Table of contents
Did you know the average manufacturing plant operates at only 60 percent of its full potential? That means that 40 percent of the time is wasted due to equipment breakdowns, production bottlenecks, quality defects, and other inefficiencies. Imagine how productive, profitable, and competitive your manufacturing business could be if you eliminate these losses and optimize your equipment performance.
That’s where OEE, or Overall Equipment Effectiveness, comes in. OEE is a metric that quantifies how effectively a manufacturing process uses its equipment to produce quality products. It helps manufacturers measure, monitor, and improve their manufacturing efficiency in real-time, resulting in significant benefits such as reduced costs, enhanced quality, increased customer demand, and improved competitive advantage.
But what exactly is OEE, and how can it be calculated and optimized for manufacturing operations? This blog post will provide you with a comprehensive guide to understanding the meaning of OEE specifically in manufacturing and how it can transform your business performance.
Understanding OEE
OEE stands for Overall Equipment Effectiveness. It is a metric that quantifies how effectively a manufacturing process uses its equipment to produce quality products. It is calculated by multiplying three factors: Availability, Performance, and Quality.
- Availability measures the percentage of time that the equipment is ready and able to run, excluding planned and unplanned downtime.
- Performance measures the percentage of actual output that the equipment produces compared to its maximum possible output, excluding speed losses.
- Quality measures the percentage of good products that the equipment produces out of the total output, excluding quality defects.
OEE = Availability x Performance x Quality
By multiplying these three factors, OEE provides a holistic view of equipment performance and overall manufacturing efficiency. It reveals how much of the planned production time is productive and how much is wasted due to various losses.
OEE can range from 0% to 100%, where 0% means no production at all and 100% means perfect production with no losses. However, achieving 100% OEE is practically impossible in reality, as there will always be some degree of variation and imperfection in any process. A more realistic benchmark for world-class OEE is 85%, which indicates a highly efficient and optimized manufacturing process.
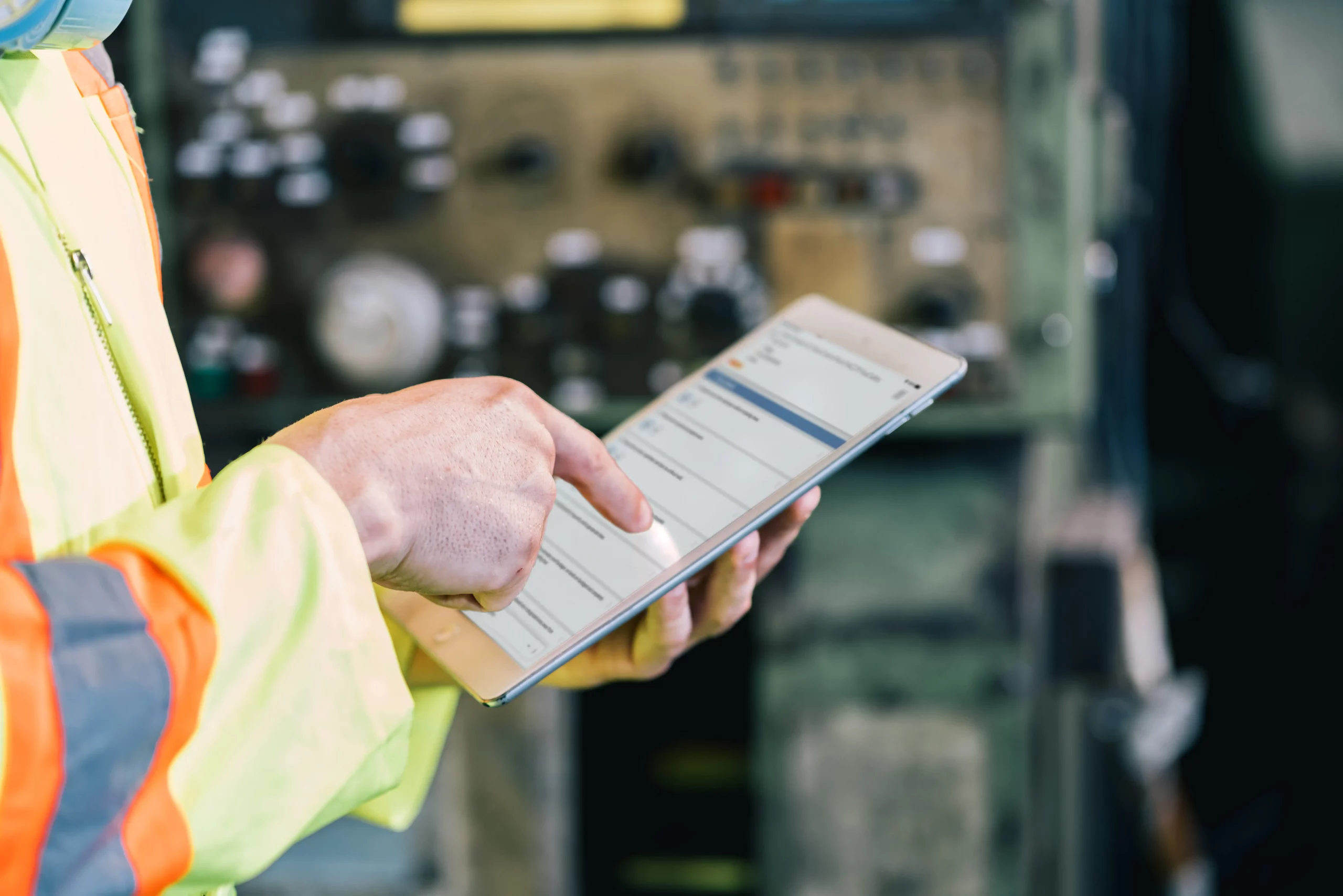
30+ Audit and inspection checklists free for download.
The Significance of OEE in Manufacturing
OEE is more than just a number. It is a powerful indicator of the health and functionality of your manufacturing process. By tracking and improving OEE, you can achieve significant benefits for your business, such as:
- Reduced production costs: By identifying and eliminating sources of waste and inefficiency in your process, you can lower your operating expenses and increase your profit margins.
- Enhanced product quality: By ensuring that your equipment produces consistent and defect-free products, you can improve your customer satisfaction and loyalty, as well as reduce rework and scrap costs.
- Increased customer demand: By optimizing your equipment output and throughput, you can meet or exceed your customer expectations and orders, as well as capture new market opportunities.
- Improved competitive advantage: By maximizing your productivity and quality, you can gain an edge over your competitors and establish yourself as a leader in your industry.
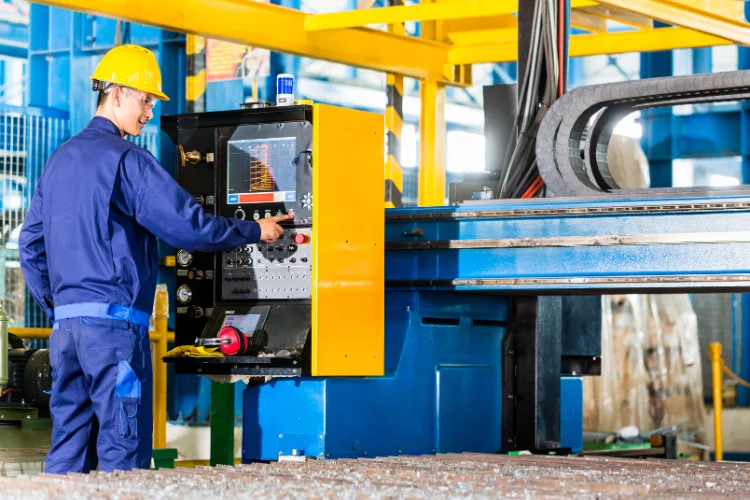
Calculating OEE for Manufacturing Operations
Now that you understand what OEE is and why it is important, you may be wondering how to calculate it for your manufacturing processes. The good news is that the OEE calculation is not complicated, as long as you have the right data and formula.
To calculate OEE, you need to measure four variables:
- Planned Production Time: The total time that your equipment is scheduled to run, excluding planned stops such as breaks, maintenance, and changeovers.
- Run Time: The actual time that your equipment is running, excluding unplanned stops such as breakdowns, power outages, and material shortages.
- Ideal Cycle Time: The fastest possible time that your equipment can produce one unit of output, assuming optimal conditions and speed.
- Total Units: The total number of units that your equipment produces during the run time, including good and bad products.
Using these variables, you can calculate the three factors of OEE:
- Availability = Run Time / Planned Production Time
- Performance = (Total Units x Ideal Cycle Time) / Run Time
- Quality = Good Units / Total Units
Then, you can multiply these factors to get the OEE:
- OEE = Availability x Performance x Quality
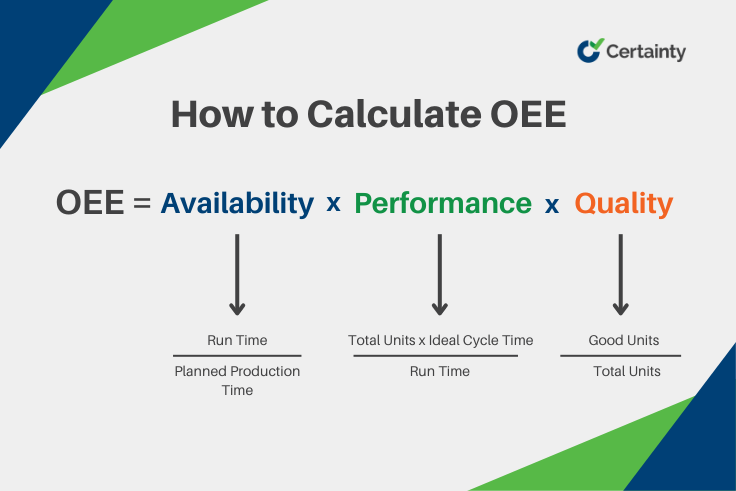
OEE Calculation Example
To illustrate how this works, let’s look at a simple example. Suppose you have a manufacturing process that produces widgets. The planned production time for one shift is 8 hours (480 minutes). The run time for the shift is 7 hours (420 minutes), due to 1 hour of unplanned downtime. The ideal cycle time for producing one widget is 1 minute. The total number of widgets produced during the run time is 350, out of which 300 are good and 50 are bad.
