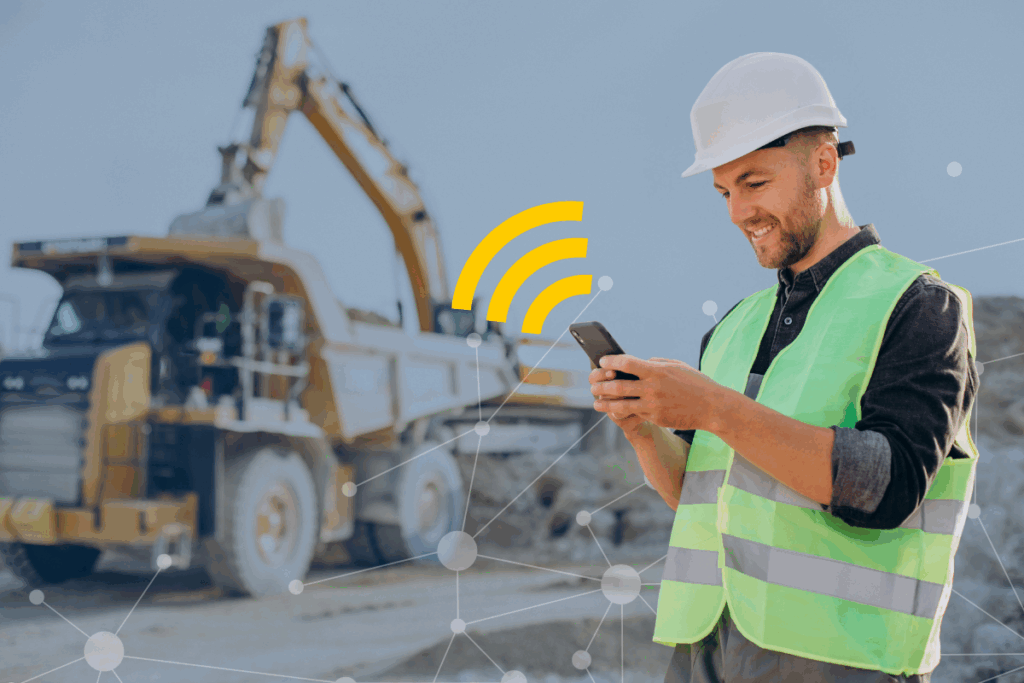
In enterprise environments, inspections serve as critical control points for ensuring compliance, mitigating risk, and driving continuous improvement. But despite the digital transformation sweeping through safety, quality, supply chain, and ESG programs, one truth remains unchanged: connectivity is unreliable in the very places inspections matter most.
Whether it’s a remote oil extraction site, an underground mechanical room in a legacy factory, or a supplier facility in a low-infrastructure region, field inspectors are regularly deployed into environments where Wi-Fi is unavailable and cellular coverage is patchy at best. Mobile devices, often used in these environments, require mobile app functionality that doesn’t depend on uninterrupted access.
In these moments, most inspection software simply stops working. Or worse, it keeps working, but quietly fails to save critical inspection data, leaving teams unaware until it’s too late.
This is where mobile offline capability becomes an operational imperative, not a mere convenience. And for organizations using Certainty, it’s also a solved problem.
Field Reality: Where Connectivity Drops, Risk Rises
Enterprise inspections aren’t tidy. They aren’t done from behind desks. And they don’t unfold in a straight line. They move through confined spaces, outdoor construction sites, across borders and facilities, into temporary job trailers, under power lines, or into walk-in freezers with steel walls that kill every signal.
Consider a plant engineer tasked with performing a weekly safety audit at a legacy steel fabrication facility. The inspection route takes them through several zones, including a production floor enclosed by concrete walls, a storage yard outside the building’s mesh Wi-Fi coverage, and a high-voltage maintenance room in the sub-basement where cellular signal is nonexistent.
At each of these locations, documentation is required that holds specific checklist responses, supporting photo evidence, and corrective actions. Without a reliable offline mode, the mobile application may freeze, refuse to save, or drop attachments mid-inspection. The inspector, now unsure of what’s been logged and what hasn’t, falls back on a paper-based process of using a notebook and camera. Later, they’ll re-enter the findings from memory, guessing timestamps and retroactively linking photos to items.
This isn’t rare. It is an entirely normal day for many field workers and field service technicians. And in every one of these scenarios, the absence of robust offline functionality disrupts workflows, but more importantly, it degrades the integrity of the audit trail.
Offline gaps also interrupt the dynamic logic modern inspections rely on. When branching questions, required evidence capture, or escalation triggers don’t function offline, the form becomes brittle. The inspector may believe the task is complete, unaware that critical logic failed to execute without an active internet connection. That invisibility makes the risk more dangerous.

Access Free Compliance Checklist Templates
The Difference Between Cached Convenience and True Offline Resilience
It’s worth distinguishing between basic offline access and true offline resilience.
Basic access often amounts to a cached form and rudimentary text entry. Photos might be captured but not previewed. Reference materials are often unavailable. Task assignments and validations are suspended. Syncing is unreliable and opaque, depending on the mobile app user to detect whether anything failed to upload, sometimes hours or days later.
In contrast, enterprise-grade mobile inspection apps with offline support treat the app as a fully independent execution environment, capable of executing the entire inspection process without any reliance on an active internet connection. That means:
- Field service workflows remain intact
- Checklists are loaded with logic trees and validations
- Corrective actions can be created and assigned, even if the assignee is offline
- Evidence is linked in real-time to the inspection item, stored in encrypted local memory, and queued for deterministic sync once reconnected.
There’s no ambiguity. When the inspector completes an offline audit, they do so with the same assurance, visibility, and audit trail fidelity as they would in a connected environment. That’s essential for maintaining data accuracy, standardization, and cross-site consistency.
Basic Access
- Cached forms
- Rudimentary text entry
- Photos captured but not previewed
- Unavailable reference materials
- Suspended action assignments and validations
- Unreliable syncing
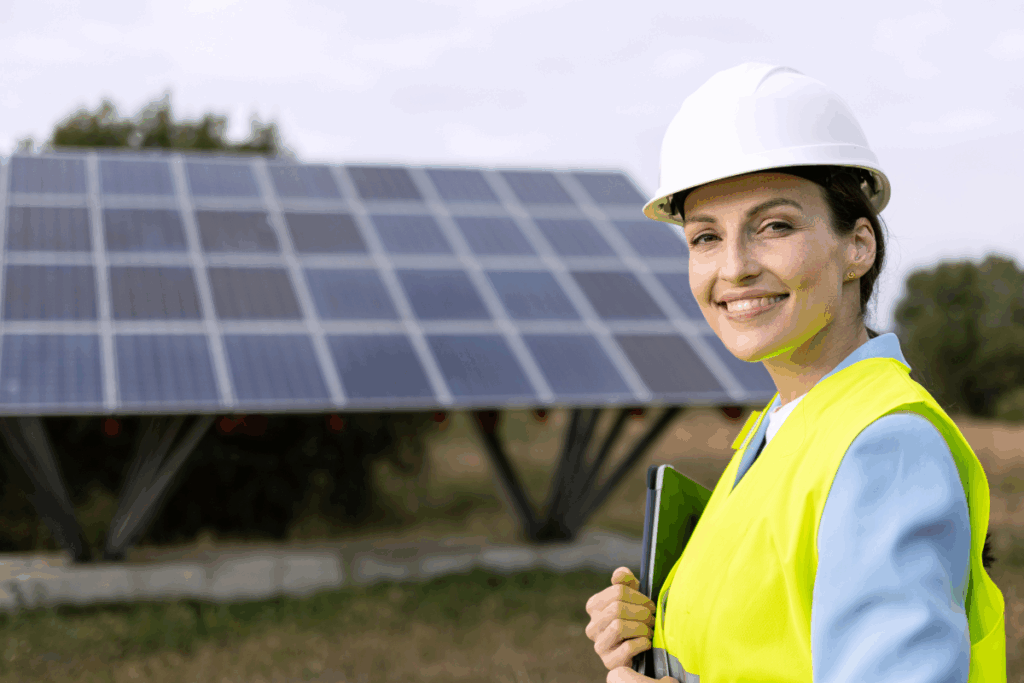
Enterprise Access
- Intact field service workflows
- Checklists loaded with logic trees and validations
- Creatable and assignable offline corrective actions
- Real-time inspection evidence linking
- Stored in encrypted local memory
- Queued sync once reconnected
The Hidden Cost of Incomplete Inspections
Field inspections are often treated as tactical activities, but the collected data they generate feeds directly into operational dashboards, CRM integrations, safety KPIs, ESG reporting, and regulatory filings. When data collection is incomplete due to poor offline support, every downstream process suffers:
- Risk models become unreliable, skewed by missing or inconsistent inputs
- Time-to-resolution metrics are padded with invisible delays and rework
- Issues go unaddressed, as non-conformances may never be logged or escalated
- Regulatory audits reveal broken timestamp sequences or mismatched attachments
- Incident investigations lack a defensible trail, leaving the organization exposed
Even more damaging is the loss of trust. When inspectors no longer believe the system can function offline, they disengage. They resort to time-consuming workarounds and paper-based documentation. Digital records become secondary to manual ones. And as informal systems reappear, field service operations become harder to measure, optimize, and govern.
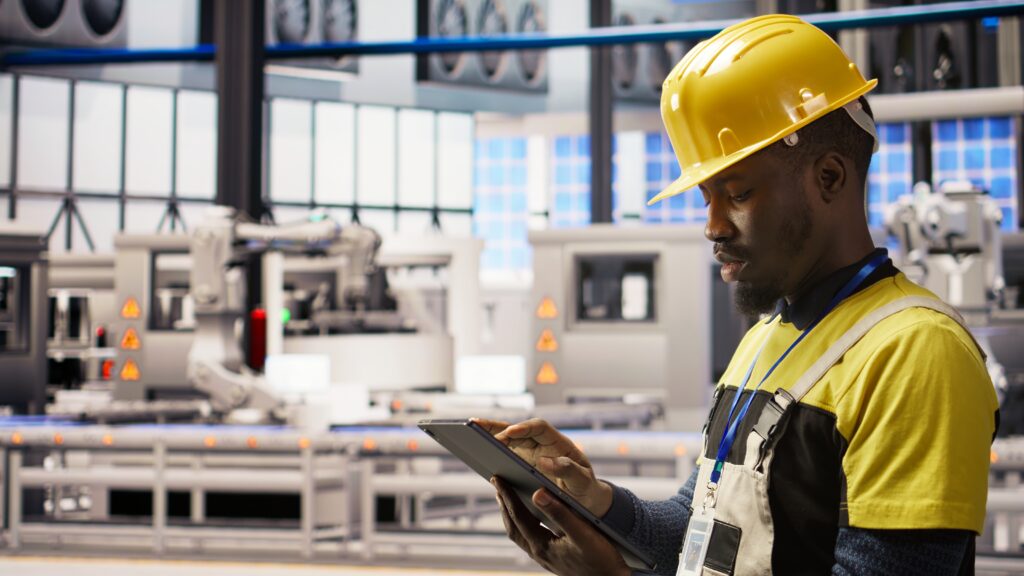
What Robust Offline Capability Looks Like in the Field
A successful field inspection workflow begins long before the inspector enters a signal-dead zone.
In a properly designed solution, mobile forms, historical records, asset IDs, and permissions are preloaded onto the smartphone or tablet, with logic intact. As the inspection unfolds, the inspection software enables progression, photo capture, task assignment, and scoring with full traceability. Issues or omissions are flagged immediately, not hours later during sync.
Once reconnected, the system syncs in a deterministic, conflict-aware, and user-friendly manner. No silent overwrites. No duplicate records. No guesswork.
Certainty ensures that inspectors never have to wonder whether their work is saved, whether the photo was attached, or whether the task was recorded. They simply conduct inspections confidently, efficiently, and accurately.
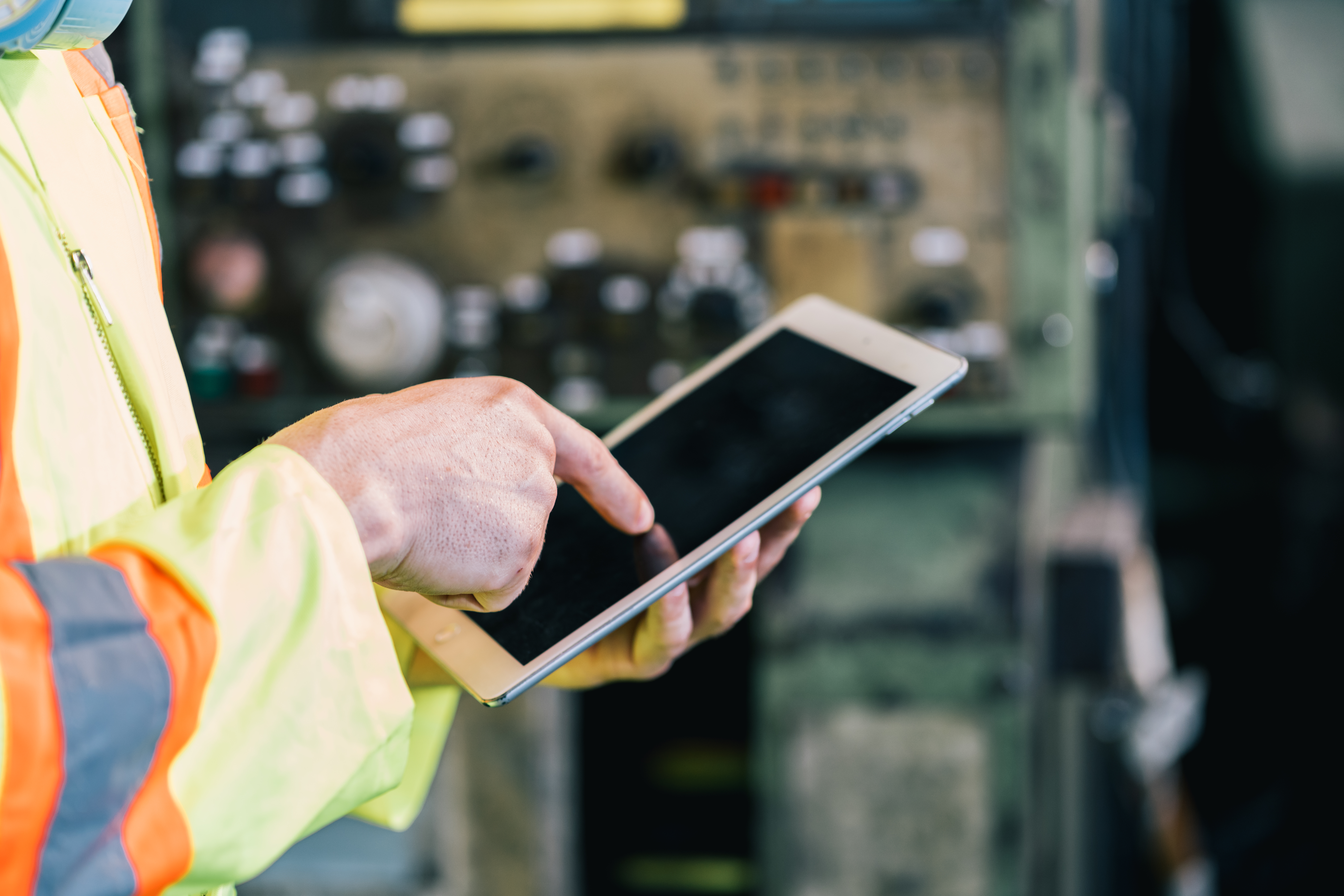
Discover what true inspection freedom looks like
See why field inspection teams trust Certainty to improve compliance and performance, no matter where their data is collected.
How Certainty Seamlessly Solves Offline Inspection Challenges
Certainty was architected to support field service teams and audit professionals in offline, high-consequence environments. Its mobile application provides full fidelity in disconnected conditions, without compromising workflow or data quality.
- Dynamic Checklists That Function Anywhere: Certainty replicates inspection logic, validations, and scoring structures that hold up in offline mode.
- Reliable Data Entry and Local Sync Queues: All entries are securely stored with full metadata such as timestamps, GPS (where enabled), and form versions until the sync completes.
- Offline Corrective Action Assignment: Non-conformances trigger follow-ups that can be created, assigned, and tracked, whether or not a connection exists.
- Sync Designed for Accuracy: Certainty uses structured conflict resolution, audit trail preservation, and built-in notifications to give teams confidence that nothing is lost or overwritten.
Whether deployed on Android or iOS, Certainty’s app empowers teams to optimize field service inspections, improve data accuracy, and eliminate the friction of paper-based processes.
In the Real World, Offline Isn’t Optional
Inspections don’t wait for a strong signal. They happen where compliance lives, whether that be at remote supplier sites, underground power rooms, outdoor processing units, or across multi-acre logistics yards.
To succeed in these settings, organizations need inspection software built not just for efficiency, but for resilience. Certainty provides that resilience through seamless offline capabilities, real-time synchronization, and a mobile-first design that empowers frontline inspectors, wherever they are.
Because in the field, being offline shouldn’t mean falling off track.
If you’d like to learn more about how to achieve true offline inspection success, schedule a demo with us today for a quick chat.
More Helpful Articles
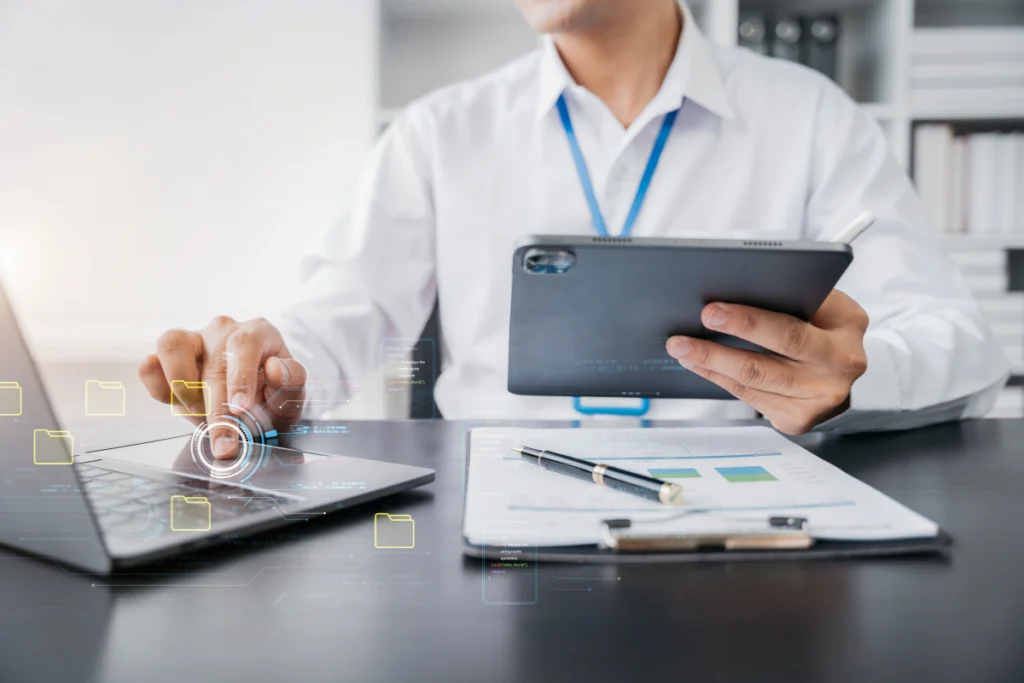
Supplier Due Diligence
How Can You Trust Compliance Data from Your Suppliers?
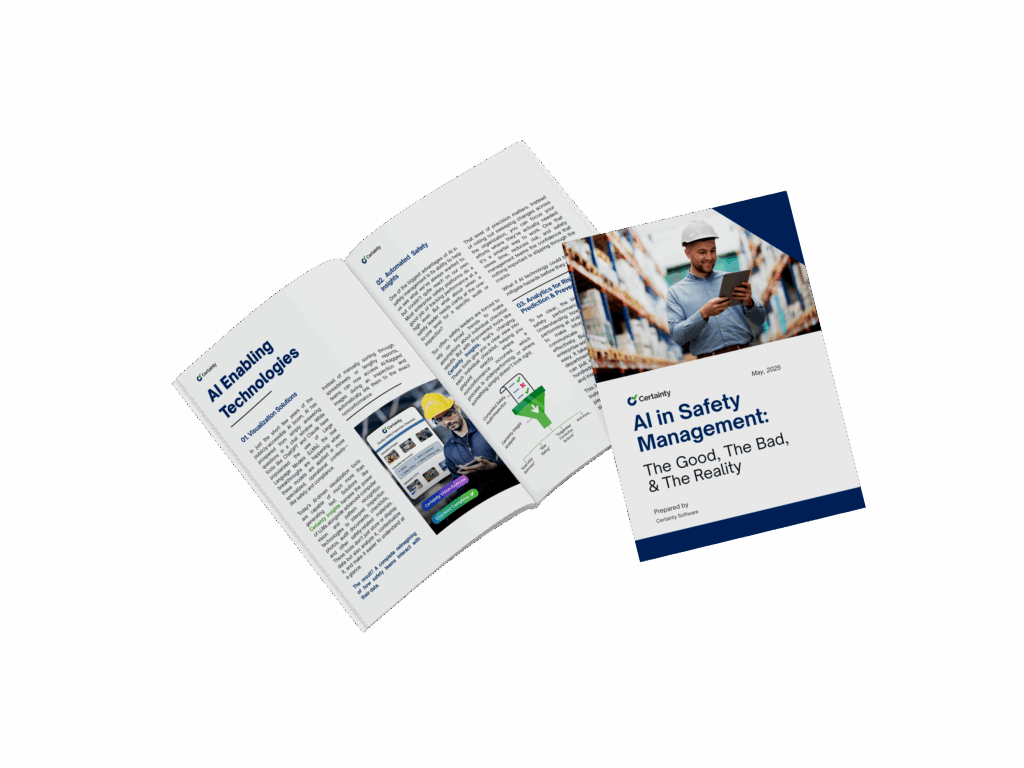
Safety Management
8 Critical Hurdles to AI in Safety Management
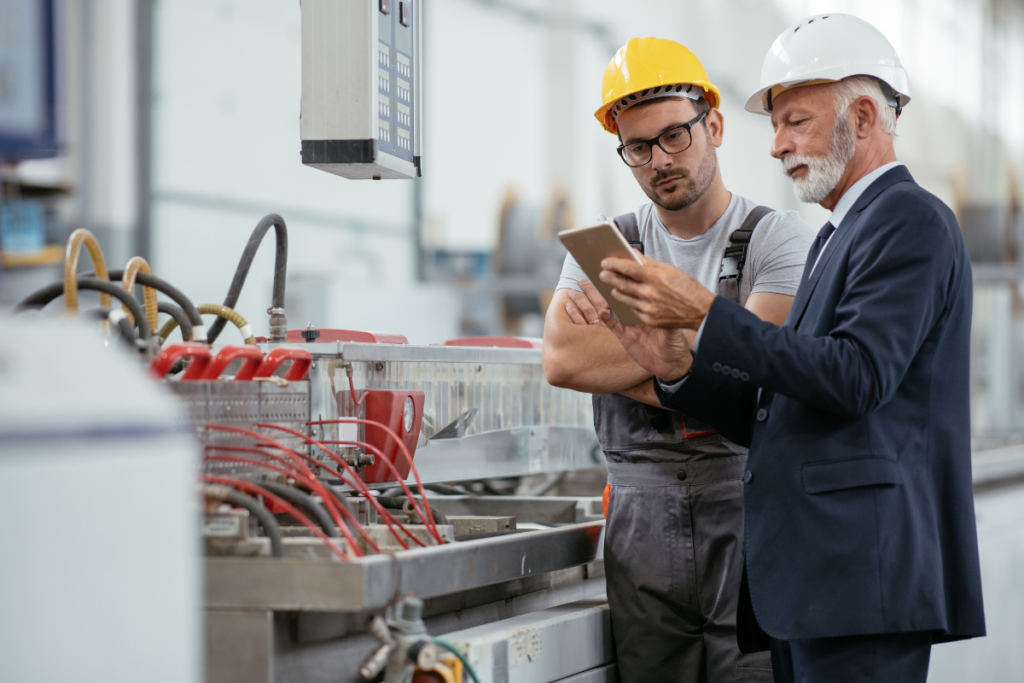
Quality Management