Table of contents
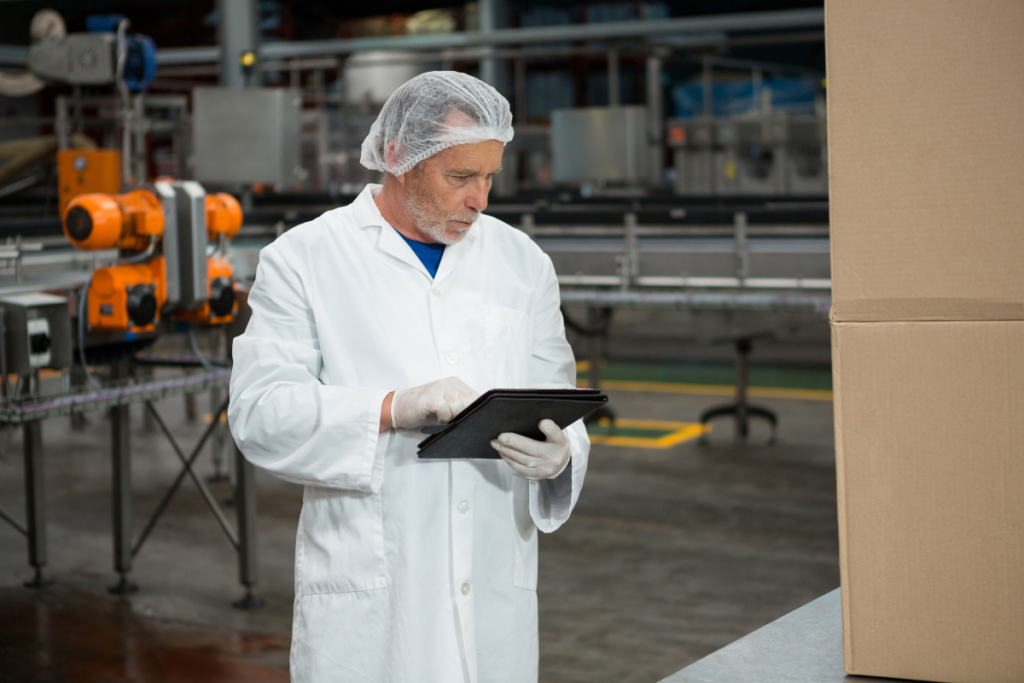
Layered Process Auditing (LPA) is a quality management technique that helps organizations ensure that their processes are followed correctly and consistently. By performing audits at different levels of management, LPAs can help organizations reduce rework, improve process control, and identify and prevent quality issues before they reach the customer, ultimately improving customer satisfaction. To make the most of LPA, it’s important to have the right tool in place. With so many options available, it can be difficult to know where to start.
In this blog post, we’ll discuss the top 10 things to consider when selecting a Layered Process Audit Tool.
How Does a Layered Process Audit Tool Work?
Layered process audit tools are designed to help organizations perform layered process audits in a more streamlined and efficient manner. These tools typically use a cloud-based software platform that can be accessed from anywhere, making it easy for multiple teams and locations to collaborate on the auditing process.
The software typically provides a pre-defined audit template that is customizable to the specific needs of the organization. This template will include a series of questions that must be answered during the audit process, covering different areas of the manufacturing process. The questions may be focused on things like equipment calibration, training requirements, or standard operating procedures.
During the audit, the auditor will answer each question and indicate whether the process is compliant or non-compliant. If non-compliance is identified, the auditor will be prompted to provide additional information on the issue and suggest a corrective action plan.
The software will then compile all of the data collected during the audit and provide real-time analytics and reports that can be used to track process improvement over time. This data can help organizations identify areas for improvement and take corrective action to prevent quality issues from occurring in the future.
What are the benefits of using a Layered Process Audit Tool?
Layered Process Auditing is a proactive approach to quality management. By using an LPA tool, you can get the following benefits:
- Improve Process Control: With real-time data, LPA tools can help you identify non-conformances in your manufacturing process and take corrective action before they cause problems.
- Drive Continuous Improvement: LPA tools help you to identify issues and track metrics so you can continually improve your processes.
- Save Time and Money: LPA tools can help you identify areas of rework, reducing the cost of wasted time and materials.
- Increase Customer Satisfaction: By catching issues before they become customer complaints, LPA tools can help you maintain high levels of customer satisfaction.
- Ensure Compliance: LPA tools can help you ensure that your processes meet ISO and other quality standards.
What are the Key Considerations When Selecting a Layered Process Audit Tool?
When choosing an LPA tool, there are ten key considerations to keep in mind to ensure optimal outcomes:
Ease of Use
User-friendliness is a key factor for the tool, with a clear process audit checklist and template that requires minimal training for shop floor workers, plant managers, and other levels of management.
Customization
Flexibility is crucial, and the tool should be customizable to meet the specific needs of your organization. It should allow you to add inputs and audit questions, and create a control plan tailored to your manufacturing process.
Real-time Data
Instant data and notifications are vital. The tool should provide real-time data, allowing you to identify high-risk areas and take immediate corrective action.
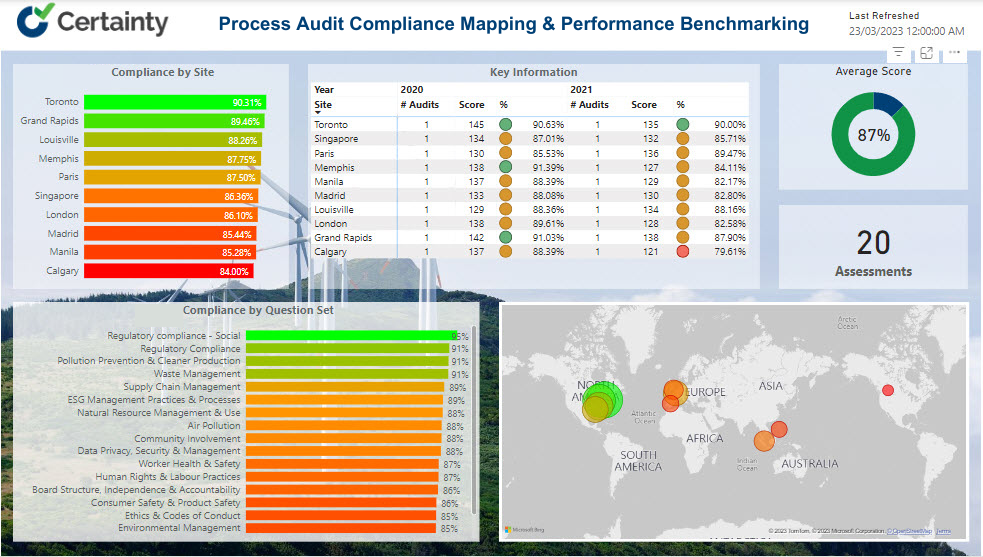
Follow-up and Reporting
Easy follow-up on non-conformances and clear reporting on corrective actions taken are essential. It should also provide dashboards and reports to track process improvement over time.
Mitigation and Root Cause Analysis
The tool should help identify the root cause of quality issues and providing guidance on problem-solving and mitigation.
LPA Software Integrations
Integration with other quality management tools, such as FMEA and your quality management system, is important. This will help ensure that your LPA program is integrated into your overall quality strategy.
High Frequency
The tool should support high-frequency LPA audits, ensuring that your processes are audited regularly and consistently.
Security and Privacy
Security and privacy are paramount. The tool should be secure, with safeguards to protect personal data, and allow you to control access levels for different users.
Rollout and Training
Proper training and support are crucial to a successful rollout. The tool should provide ongoing support to ensure that your LPA program continues to be effective.
LPA Program Development
The tool should provide guidance and support for developing an effective LPA program. This should include check sheets, templates, and best practices for conducting LPA audits.
Examples of Layered Process Audit Tool Implementation
Let’s highlight some examples of the different industries that would benefit from implementing layered process audit tools and how they can use them to improve their processes and outcomes.
Manufacturing
With LPA tools, manufacturers can create and assign audit checklists, schedule, and track audits, collect and analyze audit data, generate reports and dashboards, and initiate corrective actions. These features can help improve product quality, reduce waste, and ensure compliance with regulations and customer requirements.
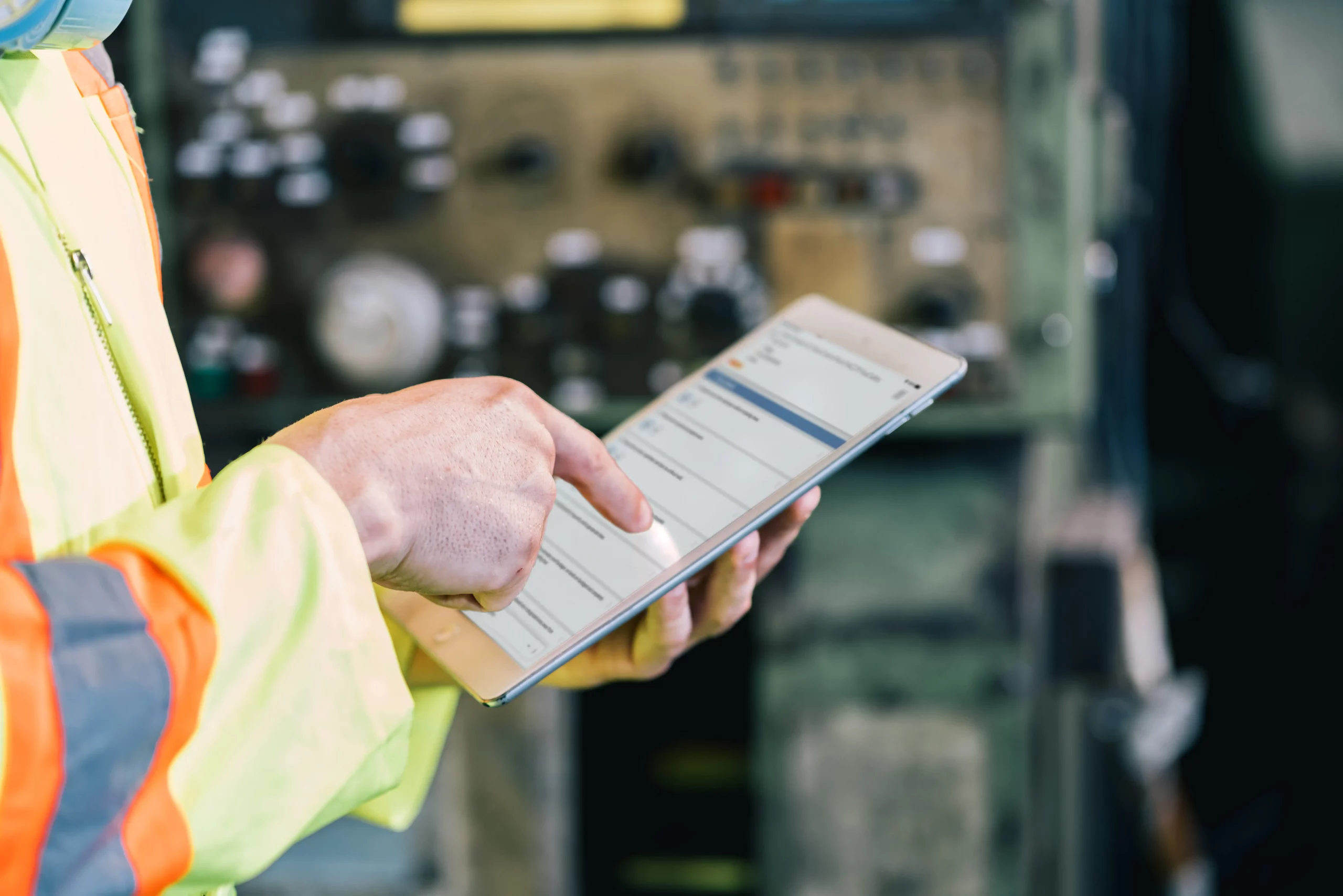
30+ Audit and inspection checklists free for download.
Healthcare
Creating and assigning audit checklists, scheduling and tracking audits, collecting and analyzing audit data, generating reports and dashboards, and initiating corrective actions are some of the functions that LPA tools enable healthcare providers to perform. These functions can help improve patient safety, quality of care, and infection prevention.
Aerospace
By using LPA tools, aerospace companies can ensure that their products meet the highest standards of safety, reliability, and performance. LPA tools allow them to create and assign audit checklists, schedule, and track audits, collect and analyze audit data, generate reports and dashboards, and initiate corrective actions. These features can also help them comply with the rigorous standards and regulations of the aerospace industry.
Automotive
LPA tools help automotive companies improve their product quality, reliability, and customer satisfaction. LPA tools allow them to create and assign audit checklists, schedule, and track audits, collect and analyze audit data, generate reports and dashboards, and initiate corrective actions. These features can also help them reduce warranty claims, recalls, and rework costs.
Construction
Ensuring project quality, timeliness, budgeting, and safety are some of the benefits that LPA tools offer to construction companies. LPA tools help them to create and assign audit checklists, schedule, and track audits, collect and analyze audit data, generate reports and dashboards, and initiate corrective actions. These features can also help them prevent accidents, injuries, and damages.
How Certainty Improves Layered Process Audit Performance
Certainty is a user-friendly, comprehensive solution with many quality audit features to help organizations like yours perform high-quality LPA audits. The tool provides you with customizable audit checklists, real-time notifications, dashboards, and metrics to monitor processes. The follow-up mechanism ensures the timely closure of non-conformances with quick and effective action management and delegation.
You may also be interested in: