Modernizing Quality Assurance and Control at Rocky Brands
Founded in 1932 Rocky Brands, Inc. designs, develops, manufactures and markets premium quality outdoor, work, western, duty and military footwear as well as outdoor and work apparel and accessories. Headquarters in Nelsonville, Ohio with manufacturing facilities in Puerto Rico and the Dominican Republic, Rocky Brands employs over 2,300 people worldwide.
As an ISO 9001-2015 certified facility, Rocky Brands manufactures products that meet strict quality and process controls. Quality Assurance is a top priority that is vitally important at every stage of the manufacturing process: from raw materials inspection to various manufacturing processes and approving products for shipping.
Legacy Tracking of Quality Assurance, Compliance, and Safety
Manual checklists and handwritten reports were previously used to track compliance and report issues. These paper reports were then digitized, which was a time-consuming process. This process also meant that there was ample room for human error and that reports were not available in real-time.
In order to upgrade this quality assurance system, several changes had to take place at Rocky Brands.
- New infrastructure needed to be established so that Wi-Fi was accessible in all facilities
- Tablets needed to be issued to plant associates to replace traditional handwritten data input methods
- Associates needed to be trained on the new technology and input processes
These changes came with their own set of challenges. For instance, upgrading the Wi-Fi infrastructure meant that the IT department had to be involved, which brings with it the challenge of communicating and coordinating between departments and teams. Furthermore, some staff were not familiar with tablet technology, which meant a steeper learning curve, and a more difficult transition away from the paper-based legacy system.
Implementing a Modern Quality Assurance System
Rocky Brands decided to upgrade their Quality Assurance and Control systems and use Certain Software, a flexible, powerful, and trusted enterprise-level audit and inspection management solution. With Certainty, Rocky Brands was able to move away from manual data entry all audit and inspection data was now instantly available online for management and reporting across the organization.
It also resulted in huge advantages in the way that Rocky Brands communicated: any quality nonconformities are now immediately communicated, reported, and corrected in real-team. Instead of finding forms, filling out the registers, carrying clip boards, and digitizing information, associates are now able to report everything on a tablet in real-time and add photographic evidence on the go as well.
This has freed up time for associates to prevent quality issues and check the process instead of being tied up in paper management and printing. Real-time information is also now available for plant managers and supervisors to make decisions and corrections on-the-go with reliable data.
Rocky Brands Quality Assurance Manager, Pedro Tapia, remarks that as an added bonus, the environment is happier too, with hundreds of trees being saved by eliminating the use of paper and printers. Pedro adds:
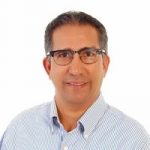
I strongly recommend that any company that is currently filling out reports manually, that perform process checks, quality inspection, and that uses check boxes in their day to day activity, takes a serious look at Certainty as a solution to automate and collect valuable data in real time.
Rocky Brands is now using Certainty Software to perform process inspections, material inspections, status inspections, final audits, and more. By downloading reports to Excel they are able to further analyse and act on their data. The applications are endless.
If you’re interested in learning about how Certainty Software can help your quality assurance and control processes, contact us today!