact — according to the CDC, 48 million Americans fall ill with food-related sickness each year. Of those, more than 100,000 are hospitalized and on average 3,000 will die.
To help standardize the creation and implementation of food safety processes, U.S. Food and Drug Administration (FDA) has created a best practice guideline: GMP. Here’s a look at what it is, where GMP applies, and how your business can make the best use of this essential safety ingredient.
What are Good Manufacturing Practices (GMP)?
According to the FDA, “GMPs describe the methods, equipment, facilities, and controls for producing processed food.” Good manufacturing processes were developed as a way to standardize frameworks around facilities management, food processing, and packaging operations to help reduce the risk of foodborne illness in the supply chain and provide clear directives to food processors and manufacturers.
Key components include adequate maintenance of facilities and buildings, the design and maintenance of equipment, record keeping, the development of reliable sanitization processes and controls, and the establishment of defect action levels (DLAs) that may prompt responses from the FDA.
Worth noting? Some GMPs are general, while others are more specific. For example, plumbing must be of “adequate size and design” to support facility operations, but companies are obligated to install self-closing doors for all toilet facilities.
Benefits of GMP Certification for Food Businesses
GMP certification is a voluntary process that demonstrates your compliance with the Good Manufacturing Practices for food safety. By obtaining certification, you can:
- Enhance your reputation and credibility among customers, suppliers, and regulators
- Reduce the risk of foodborne illnesses, recalls, and legal actions
- Improve your operational efficiency and productivity
- Gain a competitive edge in the market
- Access new markets and opportunities
How to Achieve GMP Certification
To get GMP certified, you need to undergo an audit by a third-party organization that verifies your adherence to the GMP standards. The audit will cover aspects such as:
- Facility design and maintenance
- Equipment design and maintenance
- Personnel hygiene and training
- Sanitation and pest control
- Production and process controls
- Record keeping and traceability
Common GMP Violations and How to Avoid Them
GMP violations are the instances where you fail to comply with the GMP requirements for food safety. Some of the common violations are:
- Lack of proper documentation and records
- Inadequate cleaning and sanitizing of equipment and utensils
- Poor personal hygiene and health practices of employees
- Improper storage and handling of raw materials and finished products
- Failure to monitor and control critical parameters such as temperature, pH, moisture, etc.
- Use of expired or contaminated ingredients or additives
To avoid GMP violations, you should:
- Implement a written GMP program that outlines your policies and procedures for food safety
- Train your staff on the requirements and their roles and responsibilities
- Conduct regular inspections and audits to check your compliance status and identify any gaps or issues
- Correct any non-conformities or deviations as soon as possible and document the corrective actions taken
- Review and update your GMP program periodically to reflect any changes in regulations, processes, or products
What is a GMP Audit?
A GMP audit is an end-to-end evaluation of GMP processed by a third party to ensure compliance for food processors. The goal of these audits is to identify any potential areas of concern and help companies remedy regulatory deviations to boost overall food safety and ensure compliance. It’s worth regularly conducting audits to assess compliance since the cost of bringing in a reliable auditing firm is typically far less than the potential downtime that comes with a failed FDA audit.
Best bet? Start with a GMP checklist to see where your processes meet expectations and where they could use improvement.
How to Prepare for a GMP Audit and What to Expect
A GMP audit is an assessment of your compliance with the GMP standards for food safety by an external auditor. A GMP audit can be conducted by:
- A regulatory authority such as the FDA or CFIA
- A certification body that offers GMP certification services
- A customer or supplier that requires compliance as part of their contract
To prepare for a GMP audit, you should:
- Review your GMP program and ensure it is up-to-date and complete
- Gather all the relevant documents and records that support your compliance claims
- Conduct a self-audit or a mock audit to identify any potential weaknesses or areas of improvement
- Address any findings or recommendations from previous audits or inspections
- Communicate with the auditor in advance and confirm the scope, schedule, and expectations of the audit
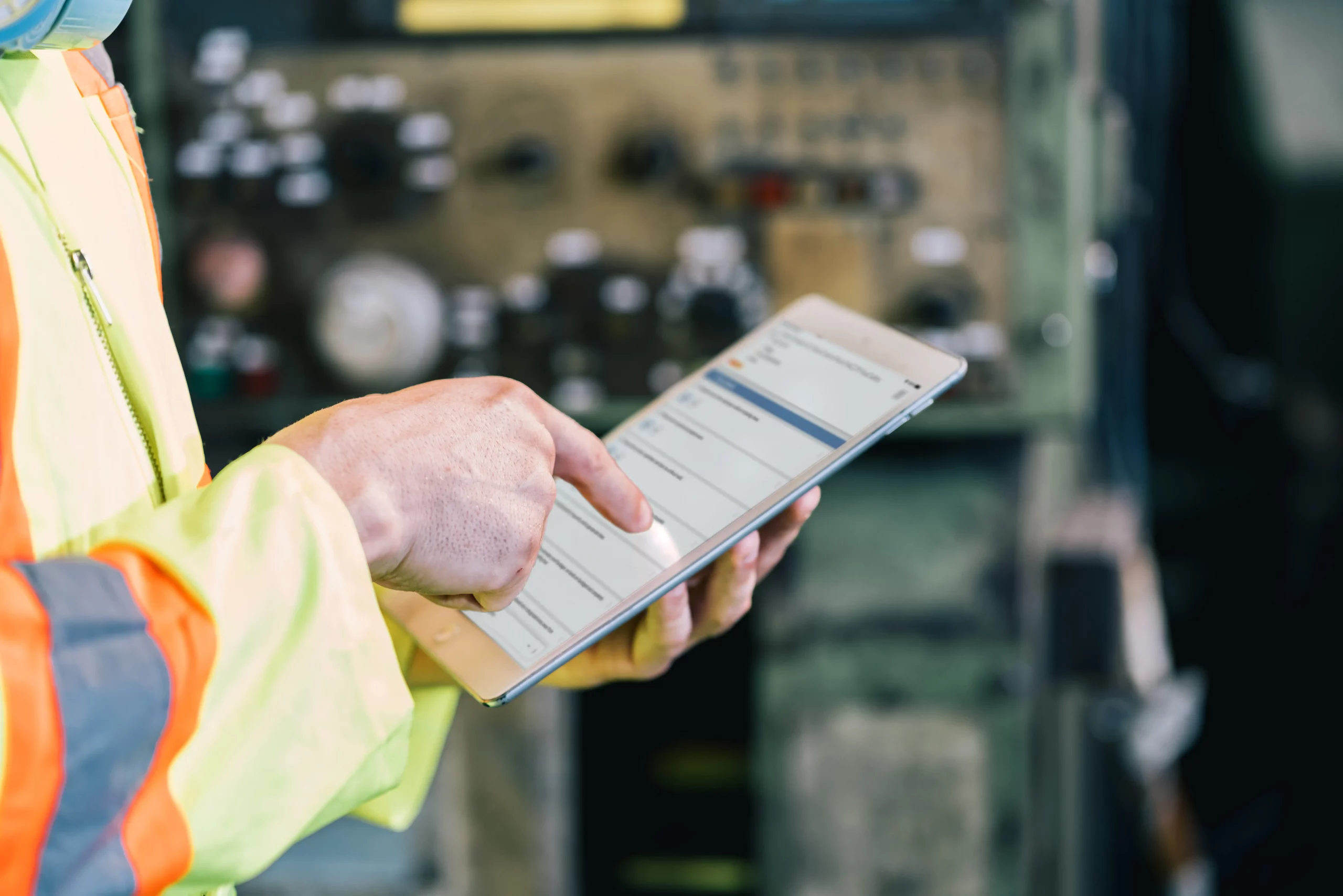
30+ Audit and inspection checklists free for download.
How to Implement GMP Training for Your Staff
GMP training is an essential component of your GMP program that ensures your staff has the knowledge and skills to perform their duties in accordance with the GMP standards for food safety. To implement GMP training for your staff, you should:
- Conduct a training needs analysis to determine who needs to be trained, what they need to be trained on, how they need to be trained, when they need to be trained, and how their training will be evaluated
- Develop a training plan that outlines the objectives, content, methods, resources, schedule, and assessment of your training program
- Deliver the training using various techniques such as lectures, demonstrations, videos, quizzes, games, etc.
- Evaluate the effectiveness of your training using various methods such as tests, surveys, observations, feedback, etc.
- Record and document your training activities and results
- Review and update your training program periodically to reflect any changes in regulations, processes, or products
Food Safety First
GMP and cGMP are key components of effective food safety and food safety program. By regularly reviewing these requirements for updates, and assessing current compliance with in-depth checklists and auditing processes to identify potential concerns, food manufacturers and food businesses can streamline operations, ensure food standards are met, and remain confident in food safety frameworks.
Ready to boost GMP best practices? Take on food safety with Certainty.
You may also be interested in:
Certainty Helps with Covid19 Pandemic Health & Safety Response At An Award-Winning Grocer
Using Certainty as a solution to manage GMP audits and food safety