Whether it’s a remote oil extraction site, an underground mechanical room in a legacy factory, or a supplier facility in a low-infrastructure region, field inspectors are regularly deployed into environments where Wi-Fi is unavailable and cellular coverage is patchy at best. […]
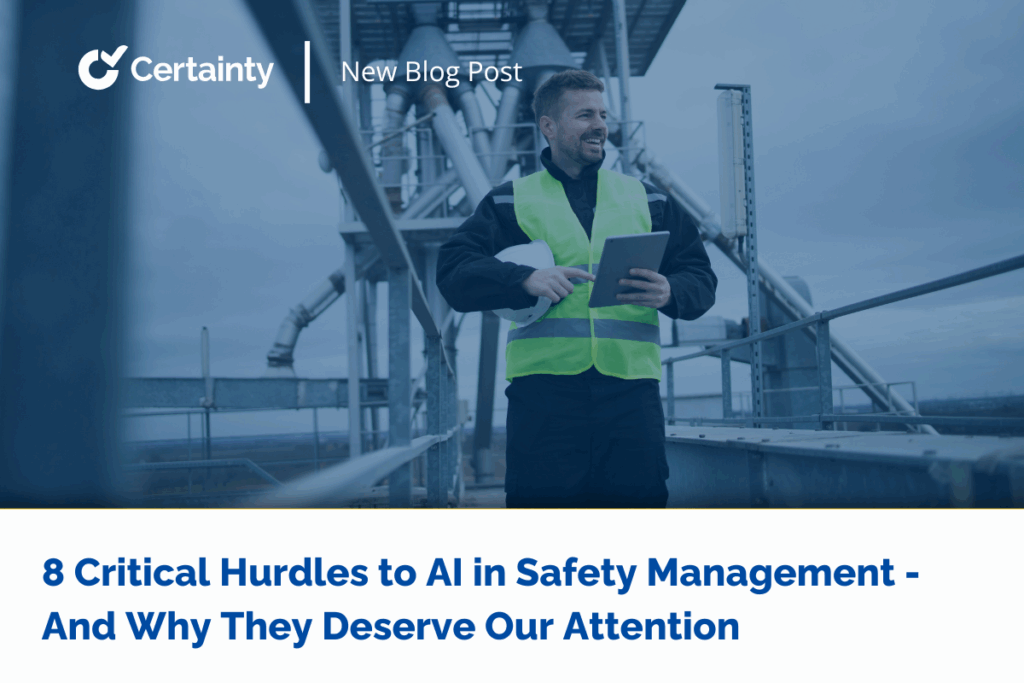
8 Critical Hurdles to AI in Safety Management – And Why They Deserve Our Attention
Drawing on research, market analysis, and the experience of practitioners and vendors in the safety tech ecosystem, the following are eight of the most formidable and most frequently encountered hurdles to AI adoption in safety management. […]
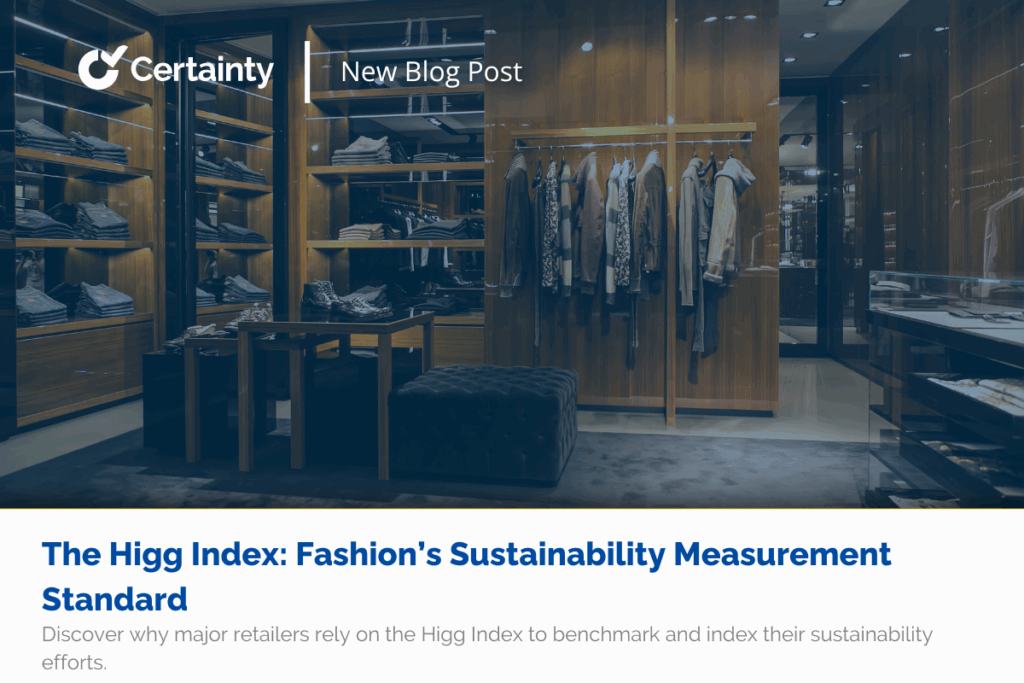
The Higg Index: Fashion’s Sustainability Measurement Standard
Discover why major retailers rely on the Higg Index to benchmark and index their sustainability efforts. […]
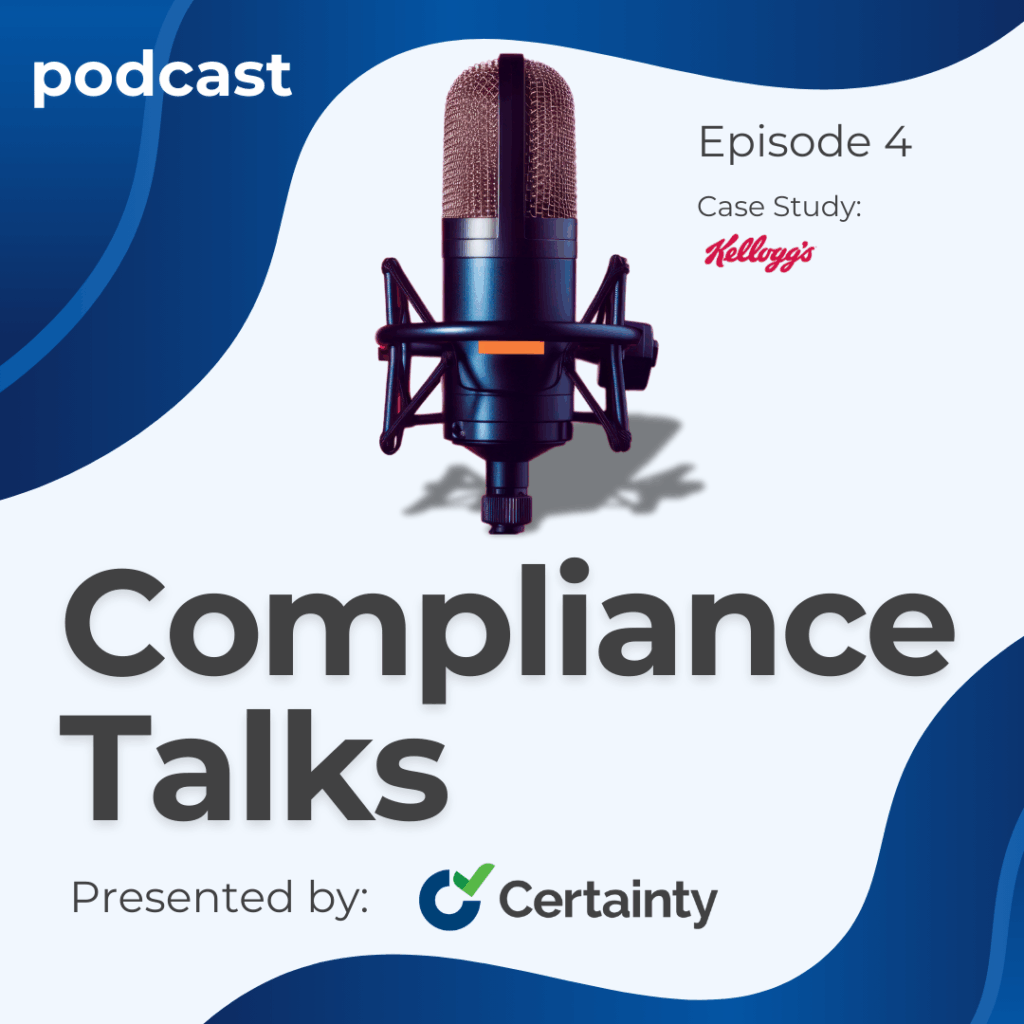
[Podcast] Compliance Talks Episode 4: How Kellogg’s Manages Global Behavior Based Safety Observations With Certainty
In Episode 4 of our Compliance Talks podcast series, we explore how Kellogg’s grew its BBS observation management by using Certainty. From originally relying on outdated paper-based forms, see how Kellogg’s enhanced visibility, gained better insights, and eased safety management through Certainty’s digital tools. […]
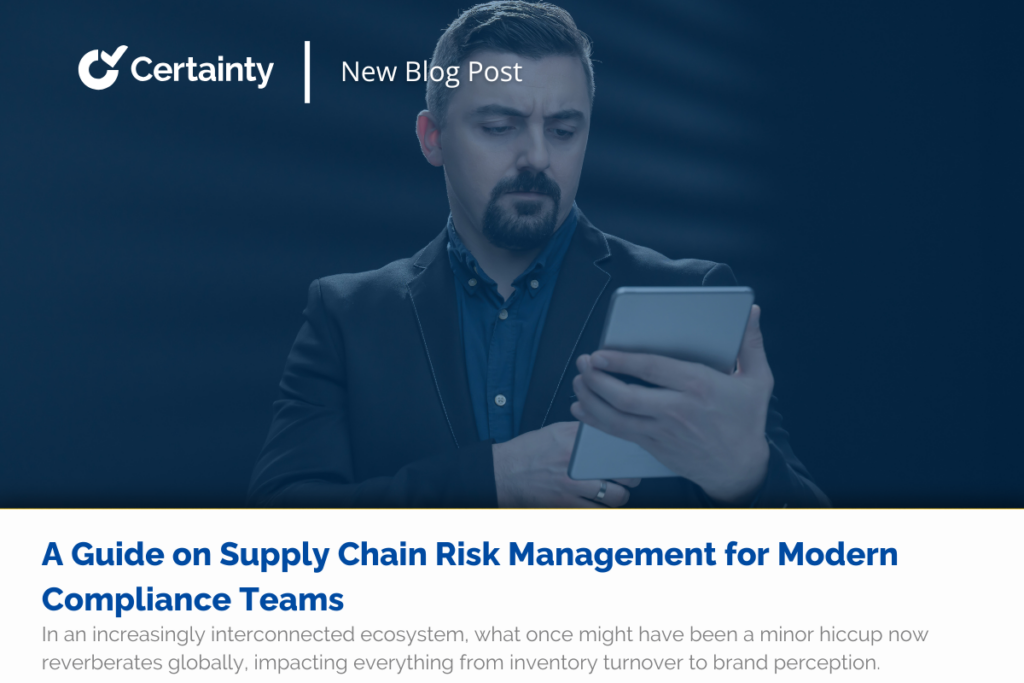
A Guide to Supply Chain Risk Management for Modern Compliance Teams
For compliance leaders, proactive supply chain risk management shifts from minimizing loss to creating an opportunity to build an adaptable and accountable supply network. One that is ready to withstand volatility without compromising performance. […]
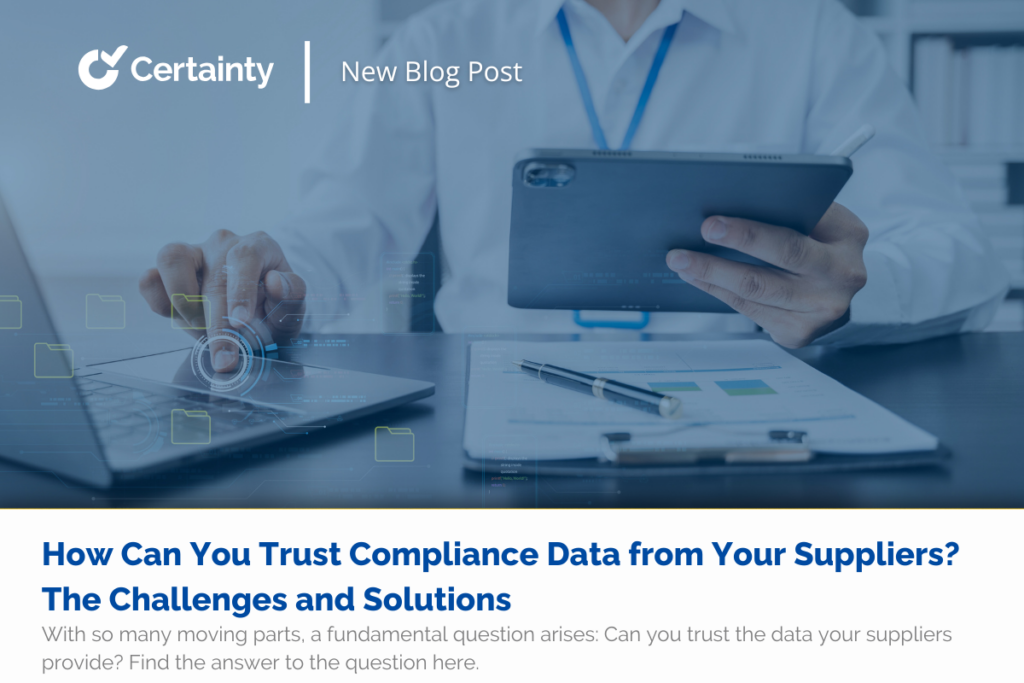
How Can You Trust Compliance Data from Your Suppliers? The Challenges and Solutions
With so many moving parts, a fundamental question arises: Can you trust the data your suppliers provide? Find the answer to the question here. […]
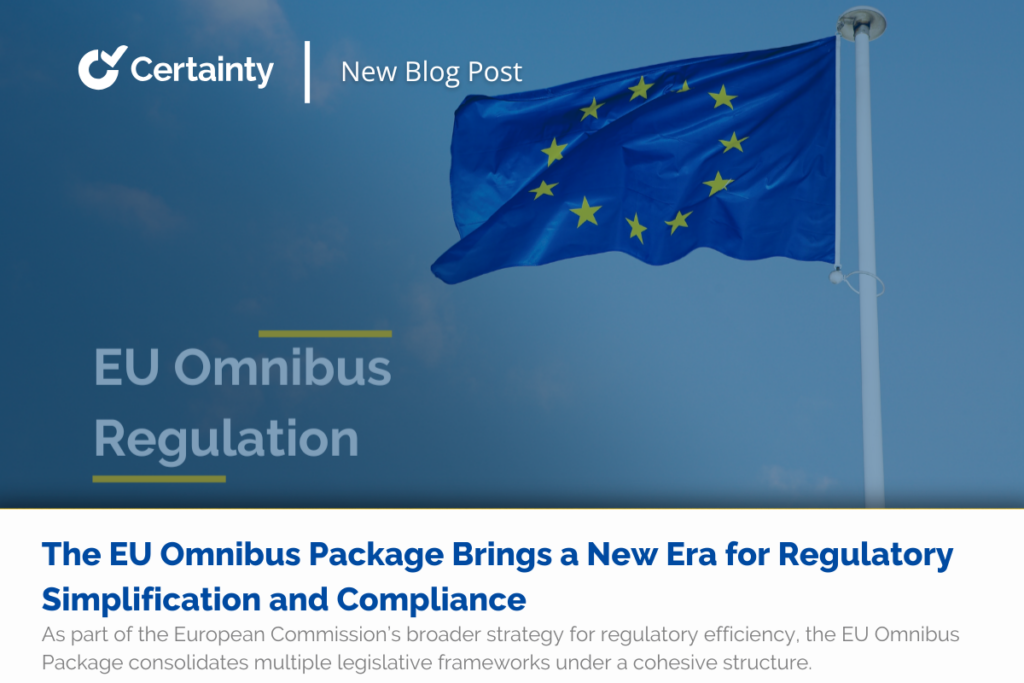
The EU Omnibus Package Brings a New Era for Regulatory Simplification and Compliance
As part of the European Commission’s broader strategy for regulatory efficiency, the EU Omnibus Package consolidates multiple legislative frameworks under a cohesive structure. Covering areas such as corporate governance, consumer protection, sustainability, and compliance, this initiative simplifies the regulatory landscape without diluting its effectiveness. […]
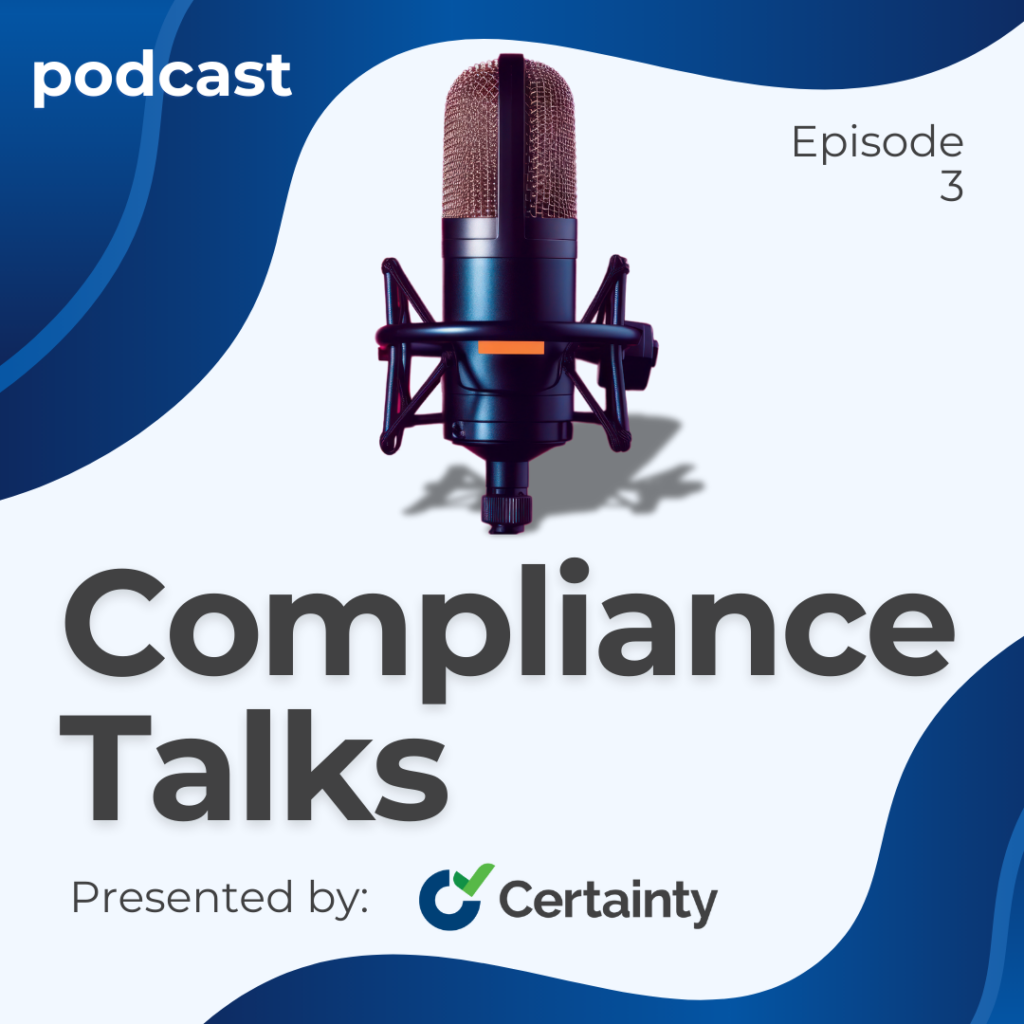
[Podcast] Compliance Talks Episode 3: The Role of Supplier Engagement in Supply Chain Sustainability
In Episode 3 of our Compliance Talks podcast series, we delve into the important role of engaging suppliers in achieving supply chain sustainability. Read on to discover the key takeaways from this episode and learn how to effectively align your suppliers’ practices with your sustainability goals. […]
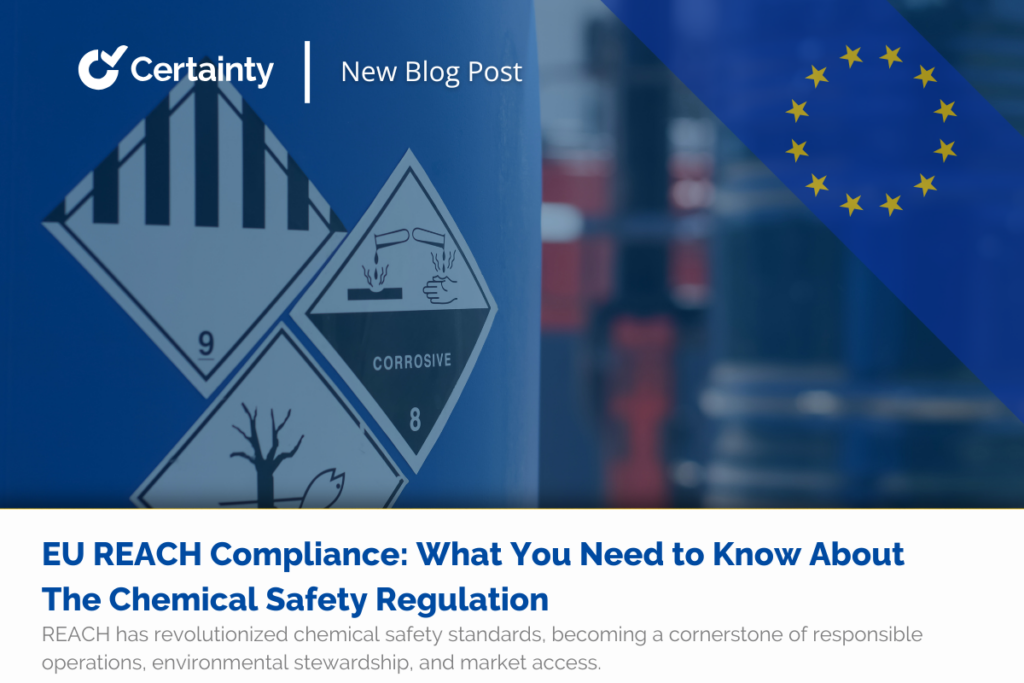
EU REACH Compliance: What You Need to Know About The Chemical Safety Regulation
Introduced in 2007, the European Union’s REACH regulation (Registration, Evaluation, Authorization, and Restriction of Chemicals) revolutionized chemical safety standards, becoming a cornerstone of responsible operations, environmental stewardship, and market access. […]
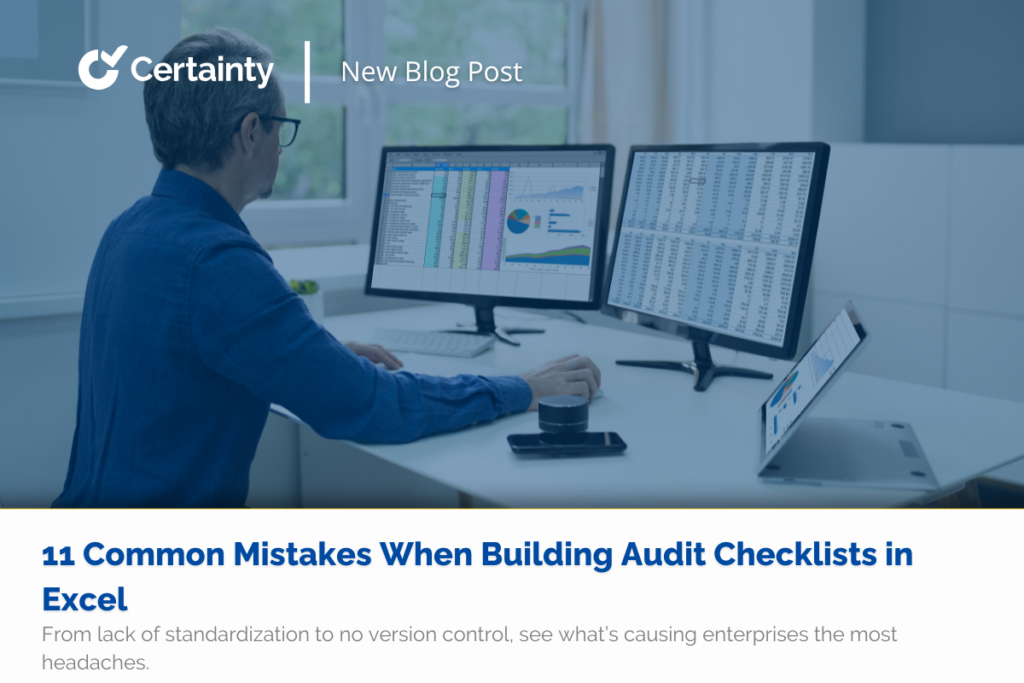
11 Common Mistakes When Building Audit Checklists in Excel
Audit checklists are indispensable tools for ensuring compliance and identifying risks across various industries, but designing them in Excel often introduces inefficiencies and errors. This blog post explores 11 common mistakes made when building audit checklists in Excel and offers actionable solutions, including how Certainty Software’s tools streamline the process and eliminate these pitfalls. […]