Kellogg’s is a $14 billion company and is the world’s largest cereal company, the second largest producer of crackers and savory snacks, and a leading North American frozen foods company. In total, Kellogg’s produces more than 1,600 types of foods, works with dozens of suppliers, and is involved in several charities.

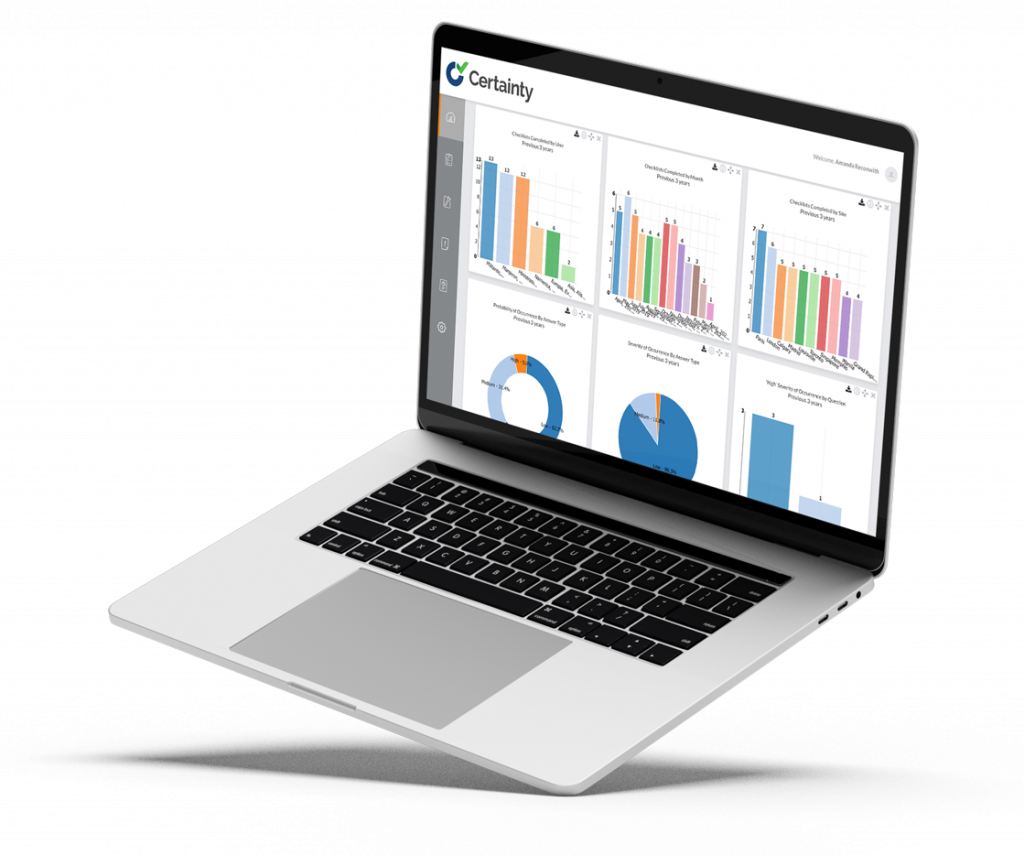
The Challenge
The Kellogg Company conducts regular behavioural-based Environmental Health and Safety (EHS) observations in more than 100 sales, distribution and manufacturing facilities globally. They used paper checklists to make it easy for employees, but faced a number of problems with this approach.
Before introducing Certainty Software, data was siloed within the sites and the business struggled to aggregate and report safety and environmental data globally. What’s more, data had to be entered into spread sheets manually which was inefficient and more prone to human error. For one observation system they had to invest in proprietary scanners at each site; and, they were locked into printing their checklists with their original scanning solution provider which was two to three times the price of normal printing.
The Solution & Result
After learning about Certainty Software, Kellogg’s implemented the tool to develop more robust observation system to meet the needs of each site.
Since implementing the solution, Kellogg’s has been able to utilize the site’s existing scanners and not rely on costly proprietary scanners. This has saved a significant amount of money for the business. To get data into the system, employees simply have to bulk scan completed checklists using existing copier “scan to email” functionality and the data is automatically populated into Certainty. Whereas previously a third party consultant was paid to collect their data globally and provide it in a format that allowed for corporate wide reporting, each site can now scan their completed cards, enabling each site to own and utilize their data.
Instead of waiting days or weeks to see observation data after cards are scanned, the sites’ automatically scanned cards now go into Certainty Software and they can see the results. Before data was stored at the site level and reporting capability was extremely limited.
Now they can easily create their own reports, and slice and dice their data to meet business needs. What’s more, each Kellogg’s site can design and create their own checklists and print directly from the system, which dramatically speeds up the process and saves significant printing and delivery costs.This results in a smoother workflow while reducing the overhead cost, improving the performance and boosting the bottom line.
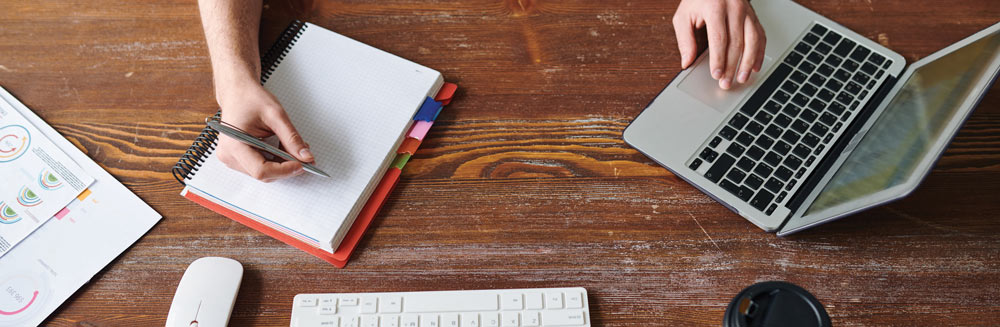