Using these data, you can calculate the OEE as follows:
- Availability = 420 / 480 = 0.875 or 87.5%
- Performance = (350 x 1) / 420 = 0.833 or 83.3%
- Quality = 300 / 350 = 0.857 or 85.7%
- OEE = 0.875 x 0.833 x 0.857 = 0.624 or 62.4%
This means that your manufacturing process is operating at 62.4% of its full potential, which is below the world-class benchmark of 85%. This indicates that there is room for improvement in your process, especially in reducing downtime and quality defects.
Strategies to Optimize OEE in Manufacturing
Calculating OEE is only the first step in optimizing your manufacturing efficiency. The next step is to implement strategies that can help you improve your OEE score and achieve your business goals. Here are some of the most effective strategies that you can use to optimize OEE in manufacturing:
- Predictive maintenance: Use data and analytics to monitor the condition and performance of your equipment and predict when it needs maintenance or repair. This can help you prevent breakdowns, reduce downtime, and extend the lifespan of your equipment.
If you need a checklist template to help compile quality-related audit and inspection data, try our free-to-download Gemba Walk Checklist.
- Process automation: Implement technology such as sensors, robots, and software to automate repetitive or complex tasks in your manufacturing process. This can help you increase output, speed, and accuracy, as well as reduce human errors and variability.
- Equipment upgrades: Invest in new or improved equipment that can enhance your manufacturing capabilities and efficiency. This can help you produce more products with less resources, time, and waste.
- Workforce engagement: Motivate and empower your employees to participate in improving your manufacturing process and OEE performance. This can help you foster a culture of continuous improvement, innovation, and collaboration among your staff.
- Training and education: Provide your employees with the necessary skills and knowledge to operate and maintain your equipment effectively and safely. This can help you improve their competence, confidence, and productivity.
- Best practices and standards: Adopt proven methods and guidelines for optimizing your manufacturing process and OEE performance. This can help you benchmark your performance against industry standards and learn from best practices.
Overcoming Manufacturing Challenges with OEE
Manufacturing is not without its challenges. Every day, manufacturers face various obstacles that can hinder their production efficiency and quality. Some of the most common manufacturing challenges are:
- Equipment breakdowns: These are unplanned stops that occur when a machine or component fails or malfunctions due to wear and tear, improper operation, or external factors.
- Production bottlenecks: These are points in the production line where the flow of work is slowed down or stopped due to insufficient capacity, resources, or coordination.
- Quality defects: These are products that do not meet the quality standards or specifications due to faulty materials, processes, or equipment.
These challenges can hurt your OEE score and your business performance. They can cause delays, waste, rework, customer complaints, and lost revenue. How can you overcome these challenges with OEE?
The key is to use OEE as a diagnostic tool to identify the root causes of these challenges and implement corrective actions. For example:
- To prevent equipment breakdowns, you can use OEE to monitor the availability and performance of your equipment and detect any signs of deterioration or malfunction. You can then perform predictive maintenance or repair before the equipment fails, minimizing downtime and costs.
- To eliminate production bottlenecks, you can use OEE to analyze the throughput and capacity of each stage of your production line and pinpoint where the bottlenecks are occurring. You can then optimize the workflow, balance the load, or increase the resources to eliminate the bottlenecks and improve the output.
- To reduce quality defects, you can use OEE to measure the quality and consistency of your products and identify any sources of variation or error. You can then improve the materials, processes, or equipment to ensure that your products meet the quality standards and specifications.
Leveraging Certainty Software for Manufacturing
If you are looking for a powerful tool to optimize OEE in manufacturing, look no further than Certainty Software. Certainty Software is a cloud-based software solution that streamlines audit and inspection data collection, analysis, and reporting in all industries including manufacturing.
With Certainty Software, you can:
- Easily collect quality audit and inspection data using mobile devices;
- Visualize and analyze your data using interactive dashboards, charts, graphs, and reports.
- Identify trends, patterns, anomalies, and opportunities for improvement using advanced analytics and artificial intelligence.
- Share and communicate your data and insights with your team, management, or stakeholders using secure cloud access and collaboration features.
Certainty Software is designed to cater to the specific needs of manufacturing operations. It has a user-friendly interface and customizable features that allow you to tailor it to your industry, process, equipment, and goals. Whether you want to monitor a single machine or a complex production line, Certainty Software can help you optimize your OEE performance and achieve manufacturing excellence.
If you are interested in trying out Certainty Software or seeking professional consultation for implementing OEE in your manufacturing processes, please contact us today. We would love to hear from you and help you take your manufacturing efficiency to the next level.
You may also be interested in: