Table of contents
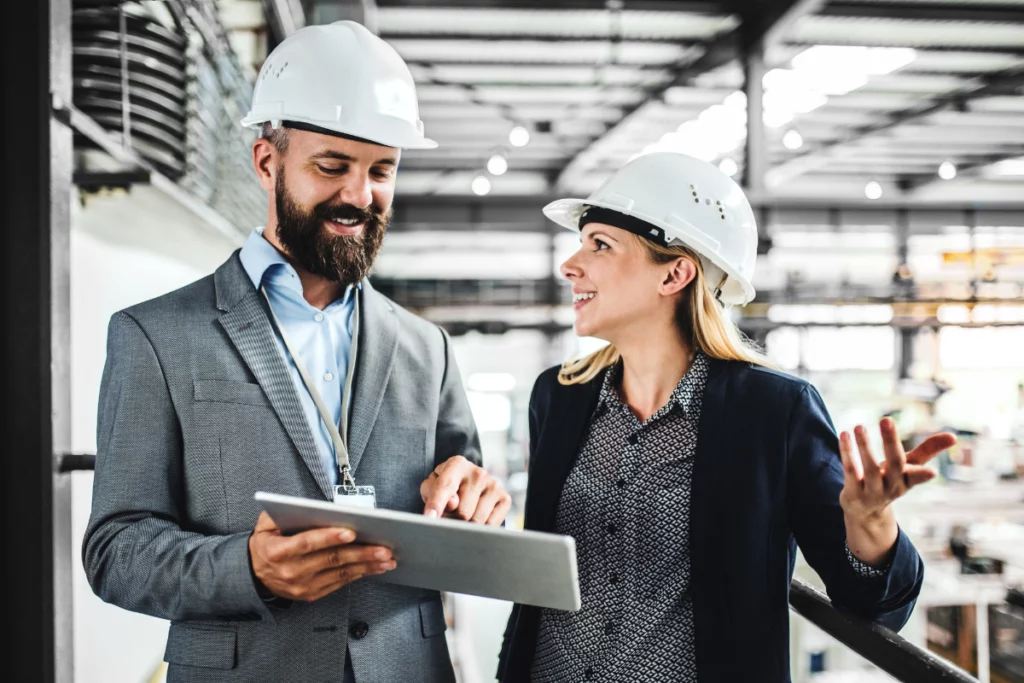
Challenges and barriers are a natural part of the journey in the dynamic world of modern business. The need for corrective actions may suddenly become necessary when navigating the complex web of supply chains, guaranteeing the highest quality in your goods and services, protecting workplace safety, ensuring compliance with environmental, social, and governance (ESG) standards, or maximizing operational effectiveness. When unforeseen storms threaten to throw you off course, these steps will serve as the compass that helps you navigate your ship back on course.
In this blog article, we will examine a few hypothetical scenarios and their sufficient Corrective Action Examples that show the necessity of taking corrective action in several business areas. We’ll also talk about potential tactics and methods that could be used to stop or lessen the consequences of these hypothetical outcomes.
What is a Corrective Action?
Let’s develop a clear knowledge of what a Corrective Action is and its function in the corporate world before we go into our hypothetical scenarios.
Defining Corrective Action
Corrective Action (CA) is a structured strategy used by businesses to detect, investigate, and resolve issues or challenges that may develop throughout their operations. It is a methodical approach to correcting violations from defined standards, quality benchmarks, or compliance criteria.
The Purpose of Corrective Action
Corrective Actions serve two primary purposes:
- Resolution: They deal with urgent problems while locating and fixing their underlying causes to stop recurrence.
- Prevention: Corrective measures go beyond addressing immediate issues. To avoid such problems in the future, they seek to improve processes and systems.
The Role of Corrective Action Plans (CAPs)
The Corrective Action process must include a Corrective Action Plan (CAP). It offers a well-organized road map describing the precise actions, liabilities, due dates, and resources needed to address and resolve identified problems.
Now, let’s dive into some Corrective Action Examples.
Corrective Action Example 1: Preventing Workplace Accidents
Scenario
A manufacturing organization has seen an upsurge in workplace accidents as a result of insufficient safety protocols. Electric shocks, wounds, burns, and slips and falls are a few of the accidents. Injuries, absenteeism, litigation, and penalties have all been caused by these mishaps.
Corrective Actions
The business could take several corrective measures to strengthen its safety culture and stop further incidents, like:
- Conduct safety training programs for all workers to inform them about potential risks and hazards in the workplace and how to deal with or avoid them.
- Perform routine hazard assessments and audits to find and get rid of any harmful working circumstances or methods.
- Improve the tools and equipment for employee safety, such as protective gear, gloves, goggles, helmets, fire extinguishers, etc.
- Create a safety committee and a reporting mechanism to facilitate employee input on safety-related issues and worries.
- Review and revise the safety policies and practices to make sure they are complete, understandable, and compliant with the necessary laws.
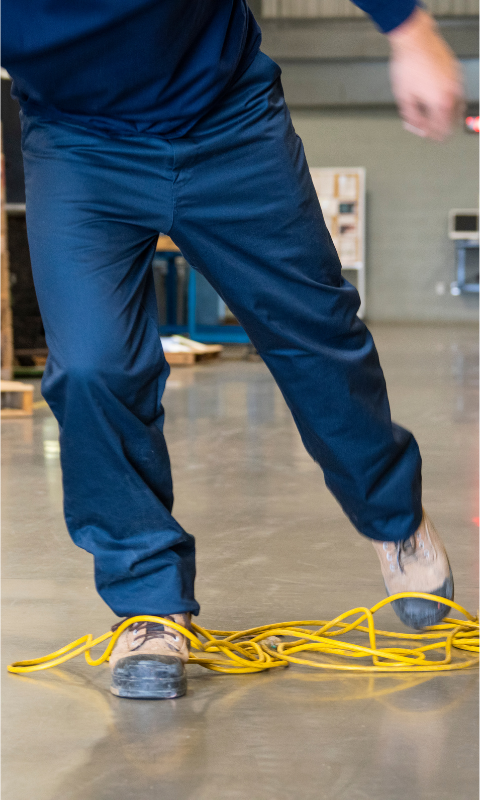
Implementation Tips
A template for a corrective action plan could be used by the business to communicate and record its safety improvement initiatives. The model can include:
- The problem or nonconformity’s description (such as a rise in workplace accidents)
- The investigation of the issue’s or nonconformity’s core causes, such as insufficient safety precautions,
- The remedial action steps (such as hazard assessments, safety training programs, etc.)
- The team members who are accountable (such as the safety manager, trainers, auditors, etc.)
- The necessary resources (such as funds, manpower, and other resources)
- The anticipated results (such as fewer accidents, a better safety culture, etc.)
- The means of verification (such as examinations, exams, surveys, etc.)
- The subsequent steps, such as monitoring, reporting, reviewing, etc.
Corrective Action Example 2: Addressing Product Defects
Scenario
One of a food processing company’s well-known products, a ready-to-eat salad, has reoccurring quality flaws. The flaws include rotten dressing, wilted lettuce, strange objects, and inaccurate labeling. Customer complaints, returns, refunds, and reputational harm have all resulted from these flaws.
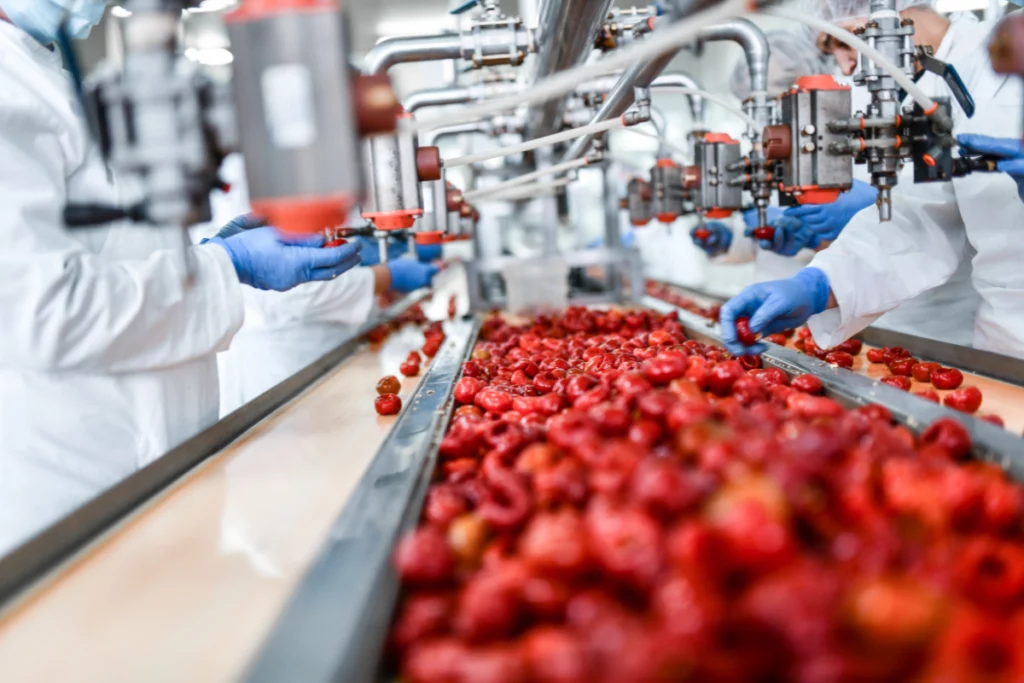
Corrective Actions
To address the quality issues and win back the customers’ trust, the business could implement a number of corrective measures, including:
- Streamlining the manufacturing process to guarantee precision and uniformity at every stage, from choosing raw materials through packing and labeling.
- Putting in place quality control measures including internal audits, tests, sampling, and inspections to find and fix any flaws before they reach the customers.
- Incorporating consumer feedback into the process of product development and improvement to better understand and satisfy customers’ wants and expectations.
- Transparently informing the clients of the quality problems and the steps being taken to fix them. This can entail sending out necessary alerts, recalls, or apologies.
- Retaining the patrons’ loyalty and happiness through providing rewards or payments.
Implementation Tips
A quality management system (QMS) could be used by the organization to streamline its remedial activities. A QMS is a collection of guidelines, practices, and resources that aid an organization in achieving its quality goals and benchmarks. A QMS could consist of:
- A quality policy that defines the company’s vision, mission, values, and goals regarding quality.
- A quality manual that documents the company’s quality system, including its scope, structure, roles, responsibilities, and processes.
- A quality plan that outlines the specific actions, resources, timelines, and metrics for achieving the quality objectives and standards.
- A quality record that tracks and records the results of the quality activities, such as data, reports, documents, etc.
- A quality audit that evaluates the effectiveness and compliance of the quality system and identifies any gaps or opportunities for improvement.
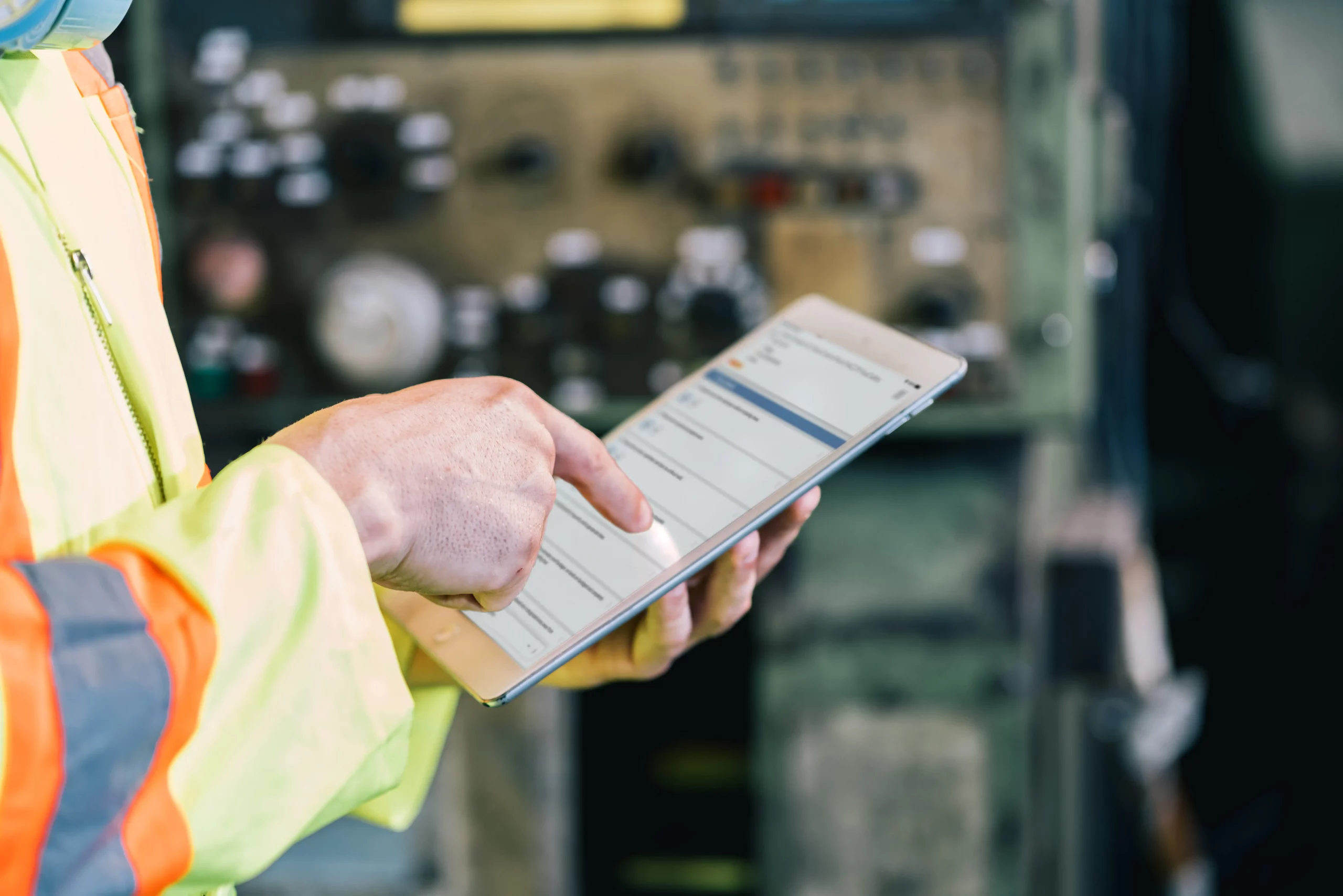
30+ Audit and inspection checklists free for download.
Corrective Action Example 3: Managing Disruptions
Scenario
When a significant supplier is severely disrupted by a natural disaster, a retail chain faces a supply chain crisis. Some of the chain’s best-selling products face inventory shortages and delivery delays as a result of the disruption. This has an impact on the company’s sales, earnings, and customer service.
Corrective Actions
To handle the supply chain issue and limit its impact on business operations, the chain could take many corrective actions, such as:
- Diversifying the supplier network to reduce reliance on a single source while increasing flexibility and resilience in the event of disruptions.
- Using cloud-based platforms, artificial intelligence, or blockchain technology to improve visibility, coordination, and collaboration across supply chain participants.
- Improving inventory management by optimizing stock levels, replenishment cycles, and distribution channels utilizing data analytics, forecasting models, or inventory optimization tools.
- Proactively communicating with clients about the supply chain situation and estimated delivery timelines. This could include offering several options or solutions to satisfy their requirements or preferences.
- Negotiating better terms or conditions with suppliers to reduce the risks or losses associated with the disruption.
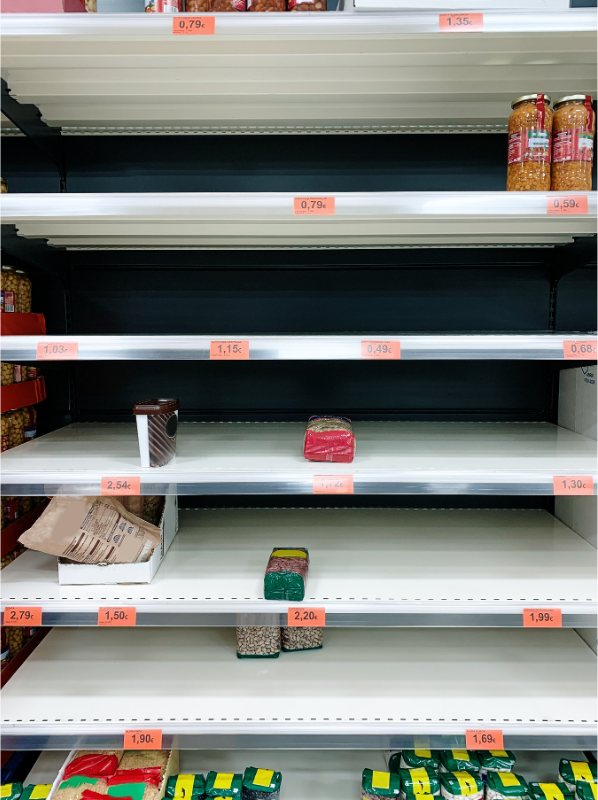
Implementation Tips
The chain might plan and carry out remedial actions using a risk-based strategy. A risk-based approach entails detecting, assessing, prioritizing, and mitigating possible threats to supply chain performance. A risk-based strategy might include:
- A technique for identifying the sources, causes, and consequences of supply chain hazards.
- A risk assessment approach that assesses the possibility and impact of supply chain risks on business goals and stakeholders.
- A risk prioritizing procedure that ranks supply chain hazards in terms of severity and immediacy.
- A risk management process that creates and implements solutions to minimize or decrease supply chain risks or the repercussions of such risks.
Corrective Action Example 4: Navigating ESG Concerns
Scenario
A production company is under fire from the public for its environmental practices and a lack of social responsibility efforts. The corporation has been accused of contributing to greenhouse gas emissions, the development of electronic waste, human rights breaches, and the digital divide. These allegations have harmed the company’s image and reputation among its stakeholders.
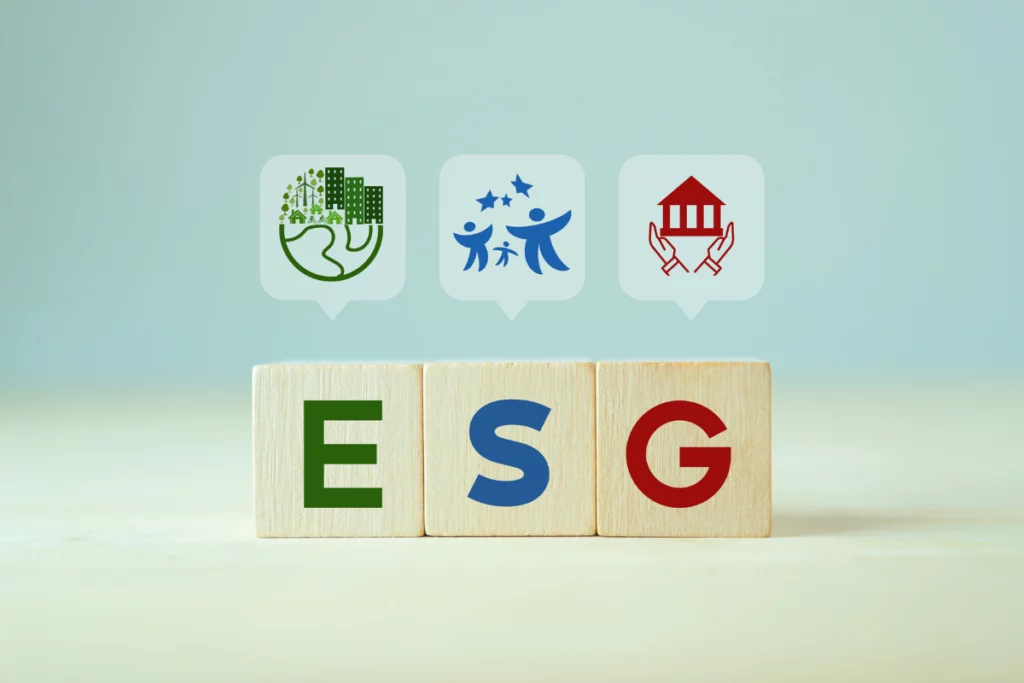
Corrective Actions
Several remedial steps could be taken by the company to align its practices with ESG (environmental, social, and governance) principles and demonstrate its commitment to ethical behavior, such as:
- Adopting green activities such as lowering energy use, using renewable energy sources, recycling products, and reducing waste output.
- Implementing social responsibility programs like community assistance, diversity and inclusion promotion, fair labor practices, and human rights protection.
- Developing governance rules and procedures to ensure accountability, openness, integrity, and adherence to applicable laws and regulations.
- Engaging with stakeholders such as customers, employees, investors, regulators, and the media to communicate the company’s ESG values, goals, and actions and solicit feedback and suggestions.
Implementation Tips
To facilitate corrective measures, the organization could employ a corrective and preventative action (CAPA) system. A CAPA system is a procedure that assists a company in identifying, correcting, and preventing faults or nonconformities that have an impact on its quality or performance. A CAPA system could include the following components:
- A CAPA request initiates the CAPA process by documenting the problem or nonconformity, its source, and its impact.
- A CAPA investigation analyzes the root cause of the problem or nonconformity and identifies the corrective actions needed to resolve it.
- A CAPA implementation that executes the corrective actions and verifies their effectiveness and compliance.
- A CAPA closure that documents the results of the corrective actions and evaluates their sustainability and improvement.
- A CAPA review that monitors the corrective actions and identifies any potential problems or opportunities for enhancement.
Corrective Action Example 5: Preventing Employee Injuries
Scenario
Employee injuries and pain are on the rise in warehousing facilities due to poor workplace ergonomics. Back discomfort and neck strain. These injuries harm the employee’s health, well-being, and productivity.
Corrective Actions
The organization could implement several corrective actions to improve its workplace ergonomics and prevent employee injuries, such as:
- Begin ergonomic assessments for the warehouse environment. These evaluations should thoroughly check the suitability and comfort of employees’ workstations, shelves, and equipment.
- Invest in ergonomic solutions tailored to warehouse personnel. Adjustable workstations, conveyor belts, lifting aids, and safety equipment may be included to give ideal support for employees’ posture and movements while performing jobs like as lifting, packing, and stocking.
- Educate staff on how to fit their workstations with warehouse tasks, maintain optimal posture while lifting and stacking, and develop healthy habits appropriate to their roles.
- Introduce safety equipment that addresses ergonomic concerns in the warehouse, such as back braces, anti-fatigue mats, and ergonomic hand tools.
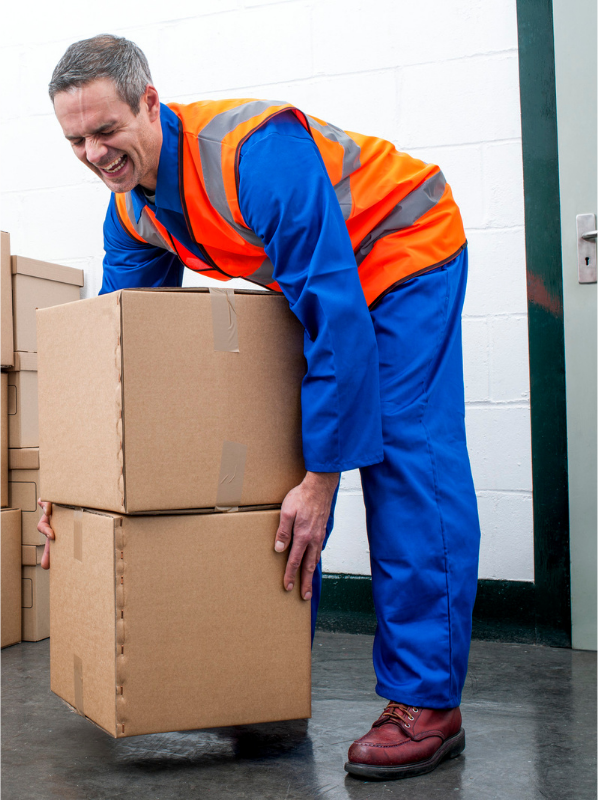
Implementation Tips
To plan and carry out corrective actions, the business could employ a problem-solving strategy. A problem-solving strategy entails defining, analyzing, solving, and assessing a problem or issue. A problem-solving strategy might include:
- A procedure for defining a problem or issue that defines its nature, extent, and impact.
- A procedure for identifying the causes, impacts, and stakeholders of a problem or issue.
- A problem-solving process that creates and selects solutions based on factors such as feasibility, effectiveness, cost-benefit analysis, and so on.
- A problem evaluation procedure that examines and confirms problem or issue solutions and measures their outcomes.
Preventative Actions and the Role of Certainty Software
We’ve seen the potential of proactive problem-solving throughout this journey of analyzing hypothetical Corrective Action Examples. While Corrective Actions are important in resolving issues for existing problems, there is an even more effective strategy—Preventative Actions.
Preventative Actions are proactive steps taken to avoid the need for the Corrective Action Examples we provided in the first place. Businesses can maintain smoother operations, improve product and service quality, and ensure workplace safety by detecting and reducing possible risks and obstacles before they become problems. Preventative Actions enable businesses to stay ahead of the curve, ensuring that they are not just responsive but also capable of preventing problems before they occur.
Certainty Software: Your Partner in Excellence
Certainty Software emerges as a valued ally in the pursuit of both Corrective and Preventative Actions. Our adaptable software solution provides a comprehensive array of conformance tools that enable firms in a variety of industries to streamline their safety, quality, compliance, and risk management operations.
- Corrective Actions: Certainty Software enables you to respond to issues as they arise in a timely and effective manner. It makes it easier to create Corrective Action Plans, allocate tasks, track progress, follow up, and guarantee that critical measures are executed as soon as possible. With Certainty Software, you can turn obstacles into opportunities for growth.
- Preventative Actions: In addition to remedial actions, Certainty Software enables enterprises to proactively identify and minimize prospective problems. Businesses can implement preventative steps to reduce the root causes of problems before they occur by employing advanced analytics, predictive insights, and data-driven decision-making.
We hope that the Corrective Action examples we provided will support your efforts to improve performance at your workplace. While these Corrective Action examples are detailed, there are still many other actions that your organization can take. It’s important to understand the uniqueness of your workplace and to adjust your actions that will best fit the success of your workflows.
If you’re interested in learning more about how Certainty Software can improve your preventative and corrective action management, book a quick demo here.
You might also be interested in: