Table of contents
To manage supply chain challenges and ensure regulatory compliance, lean manufacturing has become commonplace for organizations. The approach isn’t new — American industrialists of the early 20th century employed lean processes that focused on reducing waste and improving efficiency as a way to increase overall value.
The original 5S methodology, meanwhile, emerged as a companion to lean management thanks to Sakichi Toyoda, founder of the Toyota production system and often called the “father of the Japanese industrial revolution.” With five simple, alliterative steps, 5S made it possible to further improve production while driving increased efficiency with a focus on continuous improvement. 6S Lean takes things a step further by adding a 6th ‘S’: Safety.
What is 6S Lean?
6S lean manufacturing combines the five key tenants of 5S — sort, straighten, shine, standardize, and sustain — with safety. The goal of 6S is to ensure that safety is a part of all lean manufacturing processes from end to end, in turn reducing the risk of accidents and limiting the amount of production downtime.
The 6S framework is often imagined as a circle with the five core tenants around the edge and safety in the middle. While some critics of the 6S approach argue that safety should simply be another “step” in the process, the center position of safety in 6S lean speaks to its role across all operations from start to finish.
Key Components of the 6S Lean Framework
There are six key components of the 6S methodology:
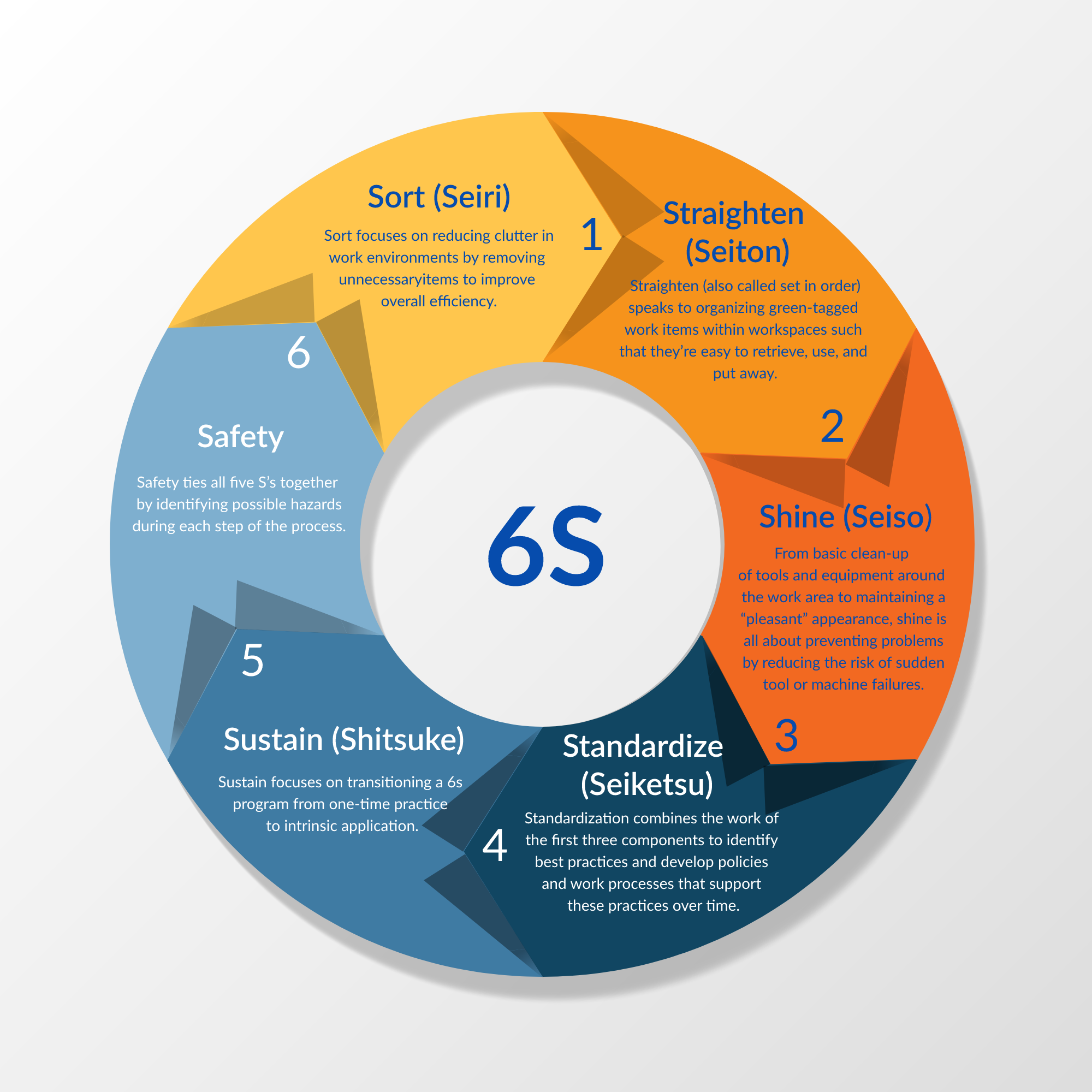
Sort (Seiri)
Sort focuses on reducing clutter in work environments by removing unnecessary items to improve overall efficiency. Items are often “tagged” by the color — green-tagged items stay, red-tagged items are immediately removed and yellow-tagged items are stored for later use.
Straighten (Seiton)
Straighten (also called ‘set in order’) speaks to organizing green-tagged work items within workspaces such that they’re easy to retrieve, use, and put away. By creating a systematic approach to production line processes, companies can increase accessibility and boost overall efficiency with an organized workplace.
Shine (Seiso)
Cleaning is the priority in this 6S component. From basic clean-up of tools and equipment around the work area to maintaining a “pleasant” appearance, Shine is all about preventing problems by reducing the risk of sudden tool or machine failures. This component also speaks to building proactive and preventative processes that help workspaces stay clean over the long term.
Standardize (Seiketsu)
Standardization combines the work of the first three components to identify best practices and develop policies and work processes that support these practices over time. Standardization may include a written code of conduct, on-site visual reminders such as signs or posters, and regular site inspections.
Sustain (Shitsuke)
Sustain focuses on transitioning a 6s program from one-time practice to intrinsic application. This requires continual monitoring and evaluation until processes become second nature.
Safety
Safety ties all five S’s together by identifying possible hazards during each step of the process and developing methods to eliminate the hazards and keep workers safe — and productive.
6S Lean vs. Lean Six Sigma
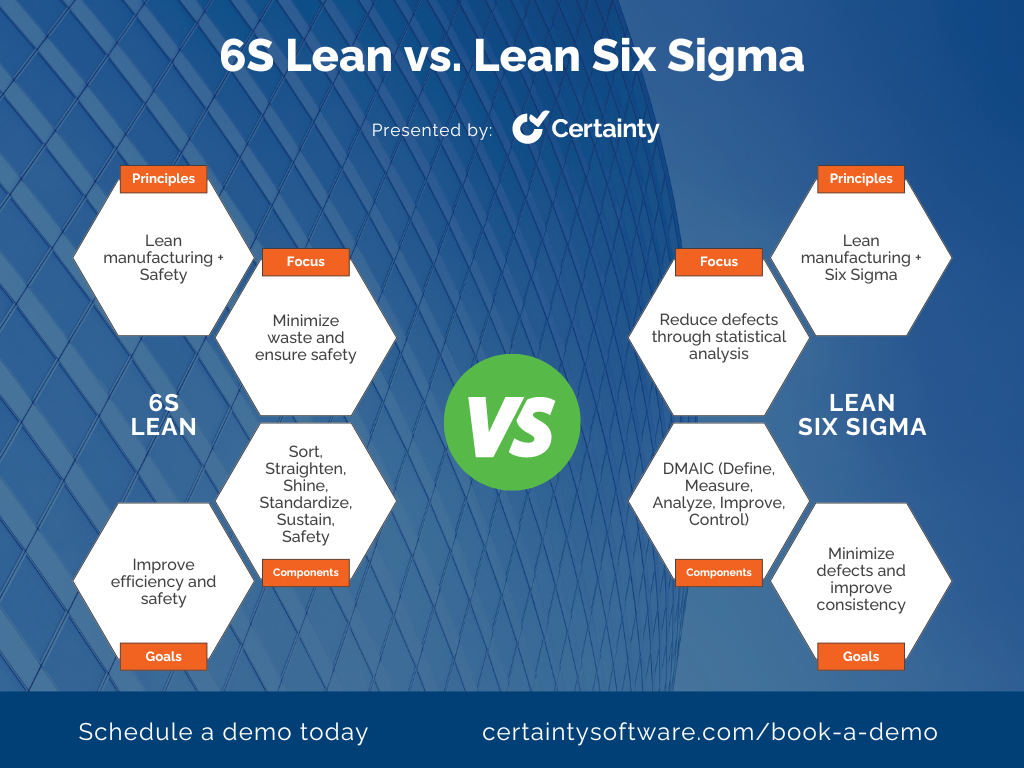
Both the 6S Lean and Lean Six Sigma frameworks are geared toward enhancing the effectiveness, productivity, and security of business operations. However, their methods and objectives differ significantly in some important ways.
In 6S Lean, the emphasis is on minimizing waste and improving the flow of value from the viewpoint of the customer. It combines safety as its guiding principle with the five steps of Sort, Straighten, Shine, Standardize, and Sustain to produce a tidy, orderly workplace. To keep the desired condition, 6S Lean relies on visible management, teamwork, and continual development.
On the other hand, Lean Six Sigma focuses on lowering variation and flaws in the results of work operations. The same six processes as 6S slim are used, however, statistics is included as a seventh step. 6S Lean Six Sigma measures, monitors, and enhances the quality of work processes using statistical techniques such as data collecting, analysis, and control charts. To reach higher quality standards, Lean Six Sigma uses data-driven decision-making, problem-solving tools, and customer feedback.
Companies can achieve operational excellence and customer satisfaction by combining the advantages of 6S Lean and Lean Six Sigma. However, all organizational levels must be committed, trained, and supportive in order to successfully execute these frameworks.
6S Lean Benefits
Applying the 6S system framework to your organization can help drive two key outcomes: Speed and safety. Speed stems from the application of 5S processes — if production line stations are sorted, straightened, shined, and standardized and these ideals are maintained, overall efficiency increases even as waste decreases, in turn leading to faster production processes with no decrease in quality.
Adding the additional “S” of workplace safety, meanwhile, helps ensure that the focus of every step in the 5S circle is underpinned by safety. Consider the “straighten” phase of 5S. While establishing systematic ways of storing and retrieving tools and items offers benefits for efficiency, safety considers how this organization may impact employees — are certain tools or equipment suddenly out of reach? Will new processes require staff to sit, stand, or turn in odd ways that could have negative impacts over time? By incorporating safety, companies can combine the health of the business with the health of individuals to benefit both.
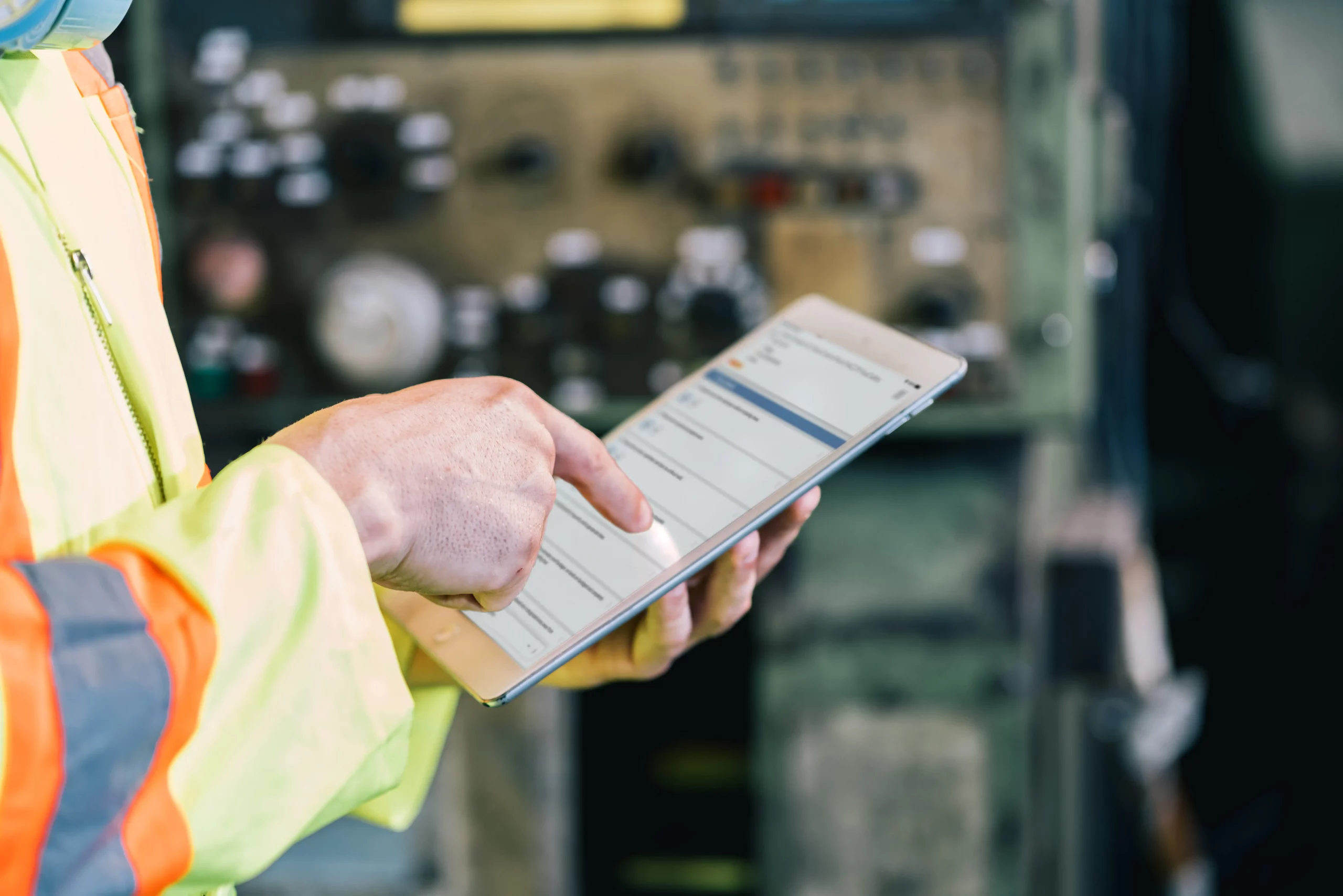
30+ Audit and inspection checklists free for download.
6S Implementation Challenges
Implementing 6S lean can be a rewarding but challenging process for any organization. Some of the common obstacles that may hinder the success of 6S lean are:
Resistance to change
Some employees could be hesitant or dubious about implementing new working practices, especially if they are accustomed to the outdated practices or feel secure in the status quo. To get through this obstacle, it’s crucial to routinely and clearly communicate the advantages and objectives of 6S lean, as well as to involve staff members in the preparation and implementation of 6S activities. Offering rewards, praise, and feedback can also encourage and involve staff members in the transition process.
Learn how to address communication challenges in audits and inspections with these 10 strategies.
Lack of training
Some personnel might lack the ability to effectively apply 6S lean, such as the ability to sort, straighten, shine, standardize, sustain, and apply statistics. Employees at all levels of the business need to get proper and continuing coaching in order to overcome this hurdle. Employees can learn and use 6S principles and techniques in their workplace by using visual aids, presentations, simulations, and case studies.
Insufficient resources
Some businesses might not have the resources they need to implement 6S lean activities like audits, data collection, or the acquisition of new tools or materials. Prioritizing and allocating resources to the demands and effects of 6S initiatives is essential to removing this obstacle. Resource shortages can also be overcome by seeking outside assistance or funding, making the most of already available resources, or coming up with innovative solutions.
How Certainty Improves 6S Management
To deliver on the potential of 6S Lean, organizations require frameworks that support the details and documentation necessary to capture and compare operational data. For example, if specific processes aren’t working as intended — if they’re putting workers at risk or resulting in additional waste — companies need streamlined ways to record what’s wrong and create a solution. 6S Lean software offers a way to centralize and streamline the implementation of this process.
As a result, robust software tools for 6S Lean implementation are critical. Paired with in-depth evaluation criteria along with lean 6S checklists and templates, companies can pinpoint where processes aren’t living up to 6S expectations and make data-driven changes that benefit staff, stakeholders, and customers.
Ready to make the shift to 6S? Start with Certainty.
FAQs About 6S Lean
What is 6S Lean?
6S Lean is an extension of the 5S methodology, incorporating safety to streamline efficiency and reduce waste.
What are the key components of 6S Lean?
The six components are Sort, Straighten, Shine, Standardize, Sustain, and Safety.
How does 6S Lean differ from Lean Six Sigma?
6S focuses on safety and lean principles, while Lean Six Sigma adds statistical analysis to minimize defects.
What challenges might organizations face when implementing 6S Lean?
Common challenges include resistance to change, lack of training, and insufficient resources.
How can Certainty help with 6S Lean implementation?
Certainty provides powerful tools for 6S Lean implementation. Features include centralized data collection, customizable checklists, and real-time reporting to streamline audits, identify safety risks, and enhance continuous improvement efforts. With these tools, organizations can improve safety, reduce waste, and achieve compliance efficiently.
You may also be interested in: