Companies lose between 20 and 30 percent of their revenue each year to process inefficiencies. For manufacturing firms, this loss of revenue is often tied to production line processes that are inconsistent, time-consuming, or error-prone. This in turn reduces overall performance and impacts potential profit. An internal Total Quality Management Audit, also known as a TQM Audit, can help organizations pinpoint issues in numerous areas and help reduce the impact of these errors at scale. These areas include the manufacturing processes, supply chain frameworks, and customer experiences to help reduce the impact of these errors at scale.
But what exactly is a TQM audit? Why does it matter? How does it work? And what sets it apart from similar frameworks such as a quality management system (QMS)? Let’s dive in.
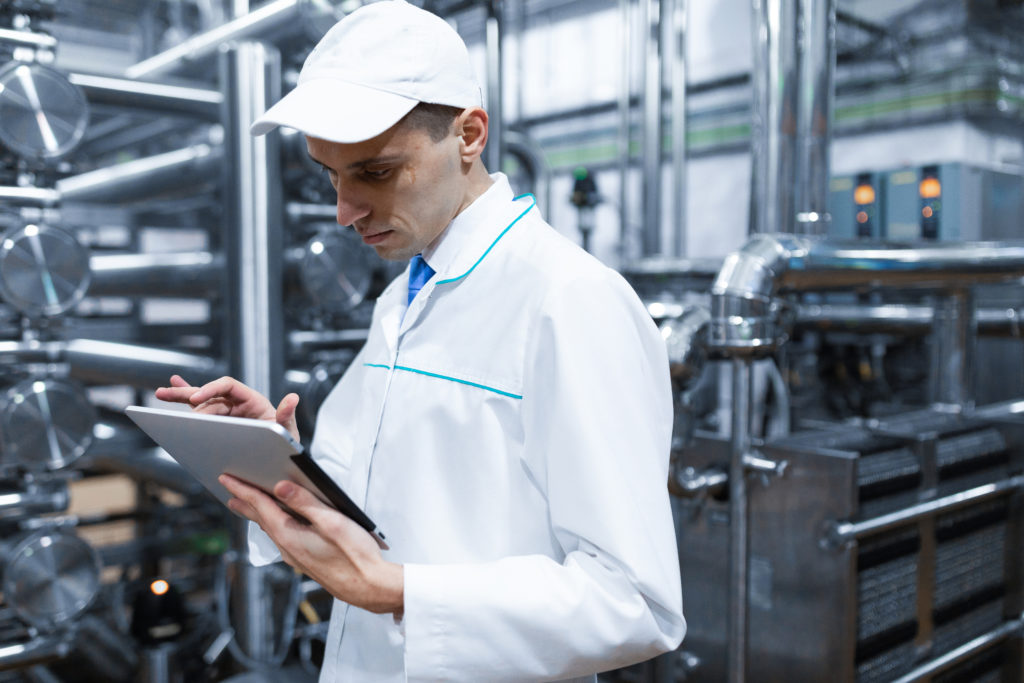
Why Quality Auditing Matters
The concept of quality auditing centers around the idea that the overall quality of processes can always be improved. While this improvement may be incidental at the moment, over time these add up to produce a significant positive business impact. Quality auditing efforts offer a way for company staff — from front-line workers to managers and executives — to achieve shared goals around product and service quality.
What is a Total Quality Management Audit (TQA)?
Originally developed by management consultant William Deming, TQM overlaps with several concepts of the more familiar Six Sigma process. While Six Sigma looks to reduce the total number of defects, TQM focuses on ensuring that company guidelines, standards, and processes effectively reduce the total number of errors.
A TQM audit, therefore, is an evaluation of these processes and standards that include all levels of staff. This is in keeping with the TQM philosophy. This philosophy holds that all parties involved in the creation of a product or service are equally responsible for its success. Worth noting? TQM audits are similar to ISO 9000 and ISO 9001 audits. This is because they share similar priorities such as reducing costs, increasing profits, and ensuring customer satisfaction.
The Key Principles of TQM
Eight TQM principles underpin this methodology:
- Shared responsibility
Team members at all levels of the business who are involved in TQM-audited processes share responsibility for their success.
- Integrated systems
Horizontal integration of systems that underpin key processes helps improve overall functionality and quality control.
- Process-centrality
By prioritizing processes — and the individual steps needed to complete these processes — TQM provides the basis for reliable and repeatable performance measurements and can help improve overall risk management.
- Customer focus
No matter what approach companies take to improve quality, customer requirements are the ultimate judge of TQM’s success or failure. If TQM audits don’t increase customer satisfaction, it’s back to the drawing board.
- A strategic approach to success
Quality improvement doesn’t happen by accident. The creation of strategic, large-scale plans is critical to empowering internal audit functions and ensuring TQM goals are met
- Continuous improvement
TQM recognizes that quality isn’t a static state. Instead, ongoing improvement is necessary to ensure internal controls can keep pace with evolving customer expectations.
- Data-driven decisions
TQM audit activities use collected data to drive decision-making, in turn requiring that companies lay the groundwork for effective data collection and analysis.
- Continual communications
Ongoing communications between staff at all levels are essential for effective TQM; not only does this approach boost overall morale but ensures that all responsible parties are on the same page.
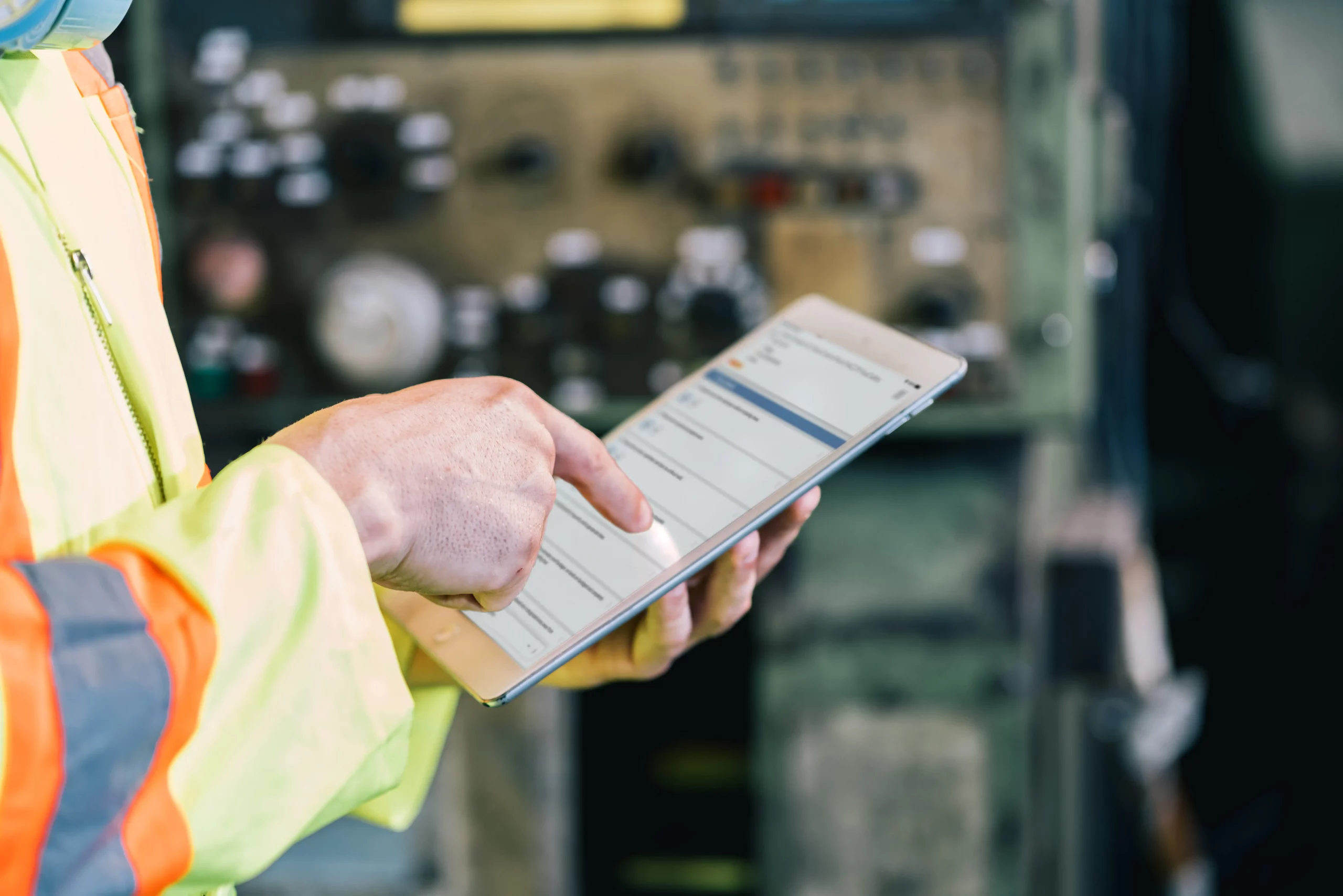
30+ Audit and inspection checklists free for download.
How Does Total Quality Auditing Differ from a Quality Management System (QMS)?
While TQM and QMS both have the words “quality management” in their names, the two concepts aren’t identical. There is significant overlap since both focus on prioritizing the consistency and quality of processes within an organization, but their approach to this goal is different. Where a quality management system is comprised of clearly defined business processes that prioritize the consistency of high-quality product and service delivery, TQM is a larger-scope approach to internal quality audits that looks to drive long-term success by identifying key issues and effectively meeting customer needs.
In practice, both TQM and QMS management practices and quality standards are beneficial for companies looking to improve overall quality. Although their specific focuses differ, these approaches help lay the framework for continually evolving processes capable of dynamically reacting to market changes and customer expectations
You may also be interested in:
Keeping Quality High: The Benefits of a Layered Process Audit
Improving Operational Quality: The Role of Qualitative Risk Assessment